In material science, Fracture is the separation, or fragmentation, of a solid body into two or more parts under the action of stress. The process of fracture can be considered to be made up of two components, crack initiation and crack propagation. According to the Strain to fracture behavior of metals, there are two types of Fracture in Metals Ductile Fracture and Brittle Fracture. Let us discuss them in more detailed manner.
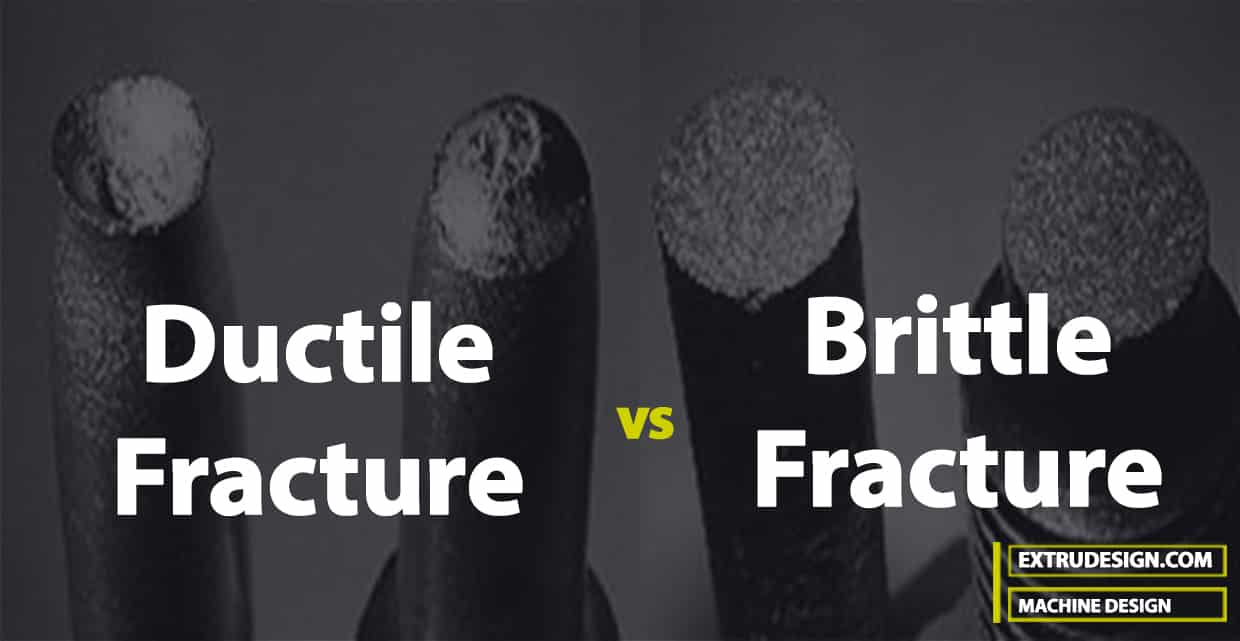
As we have already mentioned that according to the Strain to fracture behavior of metals, there are two types of Fracture in Metals Ductile Fracture and Brittle Fracture. In the previous article we have discussed many other types of fractures in metals. But these two Ductile Fracture and Brittle Fracture are the broad classification of fractures. Some times the fracture can be combination of both Ductile and Brittle.
Ductile Fracture
Ductile fracture of a metal occurs after extensive plastic deformation.
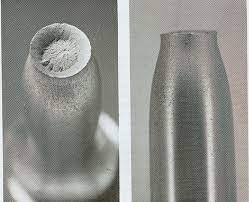
For simplicity let us consider the ductile fracture of a round tensile specimen. If a stress is applied to the specimen that exceeds its ultimate tensile strength and is sustained long enough, the specimen will fracture.
Three distinct stages of ductile fracture can be recognized in the below schematic representation of a ductile spacemen.
