We have been discussing different types of arc welding in the previous article. Yes, this MIG welding is one of the types of Arc welding. The full form of MIG welding is Metal Inert gas Welding. Let us discuss more details such as the MIG welding process, MIG welding used for which applications, and MIG welding advantages and disadvantages.
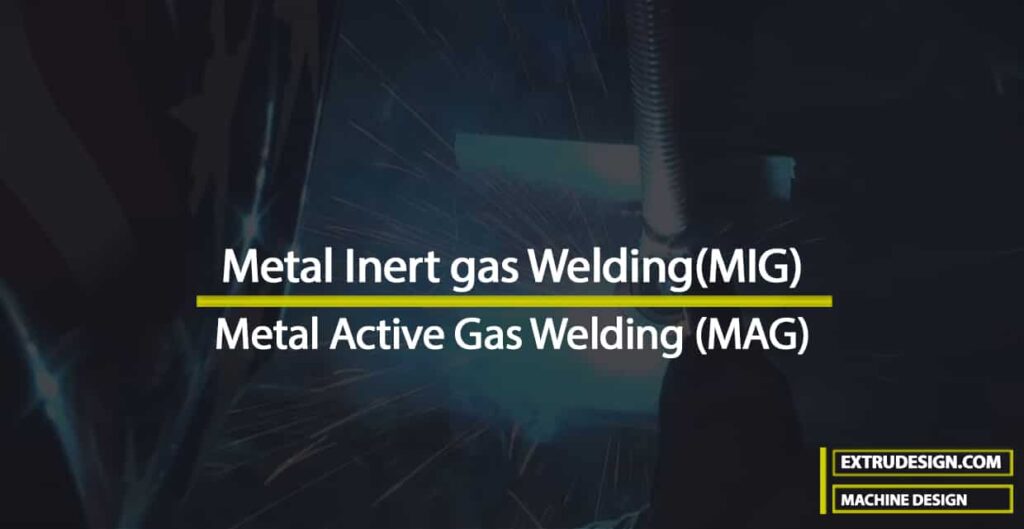
Metal Inert Gas Welding (MIG)
Metal Inert Gas Welding (MIG) or Metal Active Gas Welding (MAG) both known as Gas Metal Arc Welding (GMAW). It is one of the most common types of welding. This MIG welding process popular welding process used for automotive parts repairs (exhausts) and also used in welding requirements of homes and buildings.
In this MIG Welding process, the arc is shielded by a gas like argon or helium, or a gas mix. To prevent oxidation of the electrodes they have deoxidizers, making it possible to weld multiple layers.
Following is the overall classification of the Welding process.
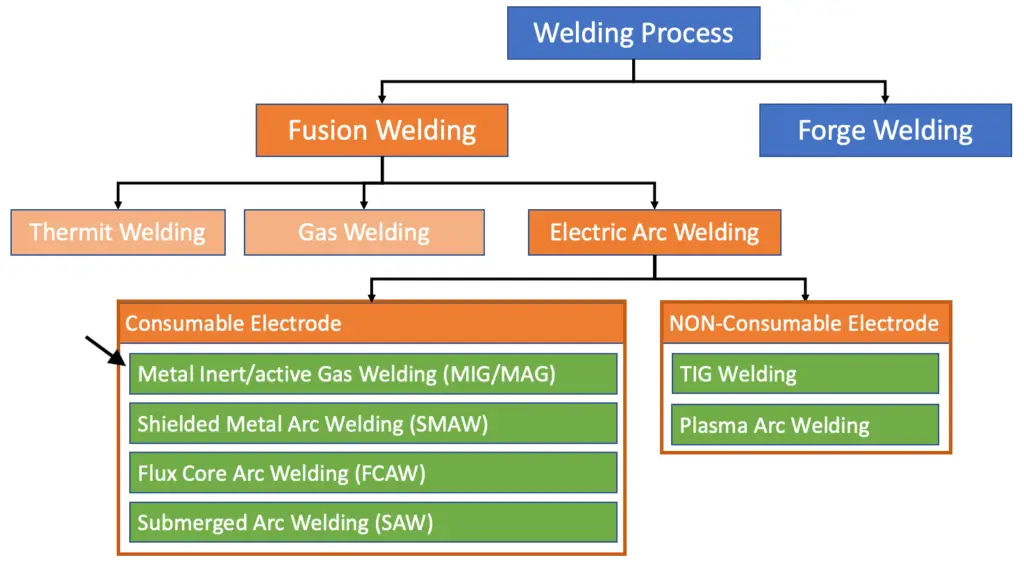
Metal Inert gas welding (MIG) is classified under the Electric arc welding process with the consumable electrode.
Metal Inert Gas Welding (MIG) Process
Metal Inert Gas (MIG) welding is an Electric arc welding process that uses consumable electrodes. A continuous solid wire electrode or definite length solid consumable electrodes are fed into the weld pool from a welding gun. Where the two base metals are melted together to form the weld joint.
The welding torch also feeds the shielding gas such as argon or helium or a gas mix alongside the electrode. Which helps to protect the weld pool from airborne contaminants.
