It is very important to know how strong is your welded joint. You have to know how good is your welded joint. Otherwise, the weldment may fail and you will be in big trouble. To make sure if the welding joint is capable of having enough strength to withstand your applied load you have to calculate welding joint strength. Let us do it by identifying the type of welding you made and the type of load it is experiencing.
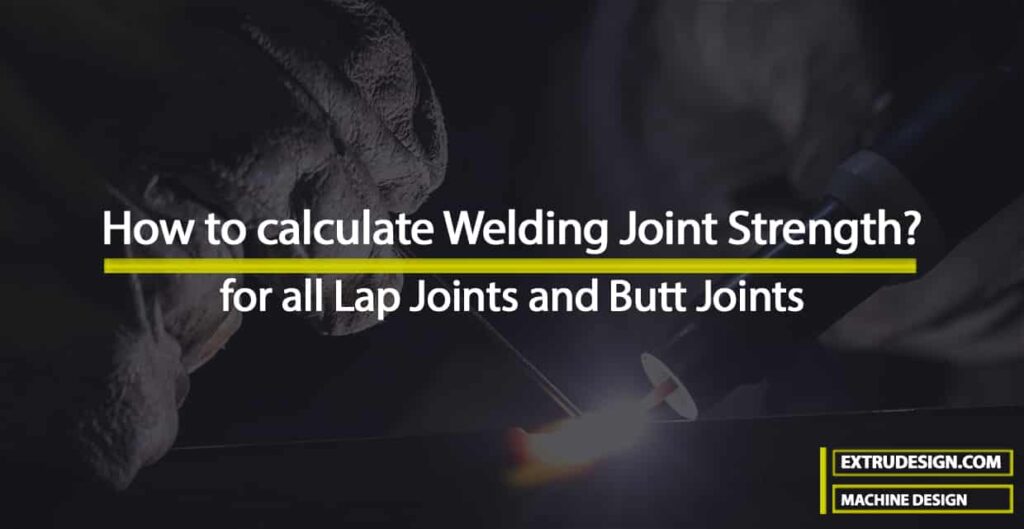
Type of Welding joints
Basically, the welding joining types are grouped into two types
- Lap Joint
- Butt Joint
There may be further classification in these two groups of welding joints. let us discuss them each.
Lap Joint
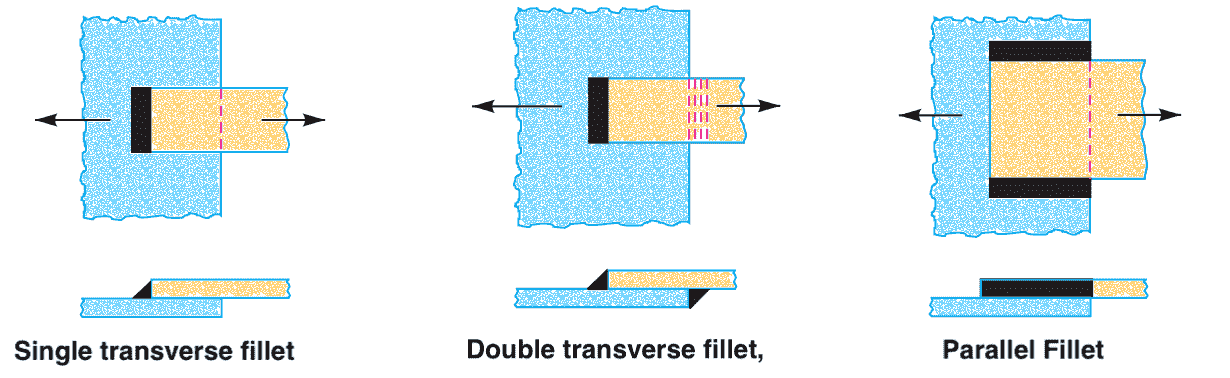
A lap joint can be made when two plates need to be welded then they will be welded by overlapping one on another. the welding is done at the edges of the two plates. now if the welding is done on one edge it is called the Single transverse fillet, similarly, the welding is done on the two end edges then it is called the Double transverse fillet, if the two weldings are done on the same side with one pate then it is called the Parallel fillet joints. These 3 types of lap joint welding are illustrated in the above picture.
