In metal works, Grinding is the metal removal process by the application of abrasives which are bonded to form a rotating wheel. In this grinding process, the metal is removed from the workpiece when the rotating wheel (abrasive) comes in contact with the workpiece. Many of us misunderstood that in this grinding process the metal is removed by a rubbing action. That is not correct. Actually, the grinding process is as much a cutting action as drilling, milling, and lathe turning. In the Grinding process, the Grinding wheel is the most important component. Let us discuss more details of grinding wheels in this article such as Abrasives used on grinding wheel, grinding wheel Properties, grinding wheel Shape and Structures.
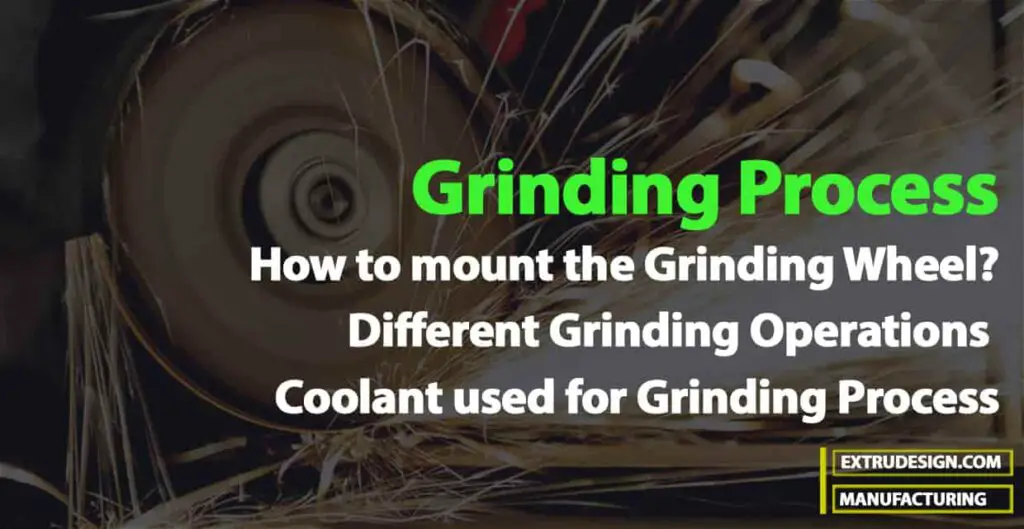
Grinding Wheel
In the grinding process, an emery or corundum wheel is used as the cutting tool. Emery and corundum are naturally found abrasives and are impure forms of aluminium oxide Al2O3. A grinding wheel is made up of thousands of tiny abrasive particles embedded in a matrix called the ‘bond’ An abrasive is an extremely hard material second in hardness only to diamond.
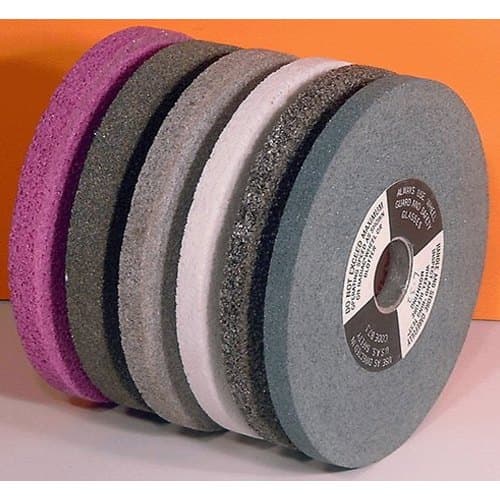
The edges of the abrasive particles project out of the periphery of the grinding wheel, and when the grinding wheel rotates, each one of the particles acts like a tiny cutting tool machining away the material from the surface of the workpiece. To the naked eye, the cut material looks like metal dust mixed with powder from the grinding wheel. However, seen under a magnifying lens, the metal dust shows all the characteristics of metal chips produced in other machining processes. The grinding process is truly a chip producing machining process.
The grinding process can produce very accurate sizes, equally accurate geometry like flatness or circularity and a perfect surface finish. The grinding wheel is capable of machining hardened steel and even hardened high-speed steel, which other machining processes cannot do.
