A lathe is a machine which is used to manufacture the machine parts. Machining is one of the manufacturing processes with which we can manufacture machine parts of different shapes and sizes. We have already discussed forging and casting processes in the previous articles. However, manufactured parts with forging and casting will have poor geometry and size control and their surface finish is not very good. Hence, in most cases, castings and forgings undergo machining before these parts can be assembled with other parts to form a complete machine-like cycle or motor car. With a Lathe machine, we can do many lathe operations to produce high quality and finished products to be directly assembled with other parts of a machine.
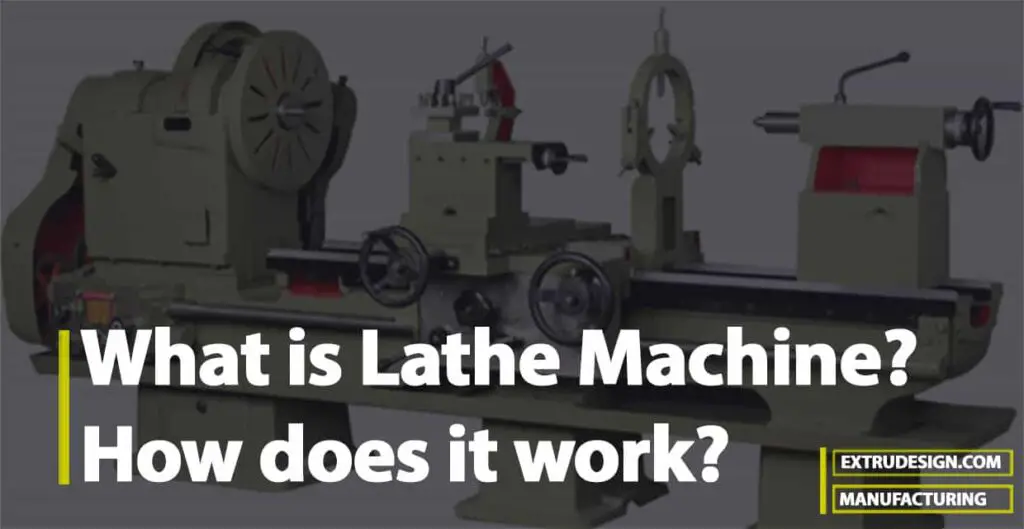
Lathe Machine
The lathe machine rotates the workpiece about its axis to perform many operations by removing material with help of a cutting tool. This cutting tool is made of a much harder material than the material of the part to be machined. Material removed from the part is achieved by the relative movement between the cutting tool and the part.
Lathe Operation
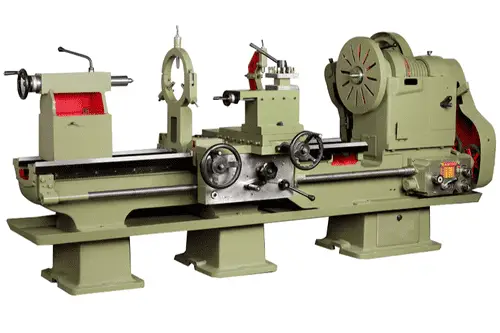
- The cutting tool is given a sharp cutting edge and it is forced to penetrate inside the workpiece surface to a small depth.
- The relative motion between the tool and workpiece results in a thin strip of material being sheared off from the workpiece reducing the thickness of the workpiece.
- This process has to be repeated several times before the entire surface of the workpiece can be covered and reduced in depth.
- The thin strip of the material sheared from the workpiece is called ‘chip’.
- It must be understood that chips are produced by shearing action and not by cutting. A substantial amount of power is required for machining.
- The function of the machine tool is to provide this power and the required motion of the workpiece relative to the tool.
- In some cases of machining, motion is given to the workpiece and the tool remains stationary.
- In some other cases, the workpiece is stationary and the machine tool provides motion to the cutting tool.
- In yet other cases, motion is given both to the tool and the workpiece.
Cutting Tools materials for Lathe
Cutting tools are made of a material which can be hardened by suitable heat treatment. During machining, a lot of heat is generated and the temperature of the cutting edge of the tool may reach 650–700°C.
