A Mechanical Lever is a rigid rod or bar capable of turning about a fixed point called a fulcrum. It is used as a machine to lift a load by the application of a small effort. Let us discuss more on how we can design a Lever for any application you have.
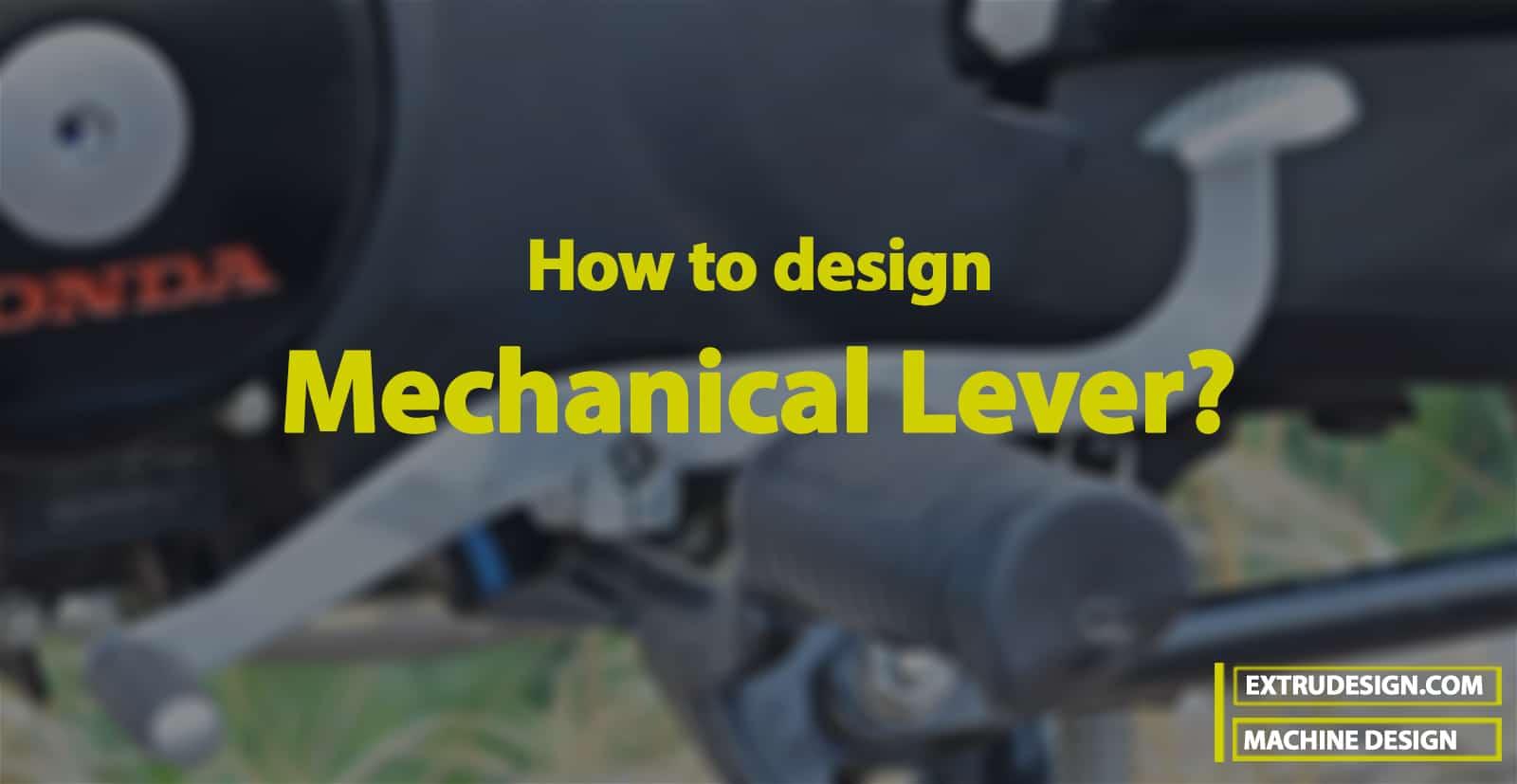
History of Lever
In ancient Egypt circa 4400 BC, a foot pedal was used for the earliest horizontal frame loom. Another device that used the principle of the lever was the swape, or shaduf, a long lever pivoted near one end with a platform or water container hanging from the short arm and counterweights attached to the long arm. This device was used in Egypt and India for raising water and lifting soldiers over battlements as early as 1500 BC.