Butt Joint
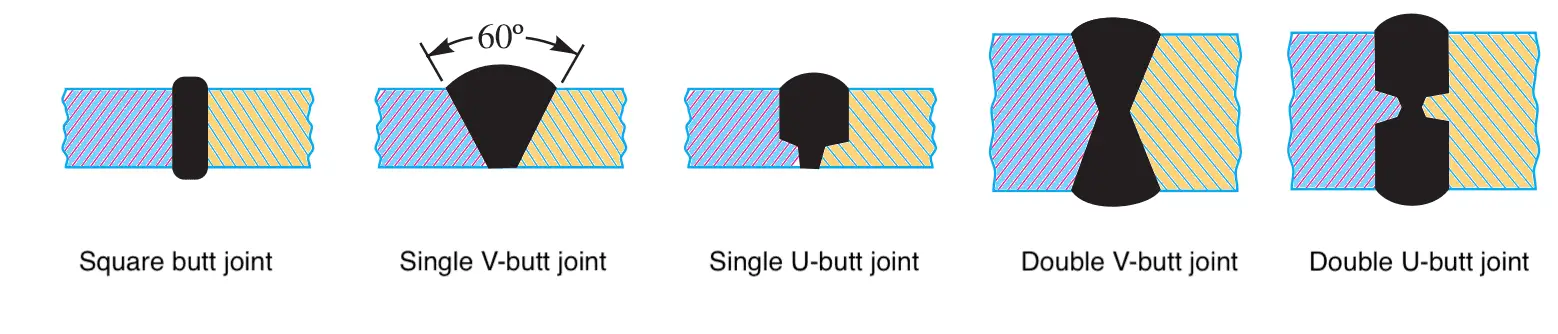
The butt joint can be made by placing the edge of the two plates to the edge as shown in the above figure. for the plates of 5mm or less thickness, we do not need to bevel. if the thickness is more than 5mm and less than 12.5mm then the edges should be beveled to V or U-groove on both sides to add the filler material. based on this beveling of the shape on the plate edges, the butt joints can be made in different ways as shown in the above representations. those are the Square butt joint, single V-butt joint, Double V-butt joint, Single U-butt joint, and Double U-butt joint.
The other types of joints available are the corner fillet joint, edge joint, and T-Joint as illustrated in the below picture.
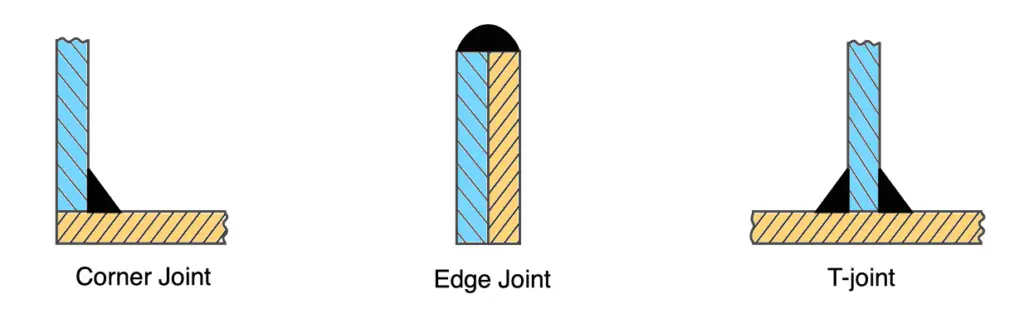
But how we can select one of these welding joint types for our applications. What factors should we consider?
- The shape of the welded component required
- The thickness of the plates to be welded
- The direction of the forces applied
These are the main considerations involved in the selection of weld types. We also discussed the different types of welding processes such as TIG welding, MIG welding, Arc welding, and Gas welding. The method of welding also needed to be selected before going to select the welding joint type.
Calculating Welding Joint Strength
For the following Welding joints, we are going to calculate the strength of the Welding Joint.