When a grinding wheel is applied to the workpiece, the sharp edges of the abrasive grains which are cutting, will eventually lose their cutting effect and become dull. At that stage, the abrasive grain should either split and form new edges or it should break away from the wheel exposing the next layer of grains to do their work. If the dulled grains stay in the wheel, they simply keep on rubbing on work without actually cutting. This defect is known as ‘glazing’. If on the other hand, the abrasive grains break away from the wheel or split prematurely, before becoming dull, it causes a reduction in the life of the grinding wheel.
We have discussed more details about the grinding wheel here.
Mounting Grinding Wheel on A Machine, Balancing, Truing And Dressing
A grinding wheel is a delicate and fragile tool. Unless it is used properly, it may not give optimum service or may even result in accidents. In this respect, correct mounting and balancing are of utmost importance. Balancing is needed as wheels revolve at many thousand r.p.m. and any unbalanced centrifugal forces may crack the wheel or spoil the bearing.
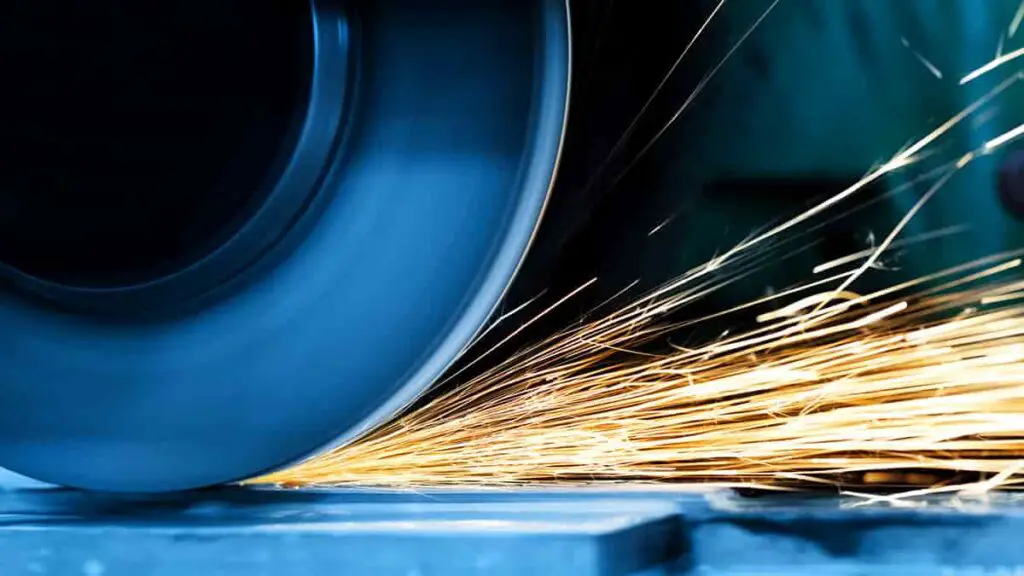
As soon as a fresh wheel has been fitted on a grinding machine spindle, it will be necessary to true its face and perhaps, its sides for a short distance down so that the wheel may become, square to the workpiece. Truing of dressing also becomes necessary after the wheel has been in use for some time, to correct for non-uniform wear on its face or for opening up its face to obtain efficient cutting conditions. The truing or dressing up of grinding wheels is done by a diamond tool. Being harder, it is able to cut through, the abrasive grains and the bond material.
Grinding Operation
There are different Grinding operations as mentioned below.
- Cylindrical grinding
- Internal grinding
- Surface grinding
Let us discuss these Grinding operations in detail.
1. Cylindrical grinding
A schematic diagram of the plain cylindrical grinder is given in the following figure.