The tool must maintain its hardness even at such elevated temperatures. This property of retaining its hardness at elevated temperatures is called ‘red hardness’. Cutting tools develop the property of red hardness due to the addition of tungsten and molybdenum to high carbon steel. These days, cutting tools are made of high-speed steel or tungsten carbide. Tools made of ceramic materials (like Al2O3, SiC) and polycrystalline diamonds are also used for special applications.
Cutting Speeds for Lathe Machine
What is the Cutting speed for Lathe Machine?
You must understand the concept of “cutting speed”. Cutting speed means the linear speed at which cutting takes place. If the tool is stationary, the speed at which the work material approaches the cutting edge of the tool is the cutting speed. It is measured in metres per minute.
The optimum cutting speed for a lathe depends upon the tool material, the material to be cut and whether a cutting fluid is being used or not. The purpose of using cutting fluid is to remove heat from the cutting area and to lubricate the tool face so that the friction between the chip and tool surface reduces. The use of cutting fluid makes the cutting process more efficient. Similarly, cutting at recommended cutting speed results in improved tool life and performance.
Recommended cutting speed for machining cast iron and mild steel with high-speed tools is 35 metres per minute. However, if tungsten carbide tools are used, cutting speeds of 65–70 metres per minute may be used. For non-ferrous material, much higher cutting speeds are permissible.
Centre Lathe Construction
A centre lathe is also called an engine lathe or simply a lathe. It is one of the commonest and oldest machine tools. It is also one of the most versatile and widely used machines. Its main function is the production of cylindrical profiles.
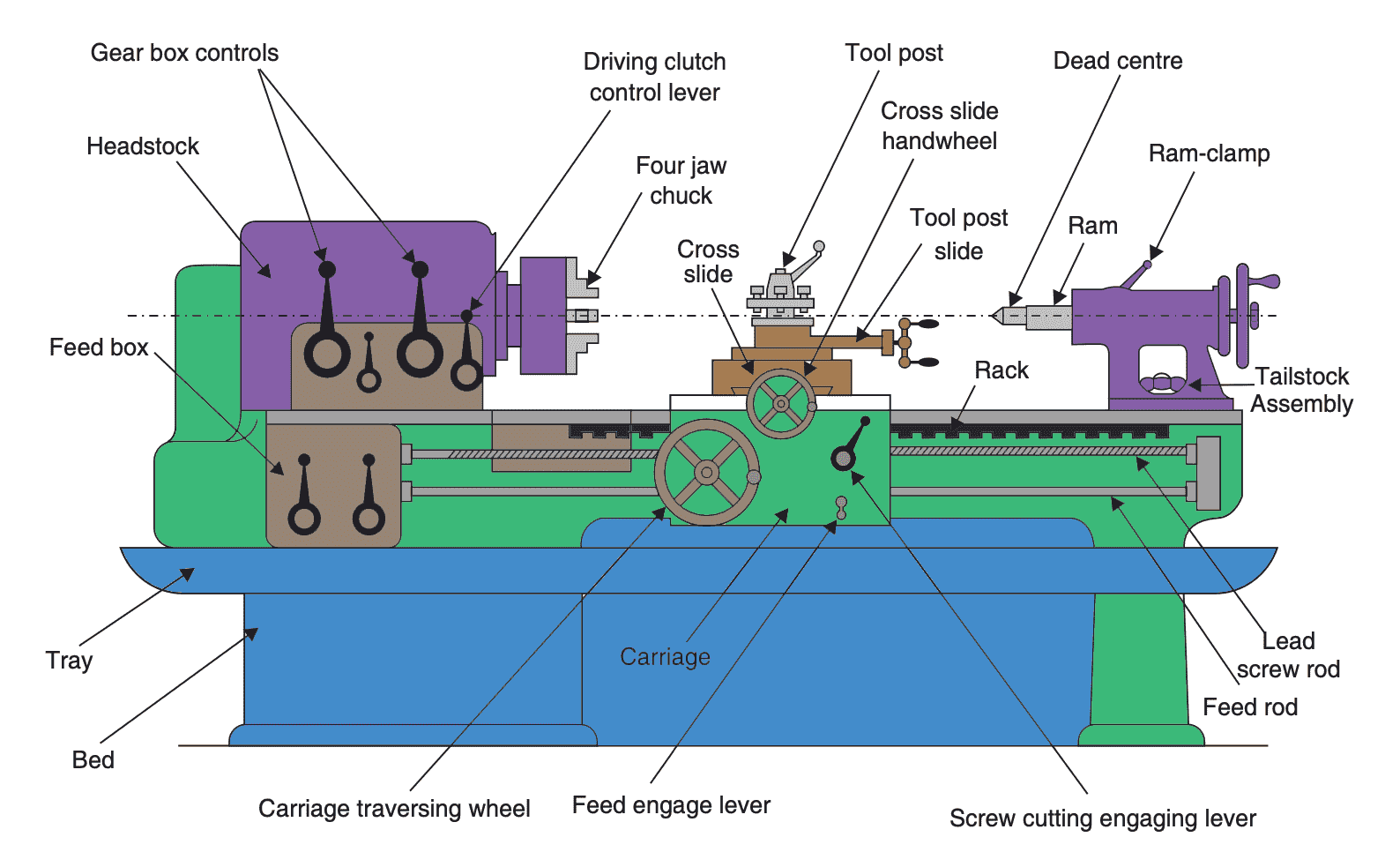
The main parts of a centre lathe are:
- Machine Bed
- Head stock
- Tailstock
- Carriage
1. Machine Bed
Machine bed usually made of cast iron. It holds or supports all other parts of the lathe. The top of the machine bed is flat and is machined to form guideways on which the carriage slides along the length of the lathe.
2. Headstock
It is fixed at the extreme left hand of the bed and contains shafts and gears immersed in lubricating oil. The driving shaft inside is driven by an electric motor. The driven shaft, which is in the form of a hollow spindle can be driven at various r.p.m. by changing gears, and projects out of the headstock, A chuck (either three-jaw or four-jaw), is screwed on this spindle. The workpiece can be held in the jaws of the chuck. When the spindle rotates, the chuck and the workpiece held also rotate about the longitudinal axis of the spindle.