- Strength of Transverse Fillet Welded Joints
- Strength of Parallel Fillet Welded Joints
- Strength of Combination of Transverse and Parallel fillet welded joint
- Strength of Circular Fillet Weld Subjected to Torsion
- Strength of Circular Fillet Weld Subjected to Bending Moment
- Strength of Long Fillet Weld Subjected to Torsion
- Strength of Butt Joint
1. Strength of Transverse Fillet Welded Joints
The transverse Fillet joints are obtained by overlapping the two plates one on another and welding the edges of the plates. these Transverse fillers are capable of withstanding high tensile Load. Let us calculate the Welding Joint strength for the single and double transverse fillet welds as shown below figures.
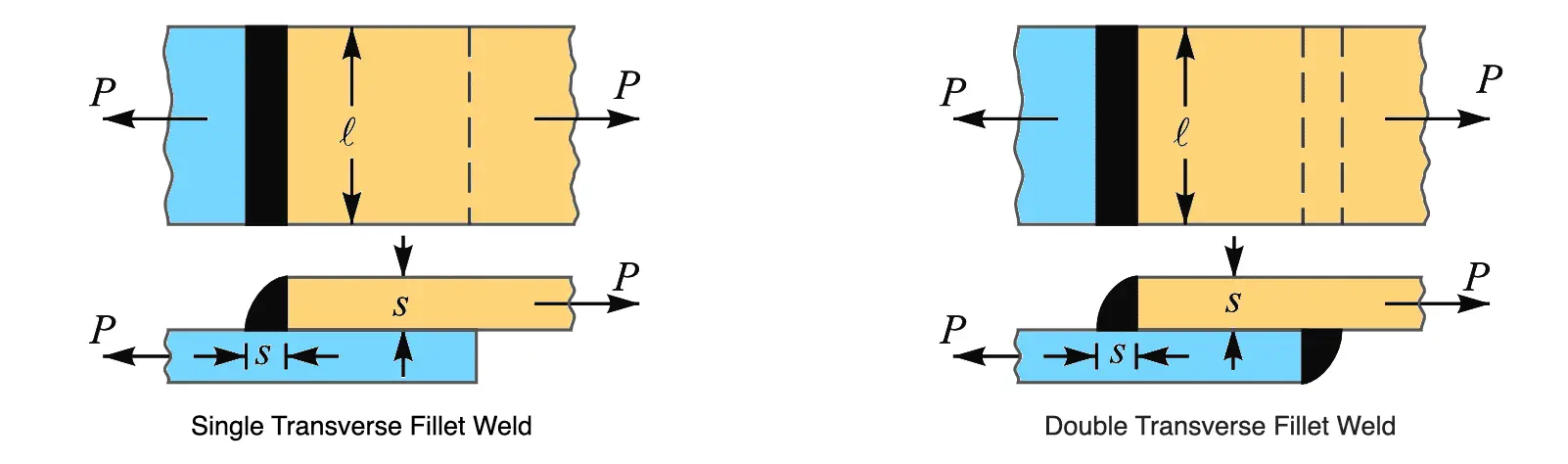
We have to assume that the fillet section is a right-angled triangle, To determine the strength of the fillet joint. In this right-angle triangle, ABC with hypotenuse AC makes equal angles with the other two sides AB and BC.
The enlarged view of the fillet is shown in the below figure. The length of each side is known as the leg or size of the weld and the perpendicular distance of the hypotenuse from the intersection of legs (i.e. BD) is known as throat thickness. The minimum area of the weld is obtained at the throat BD, which is given by the product of the throat thickness and length of the weld.
