The rope drives are widely used where a large amount of power is to be transmitted, from one pulley to another, over a considerable distance. It may be noted that the use of flat belts is limited for the transmission of moderate power from one pulley to another when the two pulleys are not more than 8 meters apart. If large amounts of power are to be transmitted by the flat belt, then it would result in excessive belt cross-section. Let us discuss the two main types of Rope drives Fiber ropes and Wire ropes.
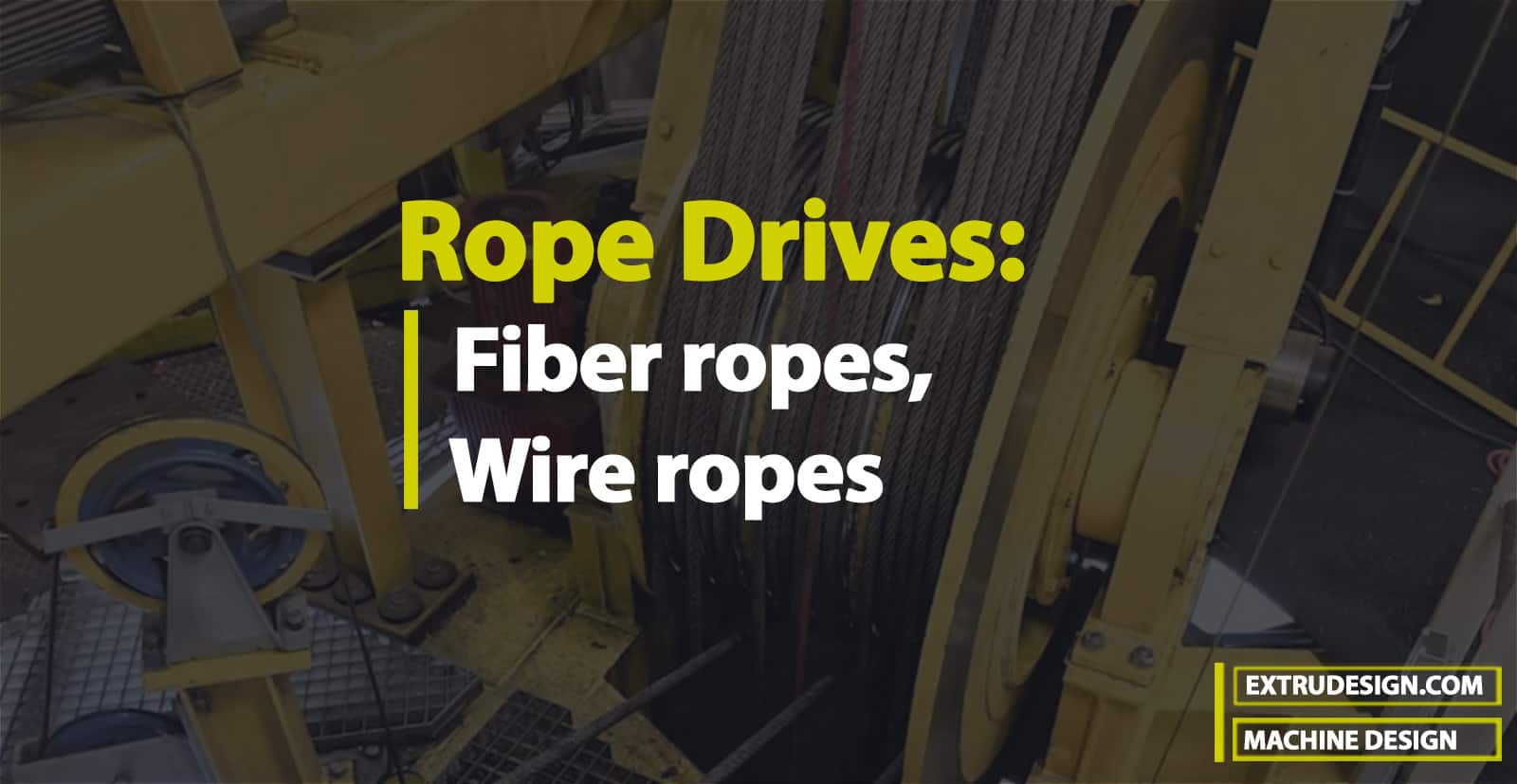
The ropes drives uses the following two types of ropes:
- Fibre ropes
- Wire ropes
The fiber ropes operate successfully when the pulleys are about 60 meters apart, while the wire ropes are used when the pulleys are up to 150 meters apart.