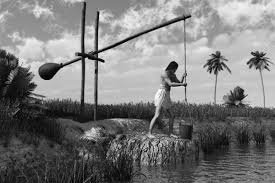
A balance beam for weighing, consisting of a bar pivoted at its centre and weights that were hung on one end to balance the object being weighed on the other end, was probably used in Egypt around 5000 BC.
Introduction to Lever
A lever is a rigid rod or bar capable of turning about a fixed point called a fulcrum. It is used as a machine to lift a load by the application of a small effort. The ratio of load lifted to the effort applied is called Mechanical Advantage.
Sometimes, a lever is merely used to facilitate the application of force in a desired direction. A lever may be straight or curved and the forces applied on the lever (or by the lever) may be parallel or inclined to one another. The principle on which the lever works is the same as that of moments.
Consider a straight lever with parallel forces acting in the same plane as shown in the following figure.
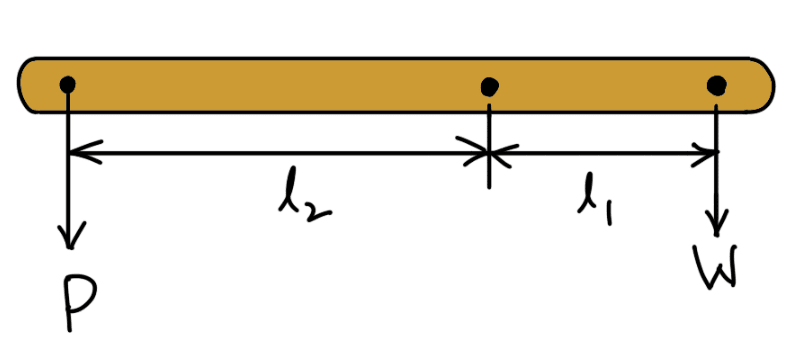
- The points A and B through which the load and effort are applied are known as load and effort points respectively.
- F is the fulcrum about which the lever is capable of turning.
- The perpendicular distance between the load point and fulcrum (l1) is known as the load arm.
- The perpendicular distance between the effort point and fulcrum (l2) is called the effort arm.
According to the principle of moments,
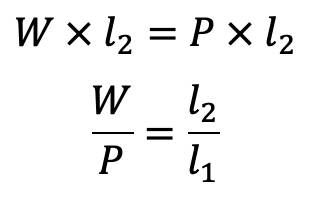
Mechanical Advantage
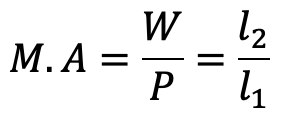
The ratio of the effort arm to the load arm i.e. l2 / l1 is called leverage.
A little consideration will show that if a large load is to be lifted by a small effort, then the effort arm should be much greater than the load arm. In some cases, it may not be possible to provide a lever with a large effort arm due to space limitations.
Therefore in order to obtain great leverage, compound levers may be used. The compound levers may be made of straight pieces, which may be attached to one another with pin joints. The bell-cranked levers may be used instead of a number of jointed levers. In a compound lever, the leverage is the product of leverages of various levers.
Application of Levers in Engineering
The load W and the effort P may be applied to the lever in three different ways as shown in the following figure. The levers shown at (a), (b) and (c) in the following figures are called first type, second type and third type of levers respectively.