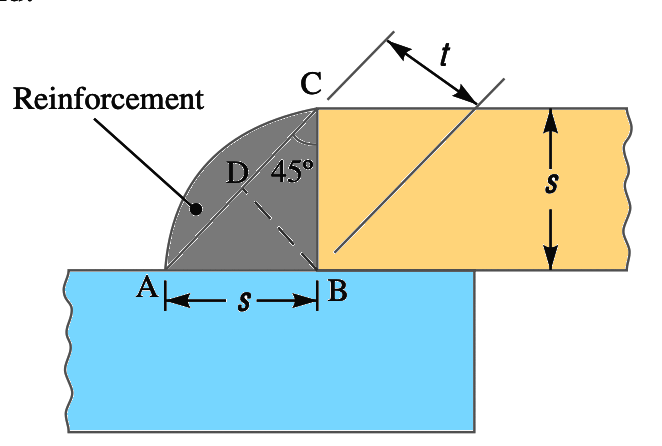
Let us consider
t = Throat thickness (BD)
s = Leg or size of weld (AB) = Thickness of plate(BC)
l = Length of weld
From the above figure, we can find that the throat thickness, t = s × sin 45° = 0.707 s
Now we need to calculate the maximum area of the weld. We have to consider the minimum area of the weld because the stress is maximum at the minimum area.
The minimum area of the weld or throat area, A = Throat thickness × Length of weld
A = t × l = 0.707 s × l
If σt is the allowable tensile stress for the weld metal, then the tensile strength of the joint for a single fillet weld can be calculated from the stress formula. (Stress =Load/Area)
Load (P) = Throat area × Allowable tensile stress
P = 0.707 s × l × σt ………………………………. Equation (1a)
This is the formula to calculate the strength of the single fillet transverse joint.
For the Double fillet transverse joint, the tensile strength can be calculated by simply doubling it,
P = 2 × 0.707 s × l × σt
P = 1.414 s × l × σt ………………………………. Equation (1b)
with this formula, we can calculate the strength of the Double fillet transverse joint.
A very important note is that the weld is weaker than the plate due to slag and blowholes, therefore the weld is given a reinforcement which may be taken as 10% of the plate thickness. For reinforced fillet welds, the throat dimension may be taken as 0.85 t.
To allow for starting and stopping of the weld bead, 12.5 mm should be added to the length of each weld obtained by the above expression.
Example Problem on Calculating Transverse fillet joint strength
A plate 100 mm wide and 5 mm thick is to be welded to another plate using double transverse fillets. The plates are subjected to a static load of 80 kN. Find the length of the weld if the permissible tensile stress in the weld does not exceed 75 MPa.
Solution:
Given data:
Width of the plate = 100 mm
Thickness (s) = 5mm (Also known as the size of the weld)
P = 80kN = 80×103 N
σt = 75 MPa = 75 N/mm2
Let l = Length of weld.
From the above equation (1b), we have P = 1.414 s × l × σt
80×103 = 1.414 × 5 × l × 75
l = (80×103) ÷ 530.25
l = 150.87
Length of the weld is 151mm
As we mentioned above to allow for starting and stopping of the weld bead, 12.5 mm should be added to the length of each weld.
So the final overall length of the weld will be 150.87+12.5 = 163.4mm
Now for each side on the plate, the single fillet length will be 81.7mm( half of the overall length) along the width of the plate 100mm to withstand the load of 80kN.
2. Strength of Parallel Fillet Welded Joints
The Strength of Parallel Fillet Welded Joints is mainly capable of withstanding the shear load. Instead of the tensile strength as we considered in the transverse fillet joint, we have to consider the shear strength of the filler material for the parallel fillet welded joint.
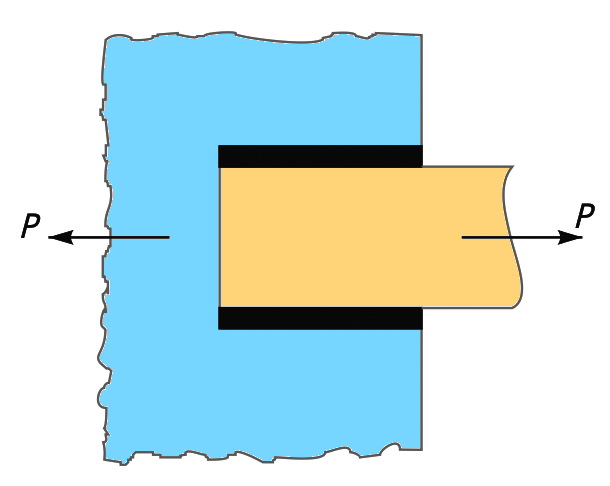
Let us consider τ is the allowable shear stress for the weld metal.
