Failure is one of the most important things that every design engineer must deal with. All the structural members and machine elements can fail to perform their intended functions. In order to understand any failure of a machine element first, we need to understand how many possible ways that a machine element can fail. Let us see the common Types of Failure Modes in Material Science.
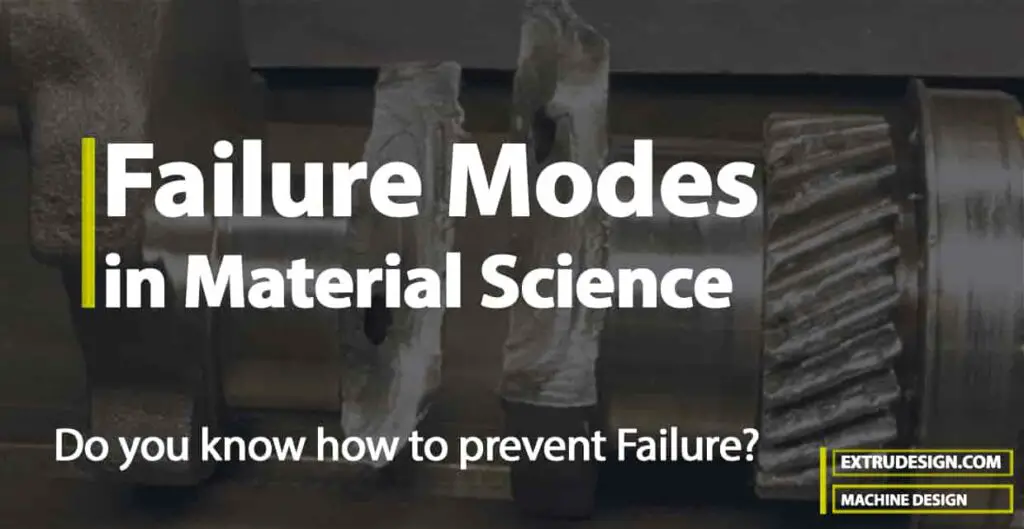
The machine elements and the structural members may fail to perform their intended functions in three general failure modes.
- Failure due to Excessive elastic deformation
- Failure due to Yielding or excessive plastic deformation
- Failure due to Fracture
An understanding of the common types of failure is important in good design because it is always necessary to relate the loads and dimensions of the member to some significant material parameter that limits the load-carrying capacity of the member.
For different types of failure, different significant parameters will be important.
Failure due to Excessive Elastic Deformation
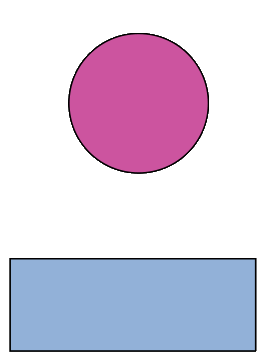
Two general types of excessive elastic deformation may occur
- excessive deflection under conditions of stable equilibrium, such as the deflection of a beam under gradually applied loads
- sudden deflection, or buckling, under conditions of unstable equilibrium.
Excessive elastic deformation of a machine part can mean failure of the machine just as much as if the part is completely fractured. For example, a shaft that is too flexible can cause rapid wear of the bearing, or the excessive deflection of closely mating parts can result in interference and damage to the parts.
The sudden buckling type of failure may occur in a slender column when the axial load exceeds the Euler critical load or when the external pressure acting against a thin-walled shell exceeds a critical value.
Failures due to excessive elastic deformation are controlled by the modulus of elasticity, not by the strength of the material.
Generally, little metallurgical control can be exercised over the elastic modulus.
The most effective way to increase the stiffness of a member is usually by changing its shape and increasing the dimensions of its cross-section.
Failure due to Yielding or Excessive Plastic Deformation
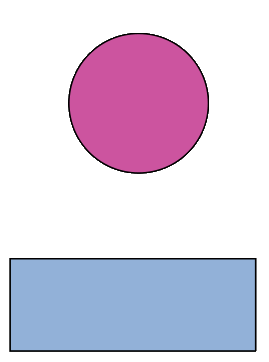
Yielding, or excessive plastic deformation, occurs when the elastic limit of the metal has been exceeded.
Yielding produces a permanent change of shape, which may prevent the part from functioning properly any longer.
In a ductile metal under conditions of static loading at room temperature yielding rarely results in fracture, because the metal strain hardens as it deforms, and increased stress is required to produce further deformation.
Failure by excessive plastic deformation is controlled by the yield strength of the metal for a uniaxial condition of loading.
For more complex loading conditions the yield strength is still the significant parameter,
but it must be used with a suitable failure criterion. At temperatures significantly greater than room temperature metals no longer exhibit strain hardening.
Instead, metals can continuously deform at constant stress in a time-dependent yielding known as creep.