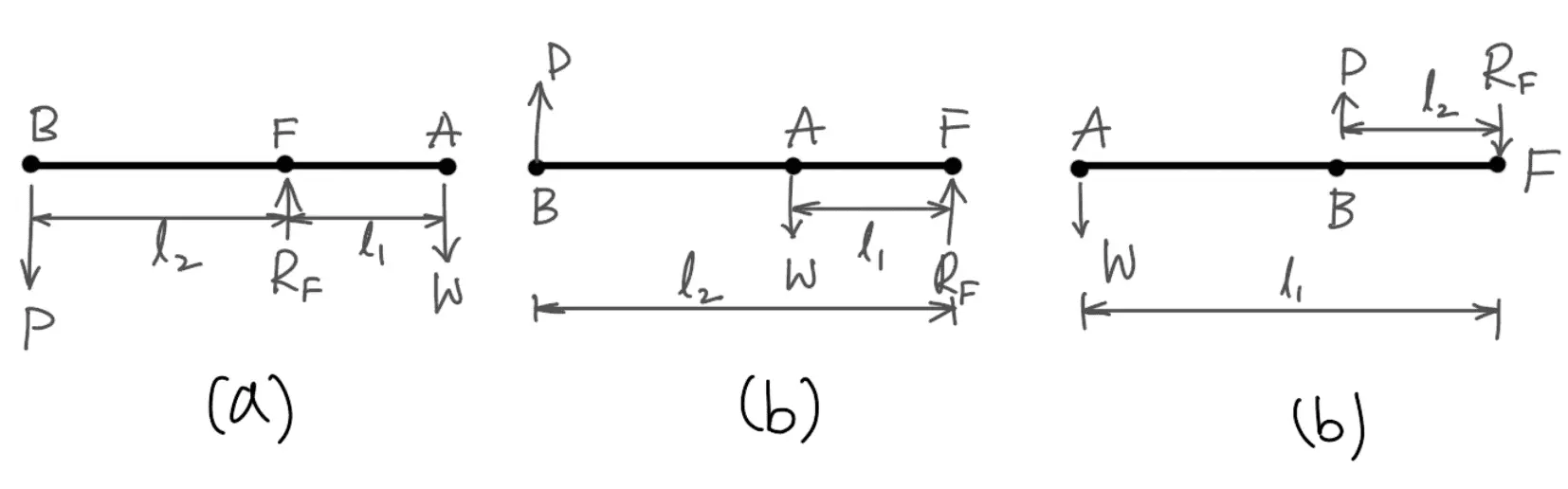
In the first type of lever, the fulcrum is in between the load and effort. In this case, the effort of the arm is greater than the load arm, therefore the mechanical advantage obtained is more than one. Such types of levers are commonly found in bell-cranked levers used in railway signalling arrangements, rocker arms in internal combustion engines, the handle of a hand pump, hand wheels of a punching press, a beam of a balance, foot levers etc.
In the second type of lever, the load is in between the fulcrum and effort. In this case, the effort arm is more than the load arm, therefore the mechanical advantage is more than one. The application of such types of levers is found in levers of loaded safety valves.
In the third type of lever, the effort is in between the fulcrum and load. Since the effort arm, in this case, is less than the load arm, therefore the mechanical advantage is less than one. The use of such types of levers is not recommended in engineering practice. However, a pair of tongs, the treadle of a sewing machine etc. are examples of this type of lever.
Designing Lever
The design of a lever consists in determining the physical dimensions of a lever when forces
acting on the lever are given. The forces acting on the lever are
- Load (W)
- Effort (P)
- Reaction at the fulcrum F (RF).
The load and effort cause moments in opposite directions about the fulcrum.
The following procedure is usually adopted in the design of a lever :
- Generally, load W is given. We need to find the value of the effort (P) required to resist this load by taking moments about the fulcrum. When the load arm is equal to the effort arm, the effort required will be equal to the load provided the friction at the bearings is neglected.
- Finding the reaction at the fulcrum (RF), as discussed below :
(i) When W and P are parallel and their direction is the same as shown in the above figure (a), then
RF = W + P
The direction of RF will be opposite to that of W and P.
(ii) When W and P are parallel and act in opposite directions as shown in figure (b) and (c),
then RF will be the difference of W and P. For load positions as shown in Fig. 15.2 (b),
RF = W – P
and for load positions as shown in Figure (c),
RF = P – W
The direction of RF will be opposite to that of W or P whichever is greater.