We have already discussed in the above transverse weld joint strength calculation, that the minimum area of weld or the throat area, is A = 0.707 s × l
The shear strength of the single parallel fillet joint weld will be
P = Throat area × Allowable shear stress = 0.707 s × l × τ
P = 0.707 s × l × τ
For the Double fillet parallel joint, the shear strength can be calculated by simply doubling it,
P = 2 × 0.707 × s × l × τ
P = 1.414 s × l × τ ………………………………. Equation (2)
3. Strength of Combination of Transverse and Parallel fillet welded joint
Now let us combine the transverse fillet welded joint with the parallel fillet welded joint.
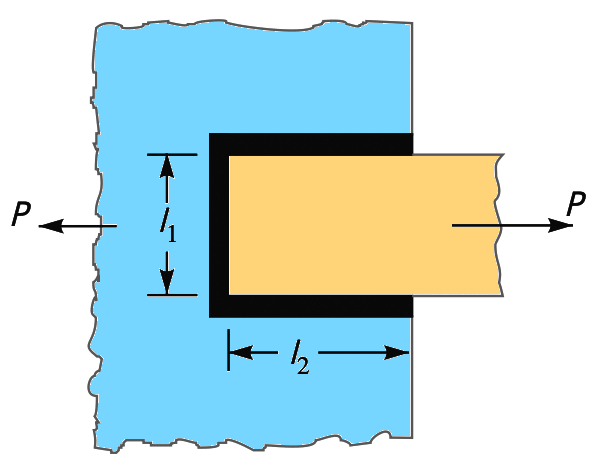
We can combine the single fillet transverse welded joint with a double fillet parallel welded joint as shown in the above figure. We already knew the formulas for the single fillet transverse welded joint and double fillet parallel welded joint. we need to simply sum it.
P = 0.707s × l1 × σt + 1.414s × l2 ×τ ………………………………. Equation (3)
Example Problem on Calculating Transverse fillet joint strength
A plate 70 mm wide and 5 mm thick is to be welded to another plate using single transverse fillets and a double fillet parallel joint. The plates are subjected to a static load of 80 kN. Find the length of the weld if the permissible tensile stress in the weld does not exceed 75 MPa and the permissible shear stress in the weld does not exceed 55 MPa.
Solution:
Given data:
Width = 70 mm
Thickness (s) = 5mm (Also known as the size of the weld)
P = 80kN = 80×103 N
σt = 75 MPa = 75 N/mm2
τ = 55 MPa = 55 N/mm2
Let l1 be the Length of a single fillet transverse weld and l2 be the double fillet parallel weld.
then From the above equation (3)
P = (0.707s × l1 × σt)+ (1.414s × l2 × τ)
80×103 = 0.707 × 5 × l1 × 75) + (1.414 × 5 × l2 × 55)
We also have the width of the plate gives us the length of the single fillet transverse weld length l1 = 70mm
80×103 = (0.707 × 5 × 70 × 75) + (1.414 × 5 × l2 × 55)
80×103 = (18558.75) + (388.86 × l2)
388.86 × l2 = 61441.25
l2 = 158mm
As we mentioned above to allow for starting and stopping of the weld bead, 12.5 mm should be added to the length of each weld.
The length of the single fillet parallel joint will be(l2) 170.5mm. this will be on each side of the plate edges.
4. Strength of Circular Fillet Weld Subjected to Torsion
In this case, a solid circular rod is going to be welded on the plate. then the welding is done around the circular edge of the rod as shown in the below figure. For this kind of welding joint, we need to calculate the weld joint strength of the solid rod is being twisted and produce torsional load.
