Copper is one of the few metals that can occur in nature in a directly usable metallic form. Copper is a pinkish-orange color metal that is very soft, malleable, and ductile metal with very good thermal and electrical conductivity. The copper (Cu) atomic number is 29 from the periodic table. Let us discuss more details on the production of copper and copper alloys.
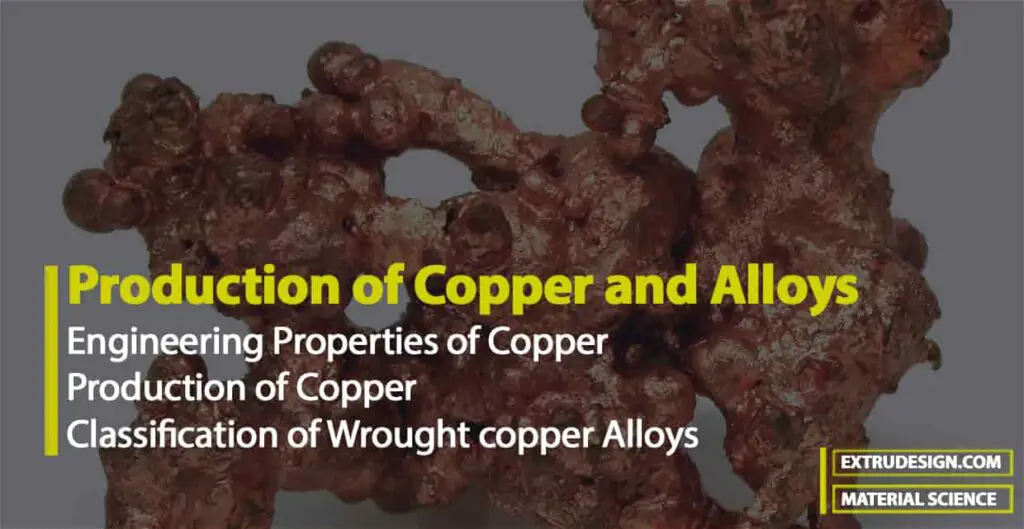
Engineering Properties of Copper
Copper is an important engineering metal and is widely used in unalloyed conditions as well as combined with other metals in the alloyed form.
- In the unalloyed form, copper has an extraordinary combination of properties for industrial applications.
- Some of these are high electrical and thermal conductivity, good corrosion resistance, ease of fabrication, medium tensile strength, controllable annealing properties, and general soldering and joining characteristics.
- Higher strengths are attained in a series of brass and bronze alloys that are indispensable for many engineering applications.
Element Properties of Copper
Atomic number | 29 |
Atomic weight | 63.546 |
Melting point | 1,083°C (1,981°F) |
Boiling point | 2,567°C (4,653°F) |
Density | 8.96 at 20°C (68°F) |
Valence | 1, 2 |
Electron configuration | 2-8-18-1 or (Ar)3d104s1 |
Production of Copper
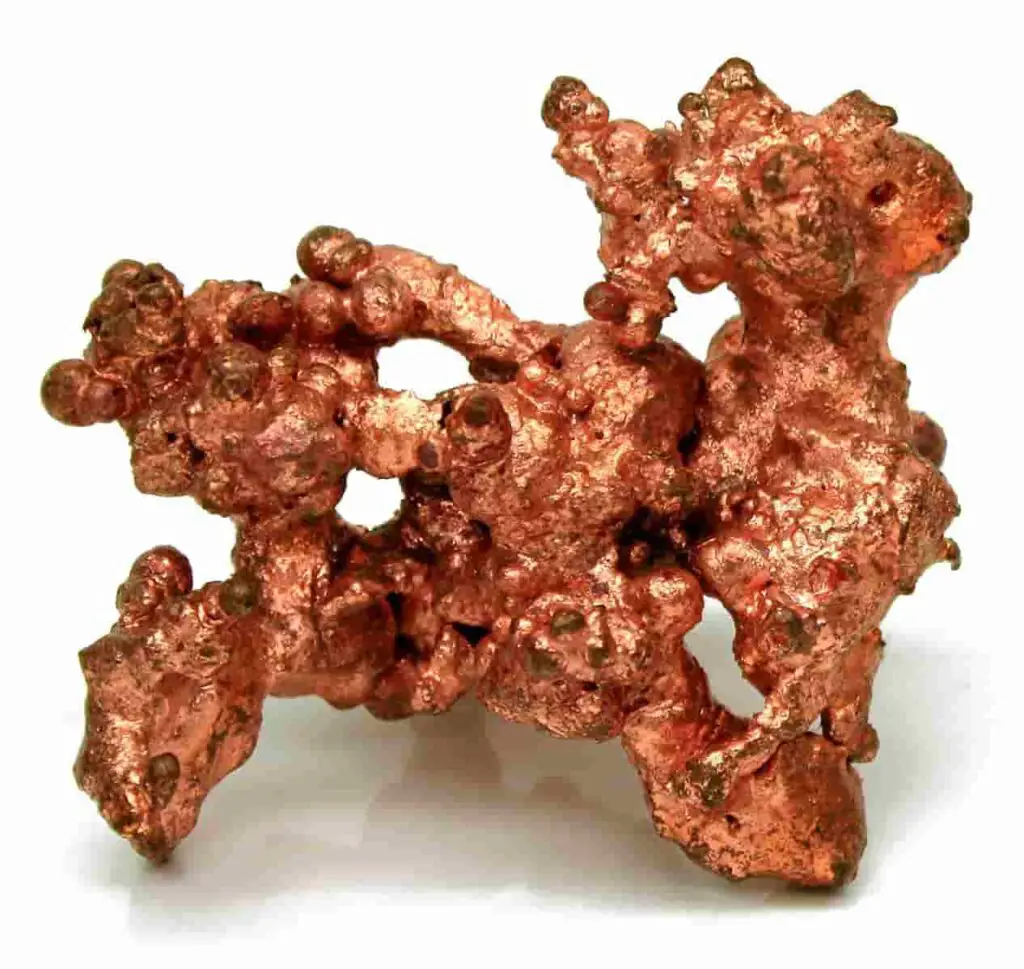
Most copper is extracted from ores containing copper and iron sulfides. Copper sulfide concentrates obtained from lower-grade ores are smelted in a reverberatory furnace to produce a matte that is a mixture of copper and iron sulfides and is separated from slag (waste material). The copper sulfide in the matte is then chemically converted to impure or blister copper (98% + Cu) by blowing air through the matte. The iron sulfide is oxidized first and slagged off in this operation. Subsequently, most of the impurities in the blister copper are removed in a refining furnace and are removed as slag. This fire-refined copper is called tough-pitch copper, and although it can be used for some applications, most tough-pitch copper is further refined electrolytically to produce 99.95% electrolytic tough-pitch (ETP) copper.