(iii) When W and P are inclined to each other as shown in below figure (a), then RF, which is equal to the resultant of W and P, is determined by the parallelogram law of forces. The line of action of RF passes through the intersection of W and P and also through F. The direction of RF depends upon the direction of W and P.
(iv) When W and P act at right angles and the arms are inclined at an angle θ as shown in
the following figure (b)
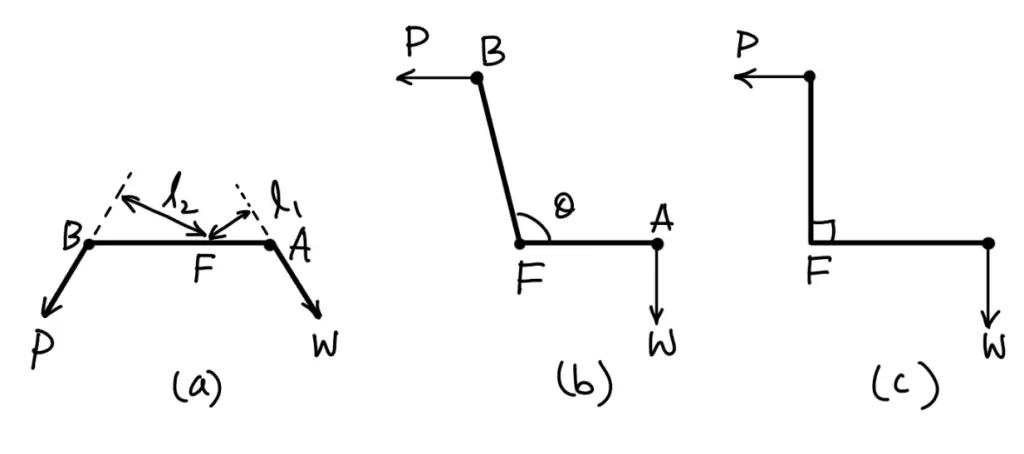
then RF is determined by using the following relation:

In case the arms are at right angles as shown in the following (c), then
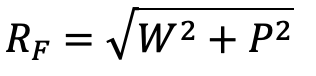
- Knowing the forces acting on the lever, the cross-section of the arm may be determined by considering the section of the lever at which the maximum bending moment occurs. In the case of levers having two arms as shown in the following figure (a) and cranked levers, the maximum bending moment occurs at the boss. The cross-section of the arm may be rectangular, elliptical or I-section as shown in Figure (b). We know that section modulus for rectangular sections,
Z = 1/6 × t × h2
where
t = Breadth or thickness of the lever
h = Depth or height of the lever
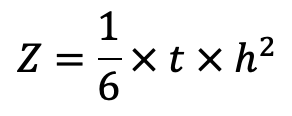
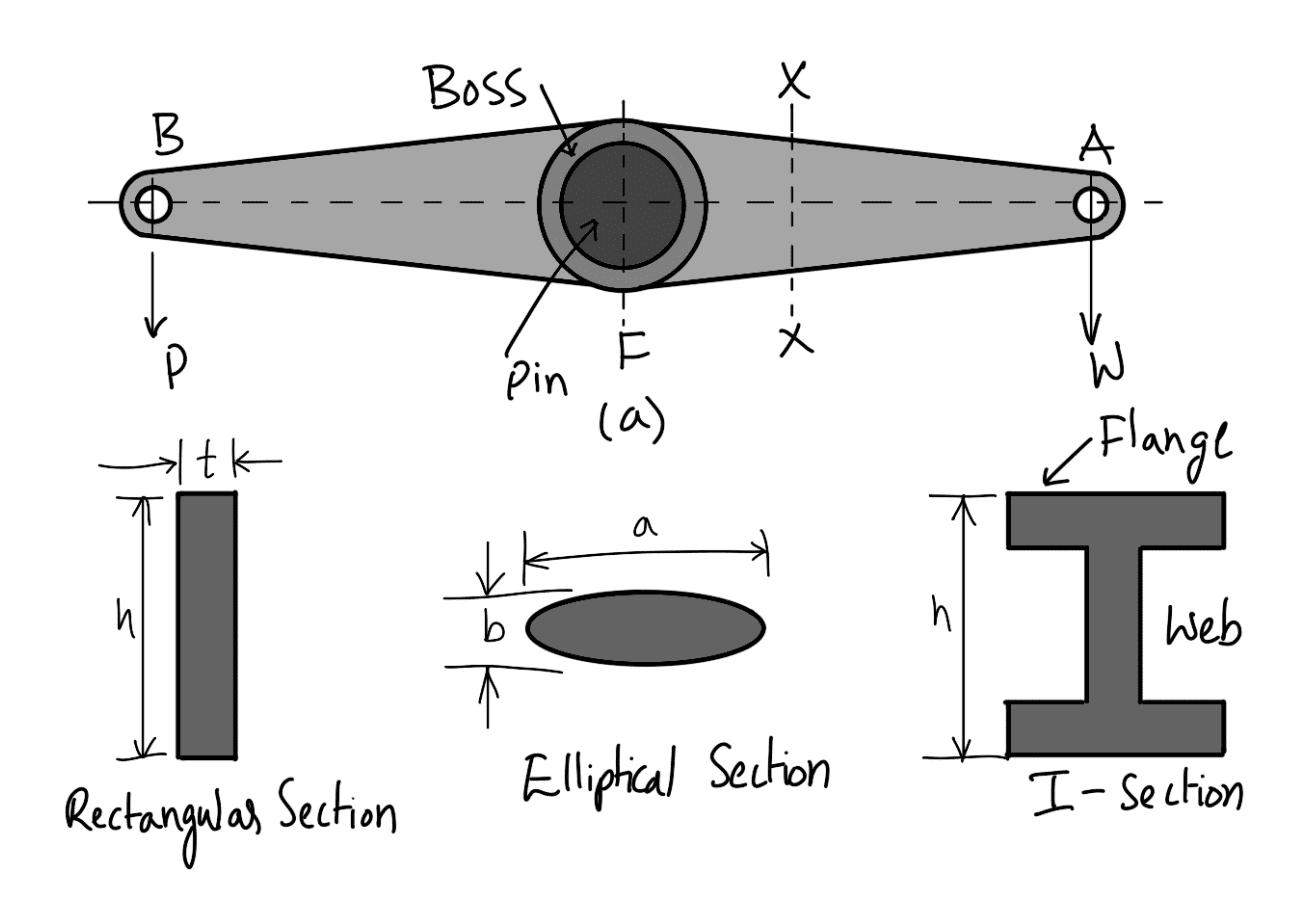
The height of the lever is usually taken as 2 to 5 times the thickness of the lever. For the elliptical section, section modulus,
Z = π/32 × b × a2
where
a = Major axis
b = Minor axis
The major axis is usually taken as 2 to 2.5 times the minor axis.
For the I-section, it is assumed that the bending moment is taken by flanges only. With this assumption, the section modulus is given by
Z = Flange area × depth of the section