The failure criterion under creep conditions is complicated by the fact that stress is not proportional to strain and the further fact that the mechanical properties of the material may change appreciably during service.
Failure due to Fracture
The formation of a crack that can result in complete disruption of the continuity of the member constitutes fracture.
A part made from a ductile metal that is loaded statically rarely fractures like a tensile specimen, because it will first fail by excessive plastic deformation.
However, metals fail by a fracture in three general ways:
- Sudden brittle fracture
- Fatigue, or progressive fracture
- Delayed fracture
The brittle material fractures under static loads with little outward evidence of yielding.
1. Sudden brittle fracture
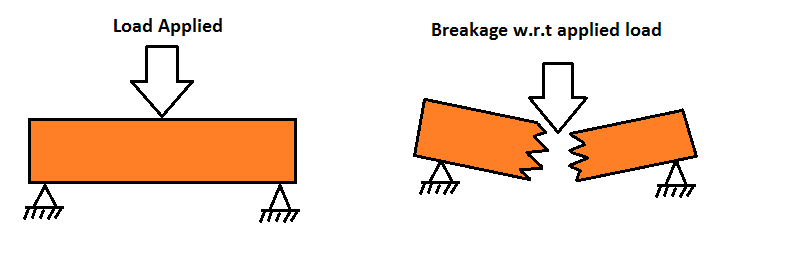
A sudden brittle type of fracture can also occur in ordinarily ductile metals under certain conditions. Plain carbon structural steel is the most common example of a material with a ductile to brittle transition.
A change from the ductile to the brittle type of fracture is promoted by a decrease in temperature, an increase in the rate of loading, and the presence of a complex state of stress due to a notch.
2. Fatigue or Progressive Fracture

Most fractures in machine parts are due to fatigue. Fatigue failures occur in parts that are subjected to alternating, or fluctuating, stresses. A minute crack starts at a localized spot, generally at a notch or stress concentration, and gradually spreads over the cross-section until the member breaks.
Fatigue failure occurs without any visible sign of yielding at nominal or average stresses that are well below the tensile strength of the metal.
Fatigue failure is caused by a critical localized tensile stress which is very difficult to evaluate, and therefore design for fatigue failure is based primarily on empirical relationships using nominal stresses. Read more about Fatigue here
3. Delayed Fracture
One common type of Delayed fracture is a stress-rupture failure, which occurs when the metal has been statically loaded at an elevated temperature for a long period of time. Depending upon the stress and the temperature there may be no yielding prior to fracture.
A similar type of delayed fracture, in which there is no warning by yielding prior to failure, occurs at room temperature when steel is statically loaded in the presence of hydrogen.
These are all the Failure modes that may occur in materials. Let us see how we can control these Failure modes.
Preventing Failure of Materials while designinng machine lements
- All engineering materials show a certain variability in mechanical properties, which in turn can be influenced by changes in heat treatment or fabrication.
- Further, uncertainties usually exist regarding the magnitude of the applied loads, and approximations are usually necessary for calculating the stresses for all but the most simple member.
- Thus, in order to provide a margin of safety and to protect against failure from unpredictable causes, it is necessary that the allowable stresses be smaller than the stresses which produce failure.
- The value of stress for a particular material used in a particular way which is considered to be safe stress is usually called the working stress σw
- For static applications, the working stress of ductile metals is usually based on the yield strength σ0 and for brittle metals on the ultimate tensile strength σu
- Values of working stress are established by the local and Federal agencies and by technical organizations such as the American Society of Mechanical Engineers (ASME). See all the list of engineering standards.
- The working stress may be considered as either the yield strength or the tensile strength divided by a number called the factor of safety.
σw = σ0/N0
or
σw = σu/Nu
where
σw = working stress, psi
σ 0 = yield strength, psi
σ u =tensile strength, psi
N0 = factor of safety based on yield strength
Nu = factor of safety based on tensile strength
- The value assigned to the factor of safety depends on an estimate of all the factors discussed above.
- In addition, careful consideration should be given to the consequences which would result from failure.
- If failure would result in loss of life, the factor of safety should be increased.
- The type of equipment will also influence the factor of safety.
- In military equipment, where light weight may be a prime consideration, the factor of safety may be lower than in commercial equipment.
- The factor of safety will also depend on the expected type of loading.
- For static loading, as in a building, the factor of safety would be lower than in a machine, which is subjected to vibration and fluctuating stresses.
Conclusion
We have discussed different failure modes in materials science also discussed how we can control these failure modes while designing machine elements. Along with these, we have different theories of failures when a machine component is subjected to different types of different stress. Also, Fracture failure, fatigue failure, and Creep failure are observed in the testing stage of prototypes. All these concepts are very important for every design engineer should have a deep understanding of. Let us know what do you think about these in the comment section below.
Leave a Reply