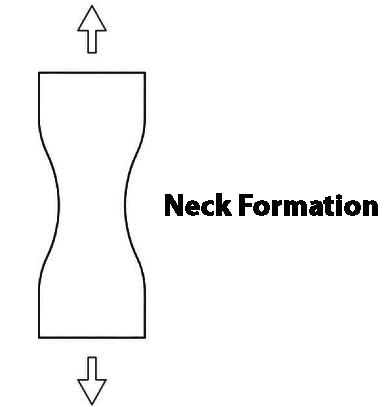
- The specimen forms a neck, and cavities form within the necked region (Necking)
- The cavities in the neck coalesce into a crack in the centre of the specimen and propagate toward the surface of the specimen in a direction perpendicular to the applied stress (Crack initiation and Propagation)
- When the crack nears the surface, the direction of the crack changes to 45° to the tensile axis and a cup-and-cone fracture results (Fracture).
In practice ductile fractures are less frequent than brittle fractures. The main cause for the ductile fracture occurrence is overloading of the component. Overloading could occur as a result of following reasons.
(a) Improper design, including the selection of material(under designing)
(b) Improper fabrication
(c) component is used at load levels above that allowed by the designer
An example of a ductile failure is given in following image. In this figure the drive shaft of an offroad vehicle is shown that has undergone significant plastic twisting. It is clear from torsion marks on the shaft due to applied torsion. As we mentioned above, the reason for the failure could be any of the above mentioned reasons.
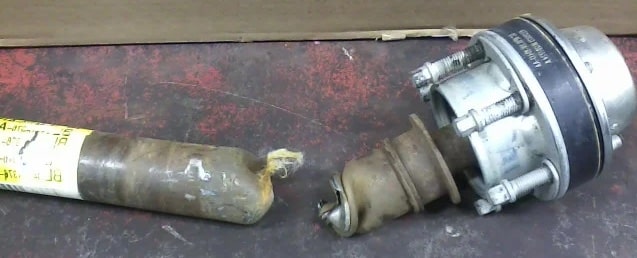
Based an engineering analysis, the cause of this failure has been attributed to excessive load taken up by the driveshaft than the allowed design limit by the engineer.
Brittle Fracture
Many metals and alloys fracture in a brittle manner with very little plastic deformation.
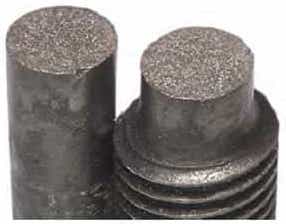
Above example shows a tensile specimen that failed in a brittle manner. Comparison of this figure with above ductile fracture reveals the drastic differences in the deformation level prior to fracture between ductile and brittle fractures.
Brittle fracture usually proceeds along specific crystallographic planes called cleavage planes under a stress normal to the cleavage plane.
Many metals with the HCP crystal structure commonly show brittle fracture because of their limited number of slip planes.
A zinc single crystal, for example, under a high stress normal to the (0001) planes will fracture in a brittle manner. Many BCC metals such as a iron, molybdenum, and tungsten also fracture in a brittle manner at low temperatures and high strain rates.
Most brittle fractures in polycrystalline metals are transgranular, i.e., the cracks propagate across the matrix of the grains. However, brittle fracture can occur in an intergranular manner if the grain boundaries contain a brittle film or if the grain boundary region has been embrittled by the segregation of detrimental elements.
Brittle fracture in metals is believed to take place in three stages:
- Plastic deformation concentrates dislocations along slip planes at obstacles.
- Shear stresses build up in places where dislocations are blocked, and as a result microcracks are nucleated.
- Further stress propagates the microcracks, and stored elastic strain energy may also contribute to the propagation of the cracks.
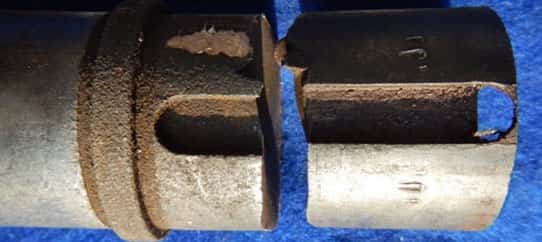
Causes of Brittle fracture
- In many cases brittle fractures occur because of the existence of defects in the metal. These defects are either formed during the manufacturing stage or develop during service.