Fibre Ropes
The ropes for transmitting power are usually made from fibrous materials such as hemp, manila, and cotton. Since the hemp and manila fibers are rough, therefore the ropes made from these fibers are not very flexible and possess poor mechanical properties.
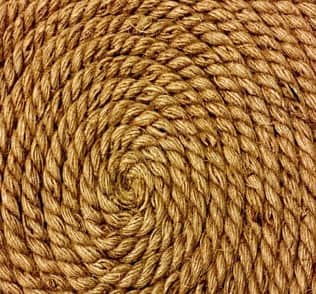
The hemp ropes have less strength as compared to manila ropes. When the hemp and manila ropes are bent over the sheave, there is some sliding of the fibers, causing the rope to wear and chafe internally. In order to minimize this defect, the rope fibers are lubricated with tar, tallow, or graphite.
The lubrication also makes the rope moisture-proof. The hemp ropes are suitable only for hand-operated hoisting machinery and as tie ropes for lifting tackles, hooks, etc.
The cotton ropes are very soft and smooth. The lubrication of cotton ropes is not necessary. But if it is done, it reduces the external wear between the rope and the grooves of its sheaves. It may be noted that the manila ropes are more durable and stronger than cotton ropes. The cotton ropes are costlier than manila ropes.
Notes :
1. The diameter of manila and cotton ropes usually ranges from 38 mm to 50 mm. The size of the rope is usually designated by its circumference or ‘girth’.
2. The ultimate tensile breaking load of the fiber ropes varies greatly. For manila ropes, the average value of the ultimate tensile breaking load may be taken as 500 d 2 kN, and for cotton ropes, it may be taken as 350 d 2 kN, where d is the diameter of rope in mm.
Advantages of Fibre Rope Drives
The fiber rope drives have the following advantages :
- They give smooth, steady, and quiet service.
- They are little affected by outdoor conditions.
- The shafts may be out of strict alignment.
- The power may be taken off in any direction and in fractional parts of the whole amount.
- They give high mechanical efficiency.
Sheave for Fibre Ropes
The fiber ropes are usually circular in cross-section as shown in the following figure (a). The sheave for the fiber ropes is shown in the following figure (b). The groove angle of the pulley for rope drives is usually 45°.
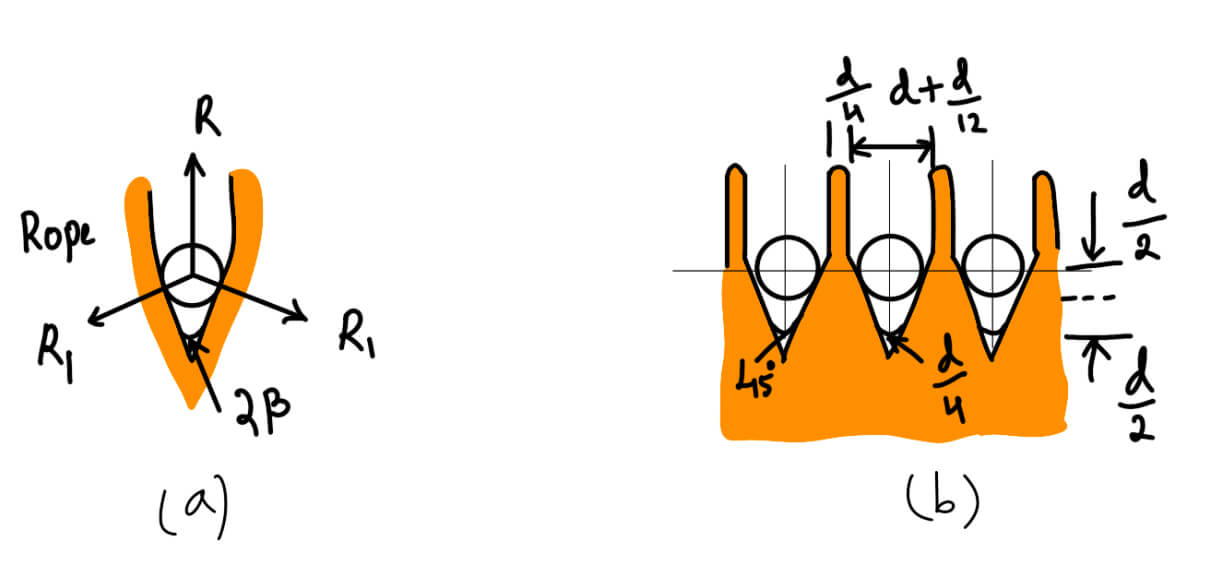
(a) Cross section of a rope. (b) Sheave (Grooved pulley) for ropes
The grooves in the pulleys are made narrow at the bottom and the rope is pinched between the edges of the V-groove to increase the holding power of the rope on the pulley. The grooves should be finished smooth to avoid chafing of the rope. The diameter of the sheaves should be large to reduce the wear on the rope due to internal friction and bending stresses. The proper size of sheave wheels is 40 d and the minimum size is 36 d, where d is the diameter of rope in cm.