3. Tailstock
A tailstock is provided at the right-hand end of the bed. It can slide along the guideways provided on the bed and maybe be brought nearer to the headstock if so desired. It can then be clamped or fixed on the bed in that position. The tailstock has a spindle in the upper part of the tailstock, the axis of which coincides with the the axis of the headstock spindle, both being at the same height above the bed. This spindle can be moved forwards or backwards by rotating a handwheel.

The front portion of the tailstock spindle carries a ‘dead’ or ‘live’ centre. When a long workpiece is held in the chuck at the headstock end, it is supported at the tailstock end by moving forward the tailstock spindle. Of course, there has to be a small conical hole in the centre of the workpiece, in which the tailstock centre may be inserted to provide support. If the centre (being carried in its bearings) rotates along with the workpiece, it is called a live centre.
However, suppose the tailstock centre remains stationary and the workpiece alone rotates. In that case, the centre is called the ‘dead centre’ and the conical tip of the centre has to be lubricated with grease to reduce the friction between the tailstock centre and the workpiece.
4. Carriage
A carriage is shown in the below figure The carriage can slide along the length of the machine bed from the tailstock end to the headstock end. This movement is controlled by manually operating the hand traversing wheel. It can also be imparted this traversing motion at different speeds automatically by engaging into the feed rod or feed shaft.
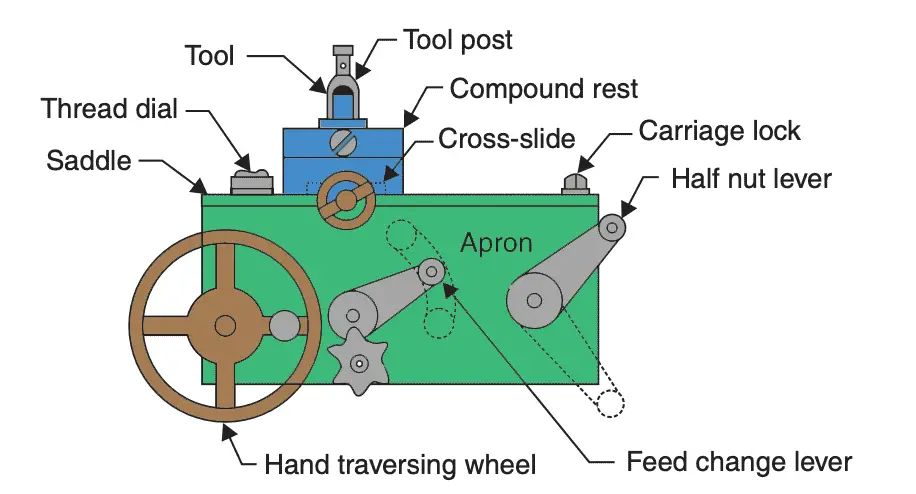
The carriage carries a cross slide, which can independently move in a crosswise direction at right angles to the bed. The cross slide can also be moved either manually through a smaller handwheel or an automatic device. Mounted upon the cross slide is another small slide, called the compound rest (or tool post slide) which can be rotated in a horizontal plane. Its normal position at 0° rotation is parallel to the bed. Its angle of rotation can be read off on a protractor. This compound rest is used during taper turning to set the tool for angular cuts. The compound rest can be moved only manually. The cutting tool is clamped in the tool post which is mounted on top of the compound rest.