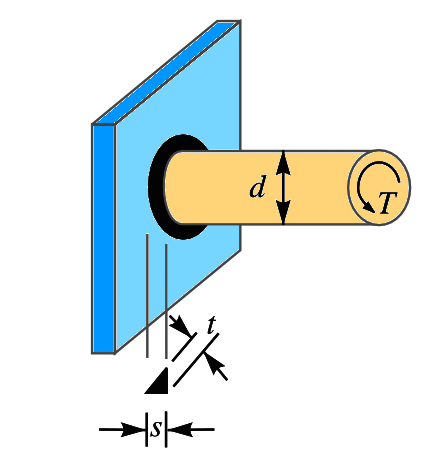
From the above figure
d = Diameter of the rod
r = Radius of the rod
T = Torque acting on the rod
s = Size (or leg) of weld
t = Throat thickness
J = Polar moment of inertia of the weld section
From the torsion equation
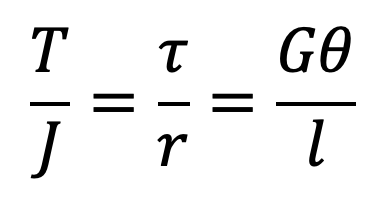
We can write the shear stress
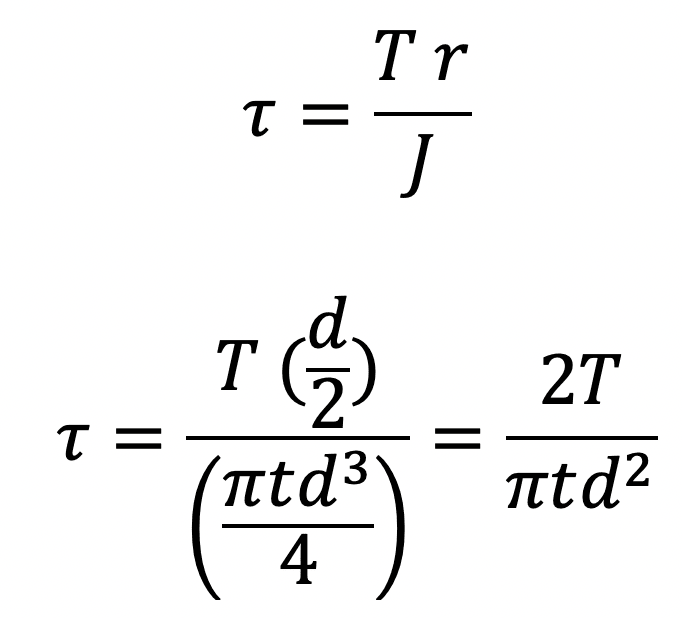
This shear stress occurs in a horizontal plane along a leg of the fillet weld. The maximum shear occurs on the throat of the weld which is inclined at 45° to the horizontal plane.
The throat thickness will be t = s sin45° = 0.707 s
then the above equation will be
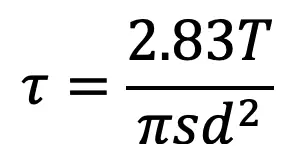
……………………………. Equation (4)
With this formula, we can calculate the allowable either torsional load (torque) or diameter of the rod with the other known parameters.
Example Problem on strength of Circular Fillet Weld Subjected to Torsion
A 50 mm diameter solid shaft is welded to a flat plate by a 10mm fillet weld. Find the maximum torque that the welded joint can sustain if the maximum shear stress intensity in the weld material is not to exceed 80 MPa.
Solution:
Given data:
d = 50mm
s = 10mm
τmax = 80MPa = 80N/mm2
T = Maximum torque that the welded joint can withstand =?
We know from. the above equation (4)
80 = (2.83 × T)÷(π ×10×502)
T = 80 × 78550/2.83
T = 2.22 × 106 N-mm
T = 2.22 kN-m ~ Answer
The weld joint can withstand up to 2.22kN-m of torque.
5. Strength of Circular Fillet Weld Subjected to Bending moment
Similar to the above welding of a circular solid rod on a plate, when the rod is subjected to the bending moment as sown in the below figure then we need to consider the section modulus of the weld section instead of the polar moment of inertia.