The section of the arm is usually tapered from the fulcrum to the ends. The dimensions of the arm at the ends depend upon the manner in which the load is applied. If the load at the end is applied by forked connections, then the dimensions of the lever at the end can be proportioned as a knuckle joint.
- The dimensions of the fulcrum pin are obtained from bearing considerations and then checked for shear. The allowable bearing pressure depends upon the amount of relative motion between the pin and the lever. The length of the pin is usually taken from 1 to 1.25 times the diameter of the pin. If the forces on the lever do not differ much, the diameter of the pins at load and effort point shall be taken equal to the diameter of the fulcrum pin so that the spares are reduced. Instead of choosing a thick lever, the pins are provided with a boss in order to provide sufficient bearing length.
- The diameter of the boss is taken twice the diameter of the pin and the length of the boss is equal to the length of the pin. The boss is usually provided with a 3 mm thick phosphor bronze bush with a dust-proof lubricating arrangement in order to reduce wear and increase the life of the lever.
Example Problems to Design a Lever
Problem Statement: A handle for turning the spindle of a large valve is shown in the following figure. The length of the handle from the centre of the spindle is 450 mm. The handle is attached to the spindle by means of a round tapered pin If an effort of 400 N is applied at the end of the handle, find the mean diameter of the tapered pin and the diameter of the handle. The allowable stresses for the handle and pin are 100 MPa in tension and 55 MPa in shear.