Note : The number of grooves should not be more than 24.
Ratio of Driving Tensions for Fibre Rope
A fiber rope with a grooved pulley is shown in the above figure (a). The fiber ropes are designed in a similar way to V-belts. We have discussed in the previous article, that the ratio of driving tensions is
2.3 log (T1 / T2) = μ . θ . cosec 𝛃
Where μ is the Coefficient of friction between the belt and the sides of the groove.
Wire Ropes
When a large amount of power is to be transmitted over long distances from one pulley to another (i.e. when the pulleys are up to 150 meters apart), then wire ropes are used. The wire ropes are widely used in elevators, mine hoists, cranes, conveyors, hauling devices, and suspension bridges. The wire ropes run on grooved pulleys but they rest on the bottom of the *grooves and are not wedged between the sides of the grooves.
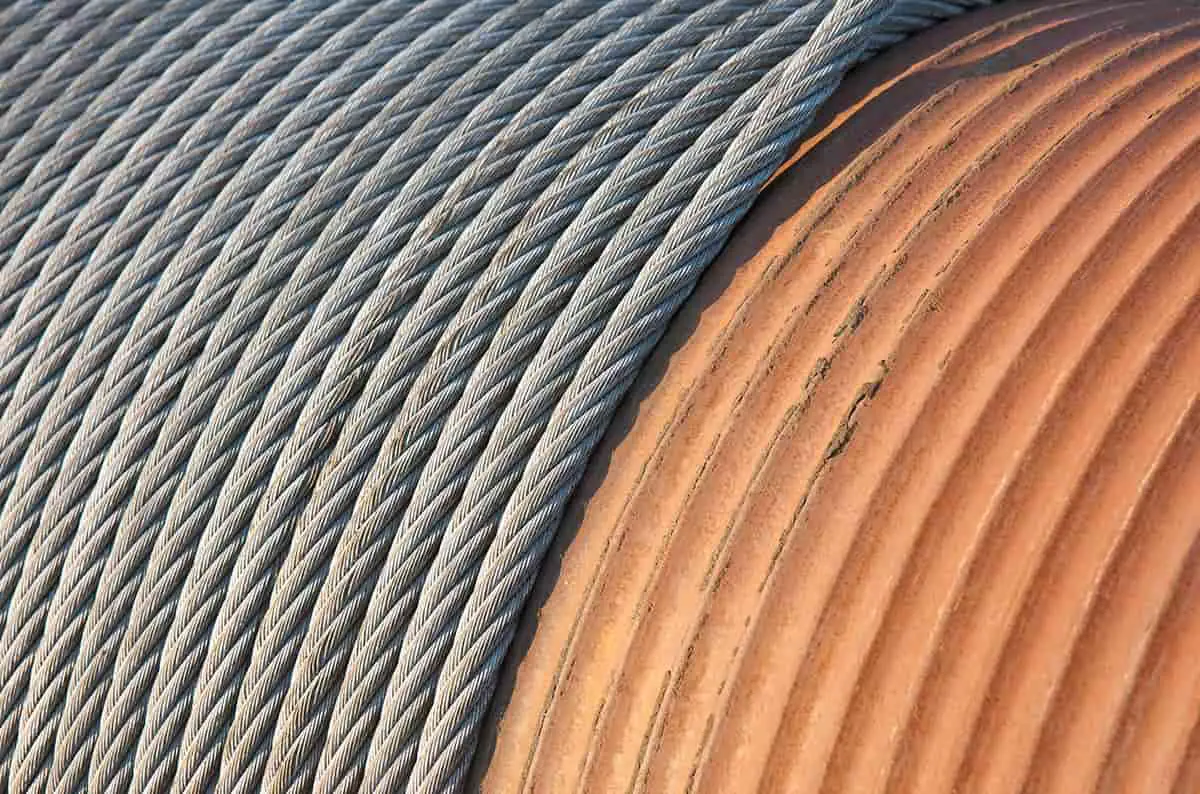
The wire ropes are made from cold-drawn wires in order to increase strength and durability. It may be noted that the strength of the wire rope increases as its size decreases. The various materials used for wire ropes in order of increasing strength are wrought iron, cast steel, extra strong cast steel, plow steel, and alloy steel. For certain purposes, the wire ropes may also be made of copper, bronze, aluminum alloys, and stainless steel.