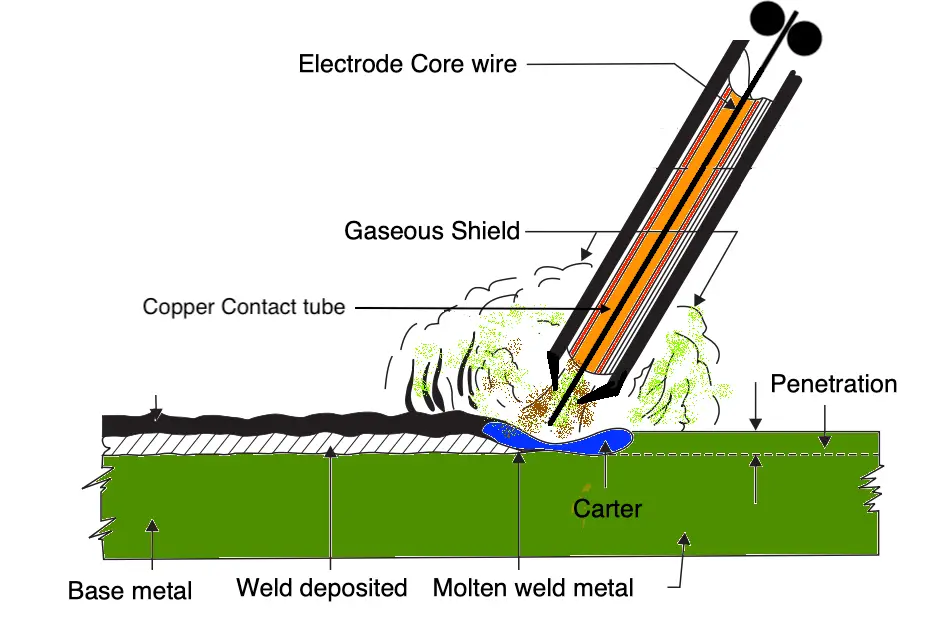
- Metal inert gas welding (MIG) is a versatile welding technique suitable for both thick section and thin sheet components.
- Mostly a wire electrode is used in MIG welding. this wire electrode is continuously fed into the welding gun.
- When an arc is struck between the end of a wire electrode and the base metals, this will melt the base metals and the wire electrode and form the weld pool.
- The wire electrode will produce the heat and melt itself to act as the filler material for the weld joint.
- The heat in the electrode is produced due to the welding current passed on to the electrode by the copper contact tube around the wire electrode.
- Shielding gas is also supplied in order to protect oxidisation by the surrounding atmosphere. The shielding gas selection can depend on the type of material we are welding and the application where we weld.
Also, read about the Heat Affected Zone in the welding process.
Additional MIG Welding Techniques
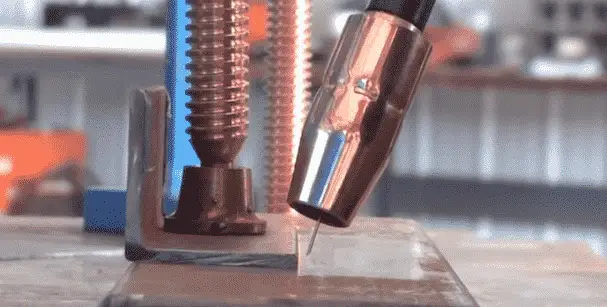
Push Welding Technique: Pushing the welding gun away from the weld puddle produces lower penetration and a wider, flatter weld bead because the arc force is directed away from the weld puddle.
Pull Welding Technique: To achieve a deeper penetration narrow weld bed, the welding gun will be pointed back at the weld puddle and dragged away from the deposited metal.
These are the general welding techniques. Along with this there 4 ways of transferring the filler metal from the wire electrode to the weld pool. Those are mentioned below.
Short-Circuiting Mode: Also known as dip mode. where the filler metal is transferred while the wire electrode is transferred during repeated electric short-circuits. The transfer of metal occurs only when the electrode is physically in contact with the molten metal puddle or the base material.
Globular Mode: With Globular mode, the filler metal will be transferred along with the short-circuiting and also in the form of gravity-assisted molten metal drops (irregular shapes). The electrode does not need to be in contact with the base metal.
Spray Mode: This technique of filler metal transfer involves high energy. unlike globular transfer mode, a continuous stream of small droplets of molten metal will be transferred at a very high energy level. The benefits of this technique are we can achieve up to 98% of electrode efficiency, a high disposition rate, the excellent appearance of the weld bead.
Pulsed Mode: This method is another variant of the above spray method with a controlled energy level. The filler metal transfer occurs in the form of a single molten droplet when the current level is high.
These are the different techniques in the MIG welding process.
Shielding Gases used in MIG Welding
The shielding gases used for the MIG welding process are Argon, Carbon dioxide, oxygen, and a special mixture of gases with helium.
The main function of the shielding gas is to prevent oxidation with the surrounding atmosphere. And also this shielding gas promotes the formation of arc plasma, and stabilizes the arc roots on the surface metal, and also smoothens the transfer of the droplets from the wire electrode to the weld pool.
What materials we can weld with MIG Welding?
With MIG welding, we can use a wide range of materials such as stainless steel, carbon steel, aluminum. Carbon steels are the most preferable materials with MIG welding.
MIG Welding Applications
- Automotive Industry, repair works of the automobile exhausts
- All the sheet metals welding done with the MIG welding
- Piping system also uses the MIG welding
Advantages of MIG welding
- Much Faster, leads to shorter lead times, low production costs
- Can join many types of metals
- Less skilled welders are sufficient
- Equipment is available for an affordable cost
- Electrode efficiencies are higher
- MIG welding is excellent for tack and spot welds
- Can weld in may all positions
Disadvantages of MIG Welding
- Not Precise weldment when compared to TIG welding process
- MIG welding is limited to the indoors, since wind is an effecting factor for this welding process.
Conclusion
We have discussed the MIG welding process, and where the MIG welding process used, and what are the applications, advantages of metal inert gas welding also disadvantages of the Metal Active Gas welding process. Most importantly what is the shielding gases used in MIG welding. Let us know what do you think about this article in the comment section below.
Compare this MIG welding with TIG welding here!
Leave a Reply