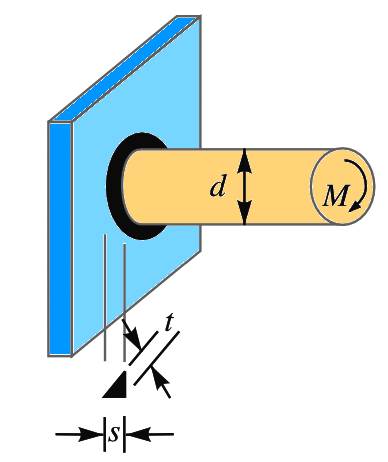
Every parameter stays the same except the section modulus(Z) instead of the polar moment of inertia and the bending moment (M) instead of the torque.
We know the bending stress σb = M/Z
σb = M/(πtd2 /4)
σb = 4M/πtd2
This bending stress occurs in a horizontal plane along a leg of the fillet weld. The maximum bending stress occurs on the throat of the weld which is inclined at 45° to the horizontal plane.
The throat thickness will be t = s sin45° = 0.707 s
then the above equation will be
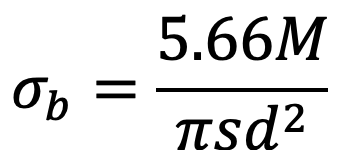
……………………………. Equation (5)
With this formula, we can calculate the allowable either bending load (moment) or diameter of the rod with the other known parameters.
6. Strength of Long Fillet Weld Subjected to Torsion
Now let us Consider a vertical plate attached to a horizontal plate by two identical fillet welds as shown in Figure.
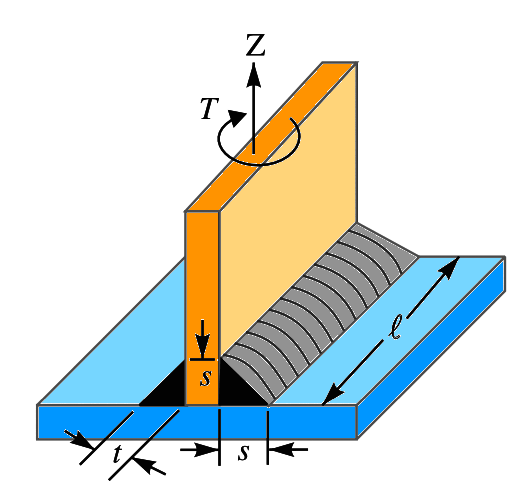
For this type of weld joint if the vertical plate is being twisted along the Z-axis at its midpoint. then we need to calculate Welding Joint Strength.
From the above figure
T = Torque acting on the vertical plate
l = Length of weld,
s = Size (or leg) of weld
t = Throat thickness
J = Polar moment of inertia of the weld section (Check here)
As we mentioned above the shaft is being twisted along the Z-axis and this rotation is resisted by the shear stress varying from zero at the Z-axis and maximum at the ends of the plate.
This variation of shearing stress is analogous to the variation of normal stress over the depth (l) of a beam subjected to pure bending.
Shear stress τ = (T × (l/2))÷(t ×(l3/6))
τ = 3T ÷ t l2
The maximum shear stress that occurs at the throat is given by
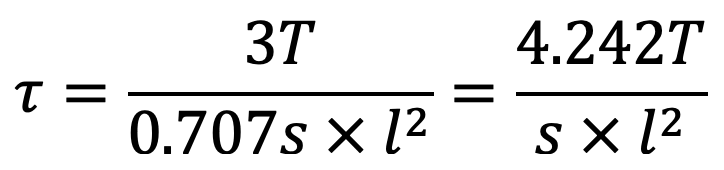
……………………………. Equation (6)
Example Problem on Strength of Long Fillet Weld Subjected to Torsion
A plate 1 m long, 60 mm thick is welded to another plate at right angles to each other by a 15mm fillet weld. Find the maximum torque that the welded joint can sustain if the permissible shear stress intensity in the weld material is not to exceed 80 MPa.
Solution:
Given Data
length of the weld l = 1m = 1000 mm
Thickness = 60 mm
s = 15mm
τmax = 80MPa = 80N/mm2
T = The Maximum torque that the welded joint can sustain =?
From the above equation (6) we know that the maximum shear stress (τmax)
τmax= (4.24 × T) ÷ (15 × 10002)
80 = 0.283 T ÷ 106
T = 283 × 106 N-mm = 283kN-m
The weld joint can withstand up to 283kN-m of torque.