Advantages of Wire Ropes
The wire ropes have the following advantages as compared to fibre ropes.
- These are lighter in weight,
- These can withstand shock loads
- These are more durable
- The efficiency is high
- These offer silent operation
- These are more reliable,
- They do not fail suddenly
- The cost is low.
Construction of Wire Ropes
The wire ropes are made from various grades of steel wire having a tensile strength ranging from 1200 to 2400 MPa as shown in the following table:
Grade of wire | 120 | 140 | 160 | 180 | 200 |
Tensile strength range (MPa) | 1200 – 1500 | 1400 – 1700 | 1600 – 1900 | 1800 – 2100 | 2000 – 2400 |
The wires are first given special heat treatment and then cold drawn in order to have the high strength and durability of the rope. The steel wire ropes are manufactured by special machines. First of all, a number of wires such as 7, 19, or 37 are twisted into a strand, and then a number of strands, usually 6 or 8 are twisted about a core or center to form the rope as shown in the following figure.
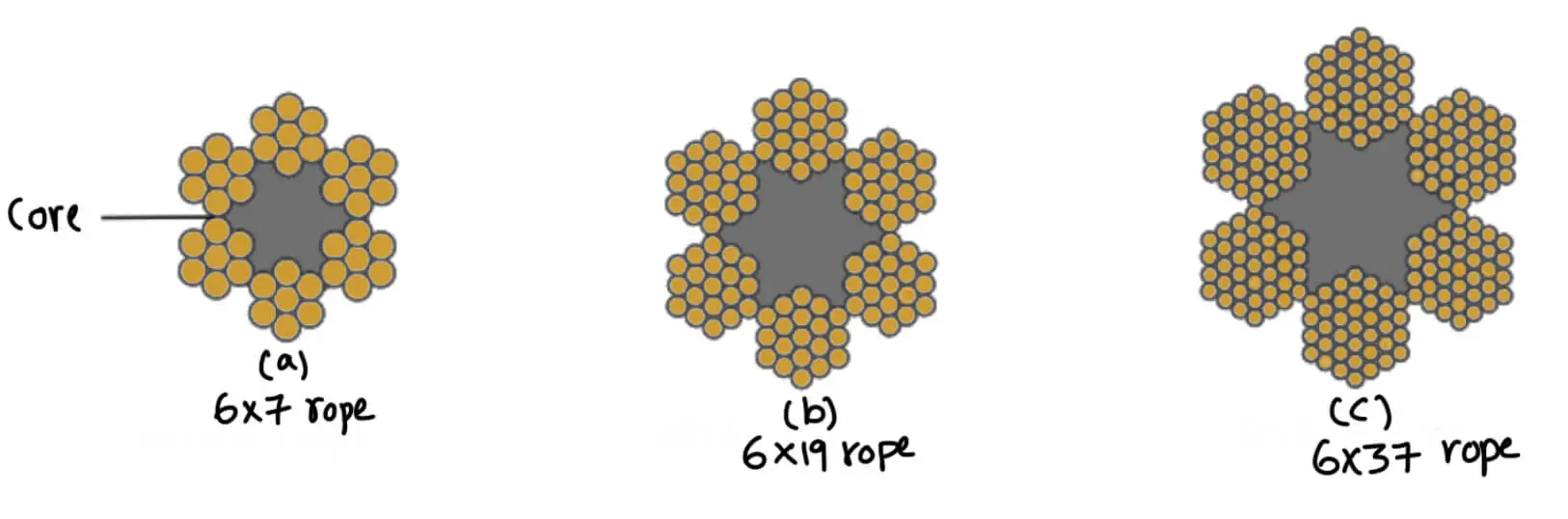
The core may be made of hemp, jute, asbestos, or a wire of softer steel. The core must be continuously saturated with lubricant for the long life of the core as well as the entire rope. The asbestos or soft wire core is used when ropes are subjected to radiant heat such as cranes operating near furnaces. However, a wire core reduces the flexibility of the rope, and thus such ropes are used only where they are subjected to high compression as in the case of several layers wound over a rope drum.