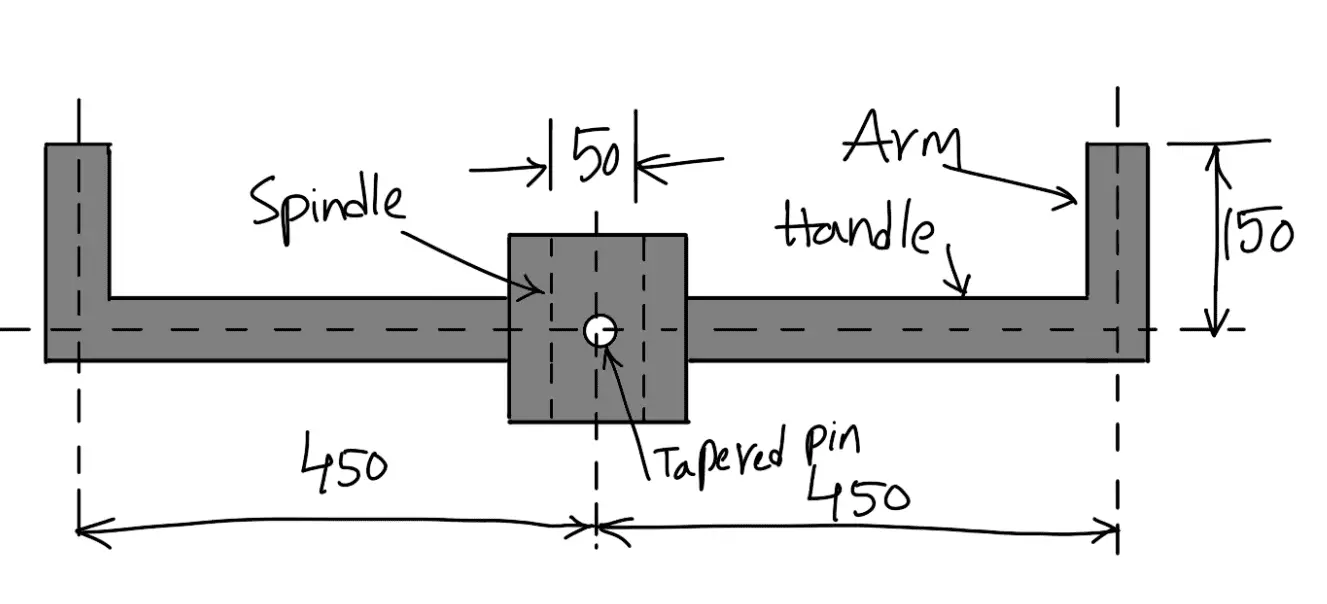
Answer:
Given data
L = 450 mm
P = 400 N
σt = 100 MPa = 100 N/mm2
τ = 55 MPa = 55 N/mm2
The mean diameter of the tapered pin
Let
d1 = Mean diameter of the tapered pin
d = Diameter of the spindle = 50 mm
We know that the torque acting on the spindle,
T = P × 2L
T = 400 × 2 × 450
T = 360 × 103 N-mm …(i)
Since the pin is in double shear and resists the same torque as that on the spindle, therefore resisting torque,
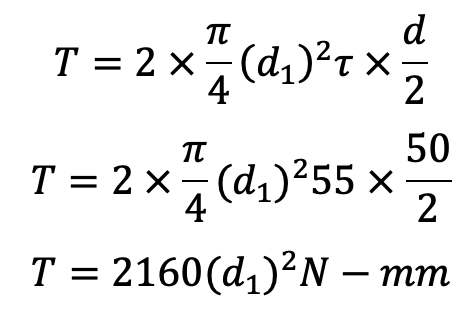
…. equation (ii)
From equations (i) and (ii), we get
(d1) 2 = 360 × 103 / 2160 = 166.7
d1 = 12.9
The mean diameter of the tapered pin is 13mm.
Diameter of the handle
Let D = Diameter of the handle.
