In the course of Product design and the development, Product Teardown is the process of taking apart a product to understand it and to understand how the company making the product succeeds. Let us discuss more detail on this topic.
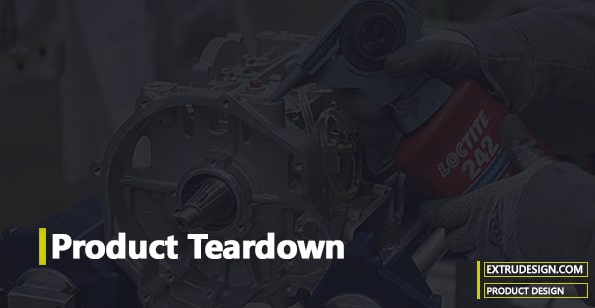
Product Teardown
Before a product to be evolved to the next stage/generation, the current version must be analyzed and understood according to its functions.
By dissecting products, we gain kernels of information on how to accomplish the function. The more we dissect technology, the larger our knowledge base of concepts grows.
Product teardown pertains to competitive benchmarking. The design team must compare the performance with the competitive product.
The main purpose of the product tear down the process is
- Dissection and analysis during reverse engineering
- Experience and knowledge for an individual’s personal database
- Competitive benchmarking
This product teardown process is performed to analyse how the Product Functions are achieved in that product, and how the Components are assembled, how the Corporate and manufacturing strategies working.
Teardown Process
As we have already mentioned the teardown process tightly integrated with the idea of benchmarking, comparing one’s product with the competitive product in the marketplace or Comparing performance with the previous version of their own product. Following are the formal steps in the Product teardown process.
- List Design Issues
- Prepare for Product Teardowns
- Examine the Distribution and Installation
- Disassemble, Measure and Analyze Data by Assemblies
- Form a Bill of Materials
1. List the design issues
- In the case of a new product, Problems and opportunities regarding customer market, competitors, and the features of competitors products should be worth investigating.
- In the case of a redesign, an investigation can ask of the previous design team
- What was difficult for them?
- What design problem did they solve that they are proud of?
- What related technologies were they interested in?
- To help design issues, a companion study of customer needs and predicted product functionality can be executed.
- Predicted functionality of a product helps to focus on the “what” before the “how” and thus can help in forming issues to measure the teardown.
- What predicted functions do they need to achieve the primary goal or overall function?
- The last set of design issues that needs recording is basic information on the components in assemblies
- Factors to be known are
- Quantity of parts per product unit
- Dimensional measurements
- Maximum, minimum and average material thickness
- Weight
- Material
- Colour/finish
- Manufacturing process, including sufficient information for a design for manufacturing analysis
- Geometric, spatial and parameter tolerances
- Primary functions
- Cost per part or sub-assembly
- Other notes
2. Prepare for Product Teardowns
After identifying the design issues, one should identify all tools that will be required to complete the teardown process.
Sensors, Flowmeter, Test equipment, Optical sensor, Camera, Dynamometer, Videotape, Calipers, Multimeter, strobe and Hardness tester.
3. Examine the Distribution and Installation
Examine the decision-making process such as means to acquire parts, contain them, ship, distribute and market the product. Customer installation instructions and procedures should be examined for costs, effectiveness and liability.
4. Disassemble, Measure and Analyze Data by Assemblies
- Disassembly is the obvious step commonly pictured when thinking of reverse engineering.
- This step has to be coordinated with measurements and experimentation
- Take apart the assembly
- Take pictures in the exploded view
- Take measurements of the parts
- Avoid destructive testing during the first iteration
- Parts with permanent joints should be carefully disassembled so that the product could still function
- Parts that are manufactured with insert moulds, rivets, welds, plastic sonic welds, solder, integral components (windings on motor, coil springs in mechanical clocks) should be carefully disassembled
5. Form a Bill of Materials
The complete data collected (pictures and dimensions of parts) should be compiled in a good format for further analyses, including cost and performance. Fill a written form that details the product. The sequence of assembly photos and exploded view CAD drawing.
Teardown methods
We have 3 methods of teardown process as we mentioned below.
- Subtract and Operate Procedure
- Force Flow (Energy Flow Field) Diagrams
- Measurement and Experimentation
We will discuss these topics in the next articles.
Conclusion
We have discussed what is the Product Teardown process and discussed the steps involved in it. If you have any thoughts about this topic, let us know in the comment section below.
[…] What is the Product Teardown Process? […]