Classification of Wire Ropes
According to the direction of twist of the individual wires and that of strands, relative to each other, the wire ropes may be classified as follows:
- Cross or regular lay ropes. In these types of ropes, the direction of the twist of wires in the strands is opposite to the direction of the twist of the stands, as shown in the following figure (a). Such types of ropes are the most popular.
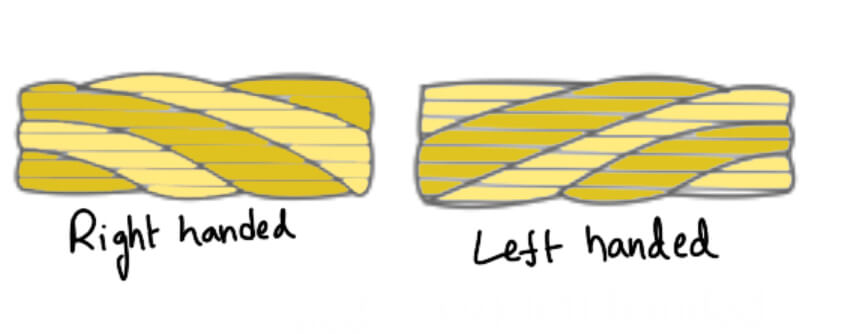
- Parallel or lang lay ropes. In these types of ropes, the direction of the twist of the wires in the strands is the same as that of strands in the rope, as shown in the following figure (b). These ropes have better bearing surface but are harder to splice and twists more easily when loaded. These ropes are more flexible and resist wear more effectively. Since such ropes have the tendency to spin, therefore these are used in lifts and hoists with guideways and also as haulage ropes.
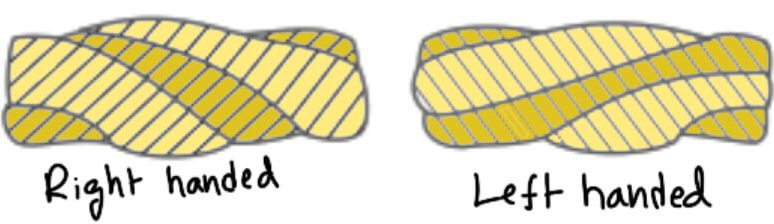
- Composite or reverse-laid ropes. In these types of ropes, the wires in the two adjacent strands are twisted in the opposite direction, as shown in the following figure (c).
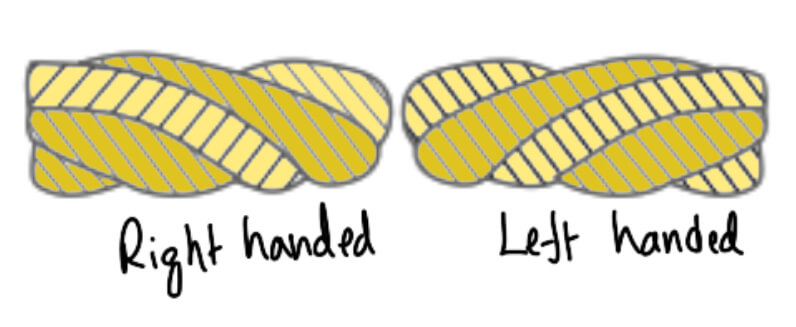
Note: The direction of the lay of the ropes may be right-handed or left-handed, depending upon whether the strands form right-hand or left-hand helixes, but the right-hand lay ropes are most commonly used.
Leave a Reply