Since the handle is subjected to both the bending moment and twisting moment, therefore the design will be based on either the equivalent twisting moment or the equivalent bending moment. We know that bending moment,
M = P × L
M = 400 × 450
M = 180 × 103 N-mm
The twisting moment depends upon the point of application of the effort. Assuming that the effort acts at a distance of 100 mm from the end of the handle, we have a twisting moment,
T = 400 × 100
T = 40 × 103 N-mm
We know that the equivalent twisting moment,
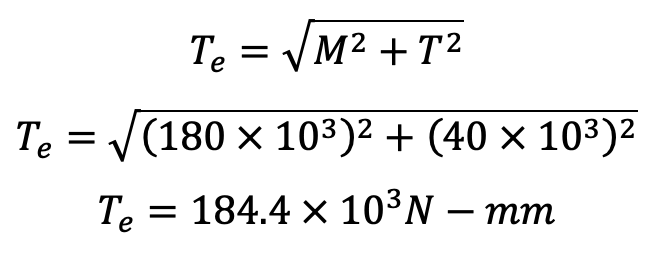
We also know that the equivalent twisting moment (Te),
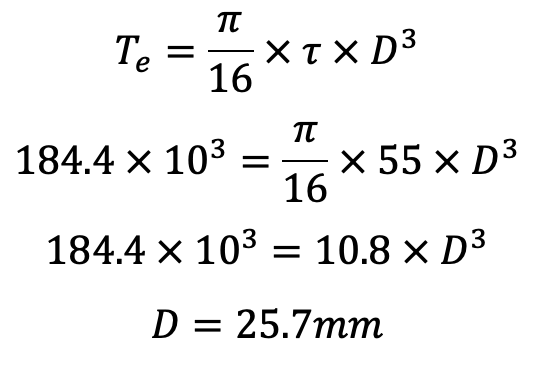
Again we know that the equivalent bending moment,
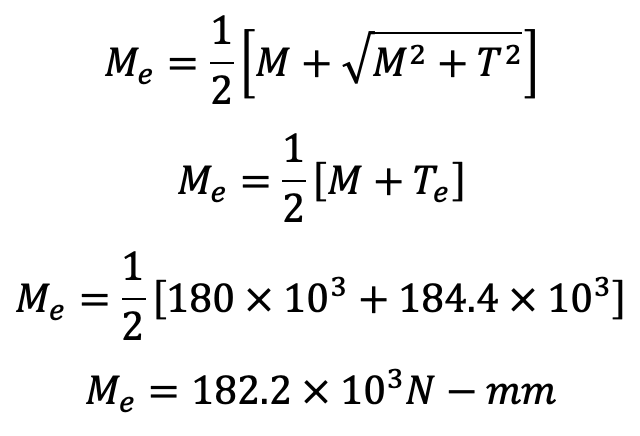
We also know that the equivalent bending moment (Me)
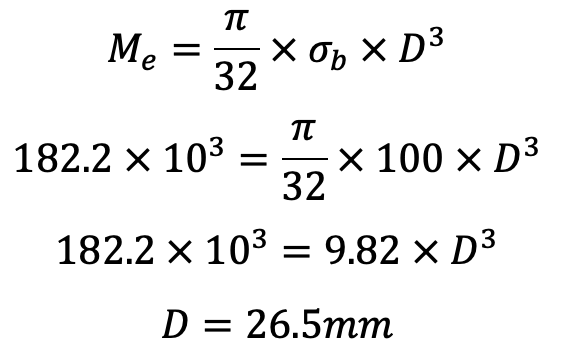
Taking the larger of the two values, we have D = 26.5 mm. Maybe we can round it up a little but we get the Diameter of the handle can be 27mm.
This is all about Levers and a brief description of how to Design a Lever. And we have discussed different lever designs separately as follows.
- Hand Lever (Hand Brake)
- Foot Lever (Brakes pedal, Foot pump Lever)
- Cranked Lever (Hoisting Winches)
- Lever Safety Valve
- Bell Crank Lever
- Rocker Arm for Exhaust Valve
Let us know what you think about this article in the comment section below.
Leave a Reply