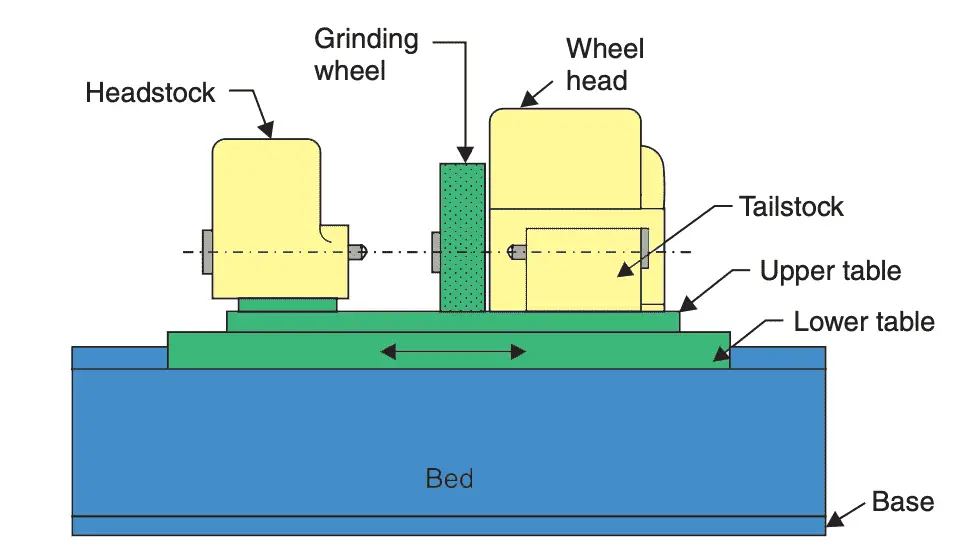
- This operation is carried out on a cylindrical grinding machine which is made in two varieties ‘‘plain’’ and the ‘‘universal’’ type.
- The fundamental design is the same in both cases, but the universal machine can be adopted for internal grinding operations as well.
- In cylindrical grinding operation, the work is mounted between two centres and is rotated.
- A grinding wheel is mounted on a spindle and revolves at a much higher r.p.m. than the work.
- The work centres are mounted on a table which can traverse at various feeds so that the entire length of the work passes to and fro in front of the wheel.
- The depth of the cut is very small, about 0.015 mm.
- When the entire length of work has passed in front of the wheel, the wheel advances forward by another 0.015 mm at the end of the traverse and so the cycle of machining goes on until the desired diameter of the workpiece is reached.
- The result is a long cylinder with a perfectly circular profile and a very fine surface finish.
2. Internal grinding
Internal grinding operation means, grinding of internal holes or bores. The principle of internal grinding is shown in the following figure.
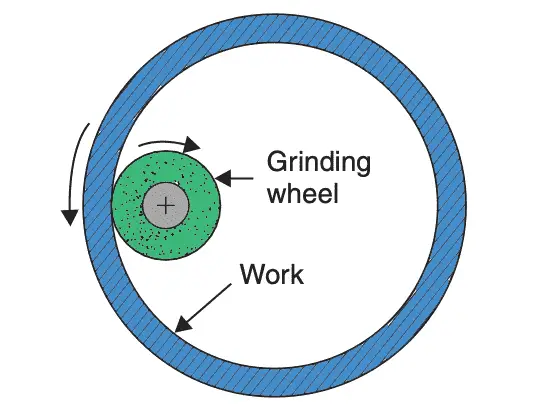
Internal grinding is designed to grind the surface of bores; whether plain or tapered with the help of a small grinding wheel mounted on a long slender spindle which can enter the bore. It is capable of giving improved geometry of the hole as well as the surface finish. This operation is performed on specially designed internal grinding machines. For internal grinding, a softer wheel is generally preferred.
3. Surface grinding
A flat surface can be ground in many ways with a grinding wheel. Some possible configurations are illustrated in the following figure.