Other Parts of Lathe
The gears, clutches and other mechanism required for giving movement to the carriage and cross slide etc. is hidden from view using an apron (thin steel plate) screwed up on the front face of the carriage. Half hidden in the front are two long shafts, (the screwed one is called the lead screw shaft/rod and the plain one is called the feed shaft/rod) extending from the headstock to the tailstock end.
These two shafts can be engaged one at a time to give longitudinal movement to the carriage. Lead
the screw is only used during the screw cutting operation. Feed shaft is used in other operations like turning. The size of a lathe is specified by the distance between headstock chuck to tailstock centre. This is the length of the longest job which can be accommodated or machined on the lathe. In addition, the swing of the lathe (i.e., the vertical distance between the chuck centre and the lathe bed) is specified as this is the radius of the largest workpiece which can be turned on the machine.
Operations performed with Lathe Machine
In a centre lathe, the workpiece is held and fastened in a chuck. If a component is manufactured out of a round bar, the bar passes through the hollow spindle of the headstock, and the required length of the bar is pulled out and then clamped in the jaws of the chuck, the free end of the bar projecting towards the tailstock end. Mostly the movement of the tool is from right to left.
This is known as right hand working. Sometimes, it becomes necessary to do some work while moving tools from left to right, i.e., left hand working. The tools for right-hand lathe operations are quite different from tools for left hand working. They are mirror images of each other.
Many different kinds of operations are carried out on lathes such as
(i) Turning
(ii) Facing
(iii) Taper turning
(iv) Profile turning or Form turning
(v) Parting
(vi) Boring
(vii) Threading
(viii) Knurling
The tools used for these operations are all different. Some of the right-hand tools are shown in the following figure.
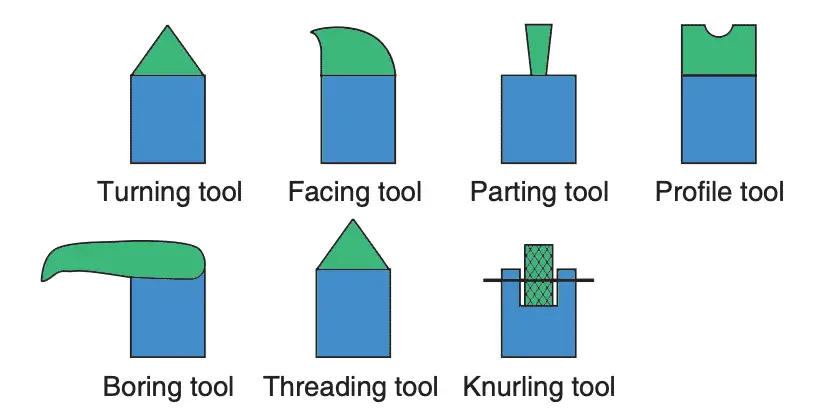
Conclusion
We have discussed what is lathe machine and the operation of the lathe machine. In lathe machine there are 4 main parts which machine bed, tailstock, headstock and carriage are discussed briefly. With this Lathe machine, we can perform many operations such as Turning, Facing, Taper turning, Profile turning or Form turning, Parting, Boring, Threading and Knurling. Let us know in the comment section if you know any operation which we did not mentioned here.
Before starting any we have to know more about that field is very important.this article will give more confidence to start my work on Lathe machines.