Classification of Copper Alloys
Copper alloys in the United States are classified according to a designation system administered by the Copper Development Association (CDA).
In this system, the numbers C10100 to C79900 designate wrought alloys, and the numbers from C80000 to C99900 designate casting alloys. The following table lists the alloy groups of each major level.
Wrought Copper Alloys
Group Name | Alloy Name |
C1xxxx | Coppers and high-copper alloys |
C2xxxx | Copper–zinc alloys (brasses) |
C3xxxx | Copper–zinc–lead alloys (leaded brasses) |
C4xxxx | Copper–zinc–tin alloys (tin brasses) |
C5xxxx | Copper–tin alloys (phosphor bronzes) |
C6xxxx | Copper–aluminum alloys (aluminum bronzes), copper–silicon alloys (silicon bronzes), and miscellaneous copper-zinc alloys |
C7xxxx | Copper-nickel and copper-nickel-zinc alloys (nickel silvers) |
The following table lists the chemical compositions, typical mechanical properties, and applications for some selected Wrought copper alloys.
Chemical compositions, Properties, and Applications of Wrought copper alloys
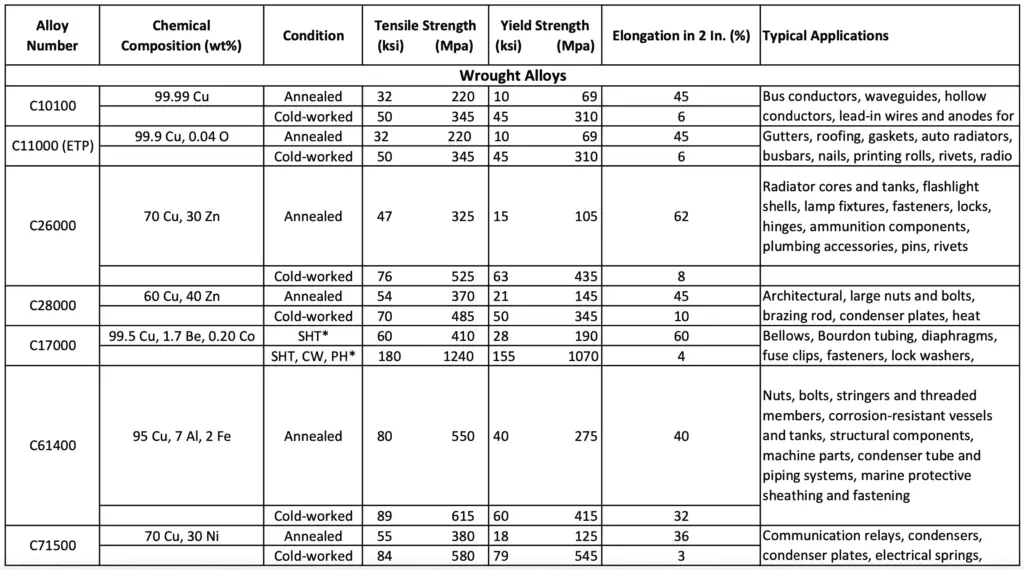
Cast copper Alloys
Group Name | Alloy Name |
C8xxxx | Cast coppers, cast high-copper alloys, cast brasses of various types, cast manganese–bronze alloys, and cast copper-zinc–silicon alloys |
C9xxxx | Cast copper-tin alloys, copper–tin-lead alloys, copper-tin–nickel alloys, copper–aluminum–iron alloys, and copper–nickel-iron and copper-nickel-zinc alloys |
The following table lists the chemical compositions, typical mechanical properties, and applications for some selected copper Cast alloys.