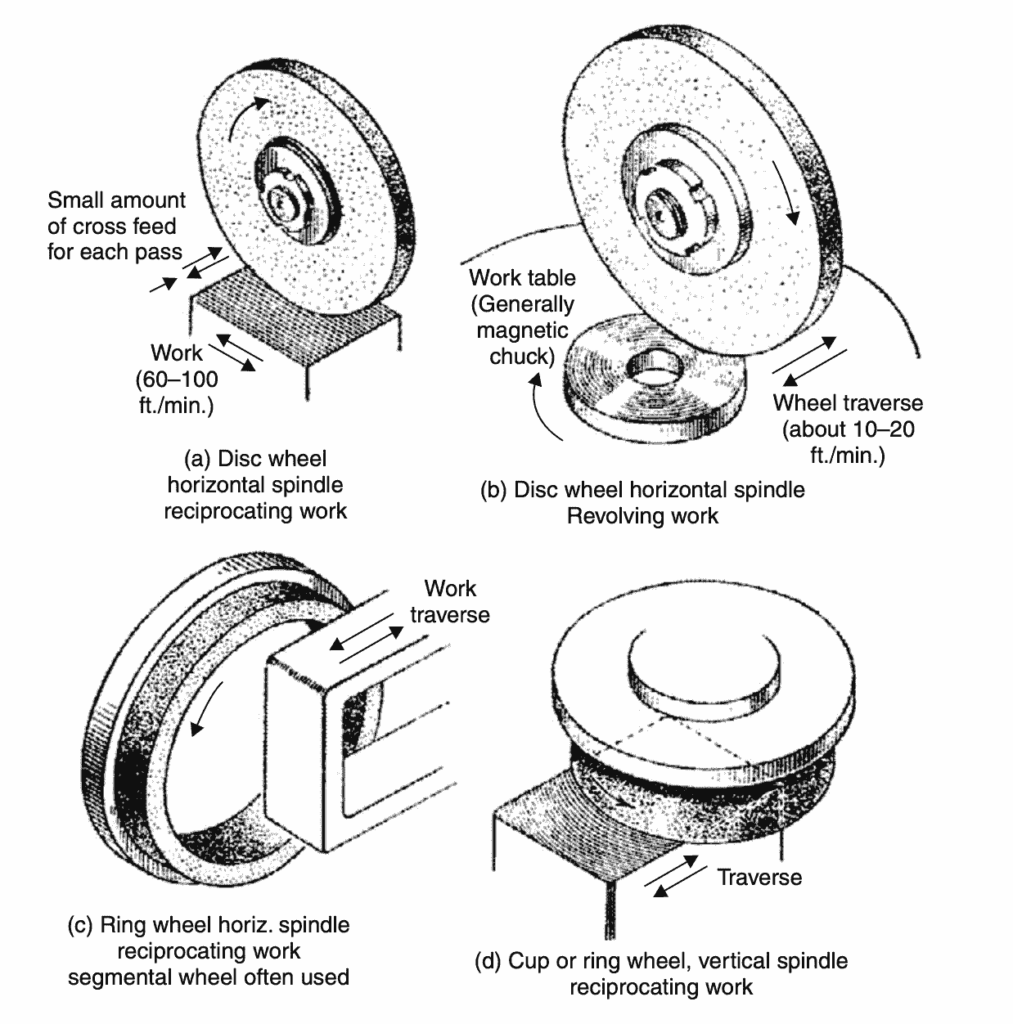
Recently surface grinding has emerged as a very important operation. Flat surfaces may be ground either by using the periphery of a disc wheel or by grinding with the end of a cup-shaped wheel. These methods can be further sub-classified according to the method of feeding the work to the wheel. The method of using disc wheels entails the use of a horizontal spindle grinding machine. The cup wheels may be used in conjunction with either a horizontal or vertical spindle machine.
Grinding Wheel Speeds
The wheel manufacturer specifies a maximum safe r.p.m. for the wheel. In actual operation, this speed should never be exceeded. Like conventional machining methods, the concept of cutting speeds applies to grinding wheels also. The average recommended wheel speeds in metres per minute for different grinding operations are given below.
Cylindrical grinding | 2000 metres/minutes |
Internal grinding | 700–1000 metres/minutes |
Surface grinding | 1200–1600 metres/minutes |
Cutting off with rubber, shellac and bakelite wheels | 3000–4000 metres/minutes |
In cylindrical grinding operation, work is made to rotate at an r.p.m. which works out to about 20-25 metres/minutes speed.
Coolant used in Grinding operation
In the grinding operation, a lot of heat is generated. This heat must be carried away. Hence an effective coolant is used. The most common coolant for grinding operation is water in which the same soda ash has been dissolved. There should be a copious flow of coolant at the work-wheel interface. The coolant also washes away the ground chips and swarf. The coolant must not have lubricant in it, otherwise, it may lead to the glazing of wheels.
Conclusion
We have clearly how to mount the grinding wheel on the grinding machine. we have also discussed the different Grinding operations and machines. Let us know what do you think about this article in the comment section below.
Oh yeah! The fact that you managed to include some explanations about cylindrical grinding wheels which have an average speed of 120 kilometers per hour for optimum safety was something I absolutely adore. As someone who’s been working at a steel factory for years, my brother-in-law always wants to get familiar with a more advanced machinery to ease his daily task. I’ll be forwarding this particular detail to him so he could get himself the right tool later on.