7. Strength of Butt Joint
The butt-welded joint is designed for tension and compression.
Let us consider a single V-butt joint as shown in the below figure.
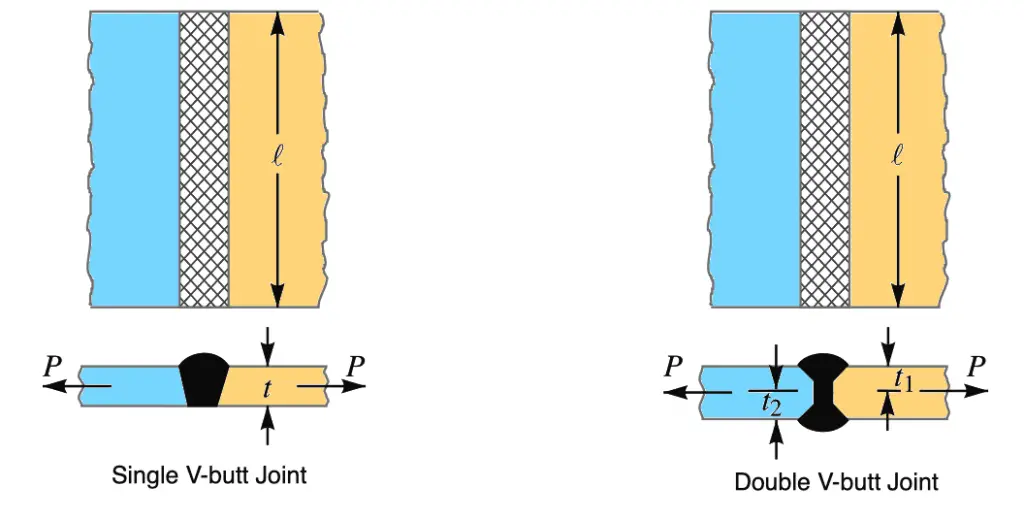
In the case of the butt joint, the length of the leg or size of the weld is equal to the throat thickness which is equal to the thickness of plates.
The tensile strength of the butt joint (single-V or square butt joint),
P = t × l × σt
where
l = Length of the weld. It is generally equal to the width of the plate.
Tensile strength for double-V butt joint as shown in the above figure(right side) is given by
P = (t1 + t2) l × σt
where
t1 = Throat thickness at the top
t2 = Throat thickness at the bottom
It is observed that the size of the weldment should be greater than the thickness of the plate, but it may be less. The following reference table shows recommended minimum size of the welds for the butt joints.
The thickness of the plate (mm) | 3-5 | 6-8 | 10-16 | 18-24 | 26-55 | over 58 |
Minimum size of the weld (mm) | 3 | 5 | 6 | 10 | 14 | 20 |
Conclusion
We have discussed different types of welds under the lap joint and butt joint. And also described how to calculate Welding Joint Strength for 7 different types of welding joints. Those are Transverse Fillet Welded Joints, Parallel Fillet Welded Joints, Combination of Transverse and Parallel fillet welded joint, Circular Fillet Weld Subjected to Torsion, Circular Fillet Weld Subjected to Bending Moment, Long Fillet Weld Subjected to Torsion and single and double V-butt Joint. Let us know what do you think about this article in the comment section below.
dear sir,
please provide us a copy in PDF format for our reference and retention,
as the following article found very useful.
How to calculate Welding Joint Strength? by ramesh
regards,
doraisubramani.
20 02 2023.
You can print this webpage as PDF and use this article link as a reference anchor: https://extrudesign.com/how-to-calculate-welding-joint-strength/
As engineers and welding enthusiasts, the extrudesign.com article on determining welding joint strength is an invaluable resource. CNC Milling Services It simplifies complicated computations by giving succinct and understandable explanations. Everyone interested in welding projects should read this.
Hello I am wondering how you would go about calculating the shear and bend capacity in a circular fillet weld that is a D shape (for attaching a chain). I assume it is not the same as a straight bar circular fillet weld.
Thanks!