Chemical compositions, Properties, and Applications of Copper Cast alloys
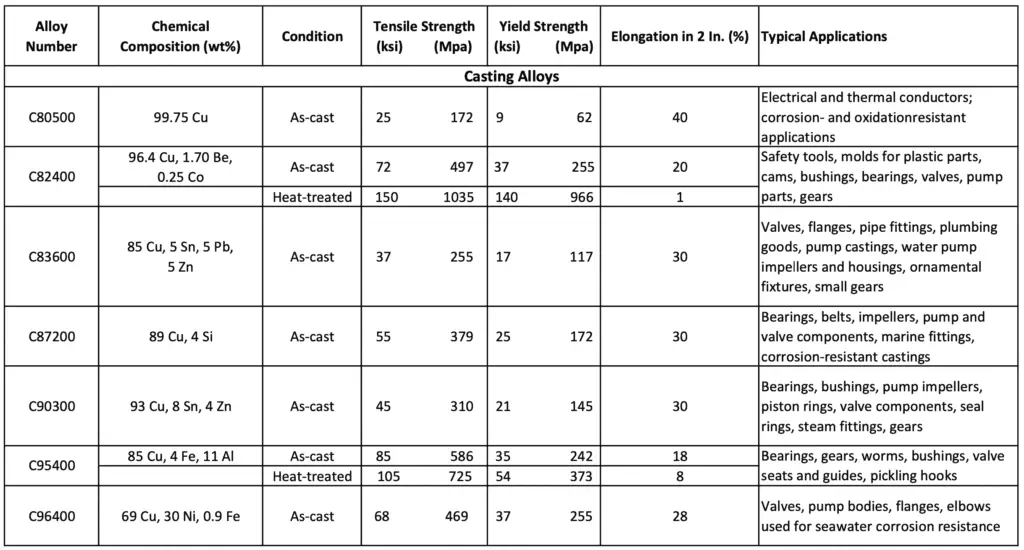
Let us discuss more details on the Wrought Copper Alloys.
Wrought Copper Alloys
Following are the Wrought Copper Alloys that we are going to discuss in brief.
- Unalloyed Copper
- Copper–Zinc Alloys
- Copper–Tin Bronzes
- Copper–Beryllium Alloys
Unalloyed Copper
Unalloyed copper is an important engineering metal, and because of its high electrical conductivity, it is used to a large extent in the electrical industry. Electrolytic tough-pitch (EPT) copper is the least expensive of the industrial coppers and is used for the production of wire, rod, plate, and strip. ETP copper has a nominal oxygen content of 0.04%. Oxygen is almost insoluble in ETP copper and forms interdendritic Cu2O when copper is cast.
For most applications, the oxygen in ETP copper is an insignificant impurity. However, if ETP copper is heated to a temperature above about 400°C in an atmosphere containing hydrogen, the hydrogen can diffuse into the solid copper and react with the internally dispersed Cu2O to form steam according to the reaction
Cu2O + H2 (dissolved in Cu) → 2Cu + H2O(steam)
The large water molecules formed by the reaction do not diffuse readily and so they form internal holes, particularly at the grain boundaries, which makes the copper brittle.
To avoid hydrogen embrittlement caused by Cu2O, the oxygen can be reacted with phosphorus to form phosphorus pentoxide (P2O5) (alloy C12200).
Another way to avoid hydrogen embrittlement is to eliminate the oxygen from the copper by casting the ETP copper under a controlled reducing atmosphere. The copper produced by this method is called oxygen-free high-conductivity (OFHC) copper and is alloy C10200.
Copper–Zinc Alloys
The copper-zinc brasses consist of a series of alloys of copper with additions of about 5% to 40% zinc. Copper forms a substitutional solid solution with zinc up to about 35% zinc. When the zinc content reaches about 40%, alloys with two phases, alpha and beta, form.
The microstructure of the single-phase alpha brasses consists of an alpha solid solution, as shown below the figure for a 70% Cu–30% Zn alloy (C26000, cartridge brass).
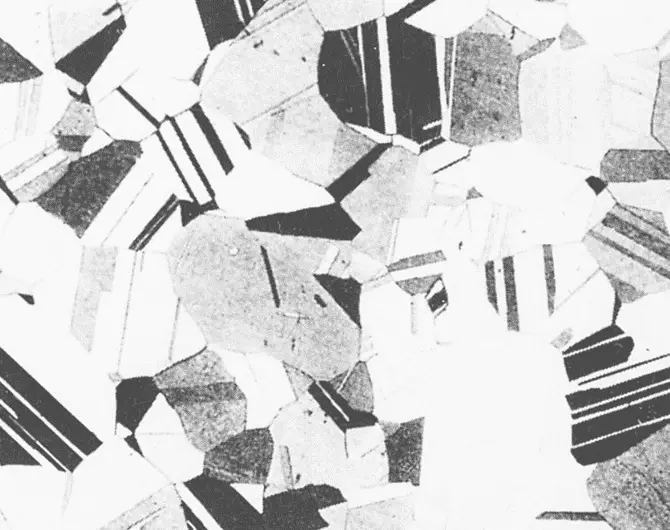
(Etchant: NH4OH + H2O2; magnification 75×.)
The microstructure of the 60% Cu–40% Zn brass (C28000, Muntz metal) has two phases, alpha, and beta, as shown below figure.

(Etchant: NH4OH + H2O2; magnification 100×.)
Small amounts of lead (0.5% to 3%) are added to some Cu–Zn brasses to improve machinability. Lead is almost insoluble in solid copper and is distributed in leaded brasses in small globules as shown in the below figure.
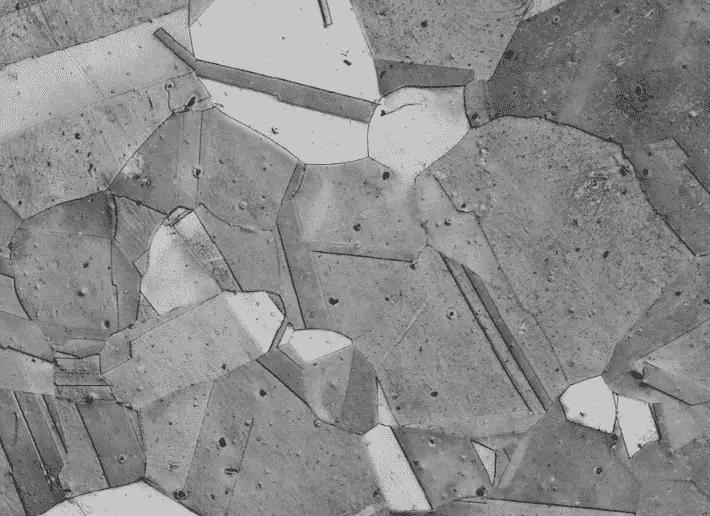
(Etch: NH4OH + H2O2; magnification 62×.)
The tensile strengths of some selected brasses are listed in the above tables. These alloys are of medium strength (34 to 54 ksi; 234 to 374 MPa) in the annealed condition and can be cold-worked to increase their strength.
Copper-Tin Bronzes
Copper–tin alloys, which are properly called tin bronzes but often called phosphor bronzes, are produced by alloying about 1% to 10% tin with copper to form solid-solution-strengthened alloys. Wrought tin bronzes are stronger than Cu–Zn brasses, especially in the cold-worked condition, and have better corrosion resistance, but cost more.
Cu–Sn casting alloys containing up to about 16% Sn are used for high-strength bearings and gear blanks. Large amounts of lead (5% to 10%) are added to these alloys to provide lubrication for bearing surfaces
Copper–Beryllium Alloys
Copper–beryllium alloys are produced containing between 0.6% and 2% Be with additions of cobalt from 0.2% to 2.5%. These alloys are precipitation hardenable and can be heat-treated and cold-worked to produce tensile strengths as high as 212 ksi (1463 MPa), which is the highest strength developed in commercial copper alloys. CuBe alloys are used for tools requiring high hardness and nonsparking characteristics for the chemical industry. The excellent corrosion resistance, fatigue properties, and strength of these alloys make them useful for springs, gears, diaphragms, and valves. However, they have the disadvantage of being relatively costly materials.
Conclusion
This is all about the production of copper and copper alloys. We have discussed Engineering Properties of copper, Production of copper, Classification of Wrought copper Alloys, copper Casting Alloy Compositions in detail, let us know what else we are missing about copper in the comment section below.
Leave a Reply