- Undesirable defects such as folds, large inclusions, undesirable grain flow, poor microstructure, porosity, tears and cracks may form during manufacturing operations such as forging, rolling, extrusion, and casting.
- Fatigue cracks, embrittlement due to the atomic hydrogen, and corrosion damage often result in final brittle fracture.
- When brittle fracture occurs, it consistently initiates at the defect location (stress risers) regardless of the cause for the formation of the defect.
- Certain defects, low operating temperatures, or high loading rates may also cause the brittle fracture of some moderately ductile materials.
- The transition from ductile to brittle behavior is called a ductile to brittle transition (DBT). Thus, ordinarily ductile materials can, under certain circumstances, fracture in brittle manner.
- Following image shows the brittle fracture of a shaft due to the existence of a sharp corner as the defect, note the chevron pattern pointing toward the origin of the fracture.
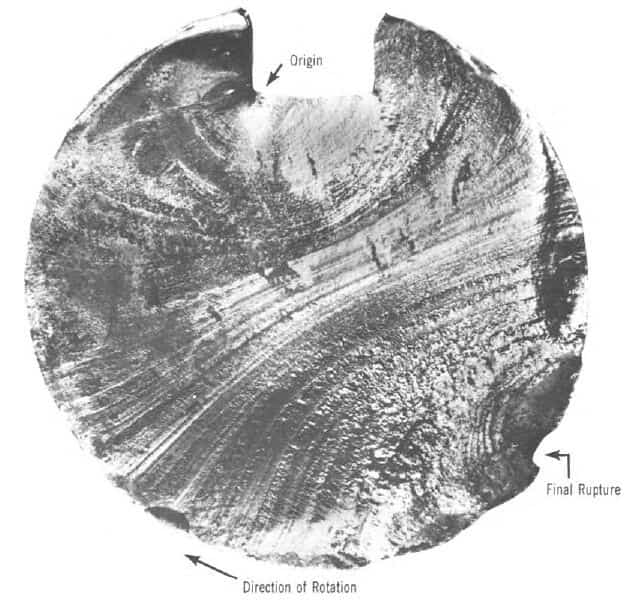
Ductile to Brittle Transition Temperature (DBT)
As mentioned above, under certain conditions a marked change in the fracture resistance of some metals is observed in service, which is called ductile to brittle transition. Low temperatures, high stress states, and fast loading rates may all cause a ductile material to behave in a brittle manner.
- However, customarily the temperature is selected as the variable that represents this transition while the load rate and stress rate are held constant.
- The impact testing, apparatus discussed in the previous article may be used to determine the temperature range for the transition from ductile to brittle behaviour of materials.
- The temperature of the Charpy specimen may be set using furnace and refrigeration units.
- Although some metals show a distinct DBT temperature for many this transition occurs over a range of temperatures.This is shown in the below graph
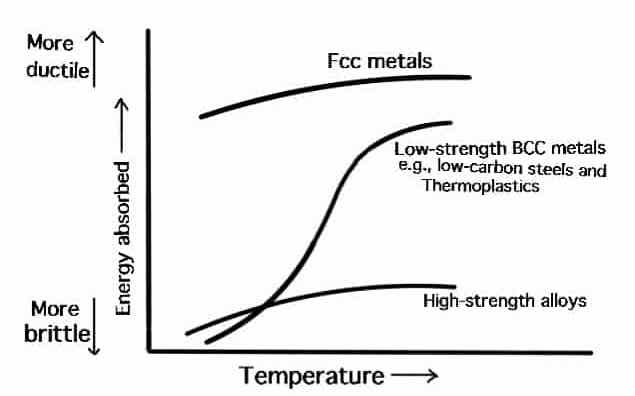
- The above Graph shows that FCC metals do not undergo DBT and, as a consequence, are suitable for low temperature use.
- Factors that Influence the DBT temperature are alloy composition, heat treatment, and processing.
- For instance, the carbon content of annealed steels affects this transition temperature range. This is shown in the below graph.
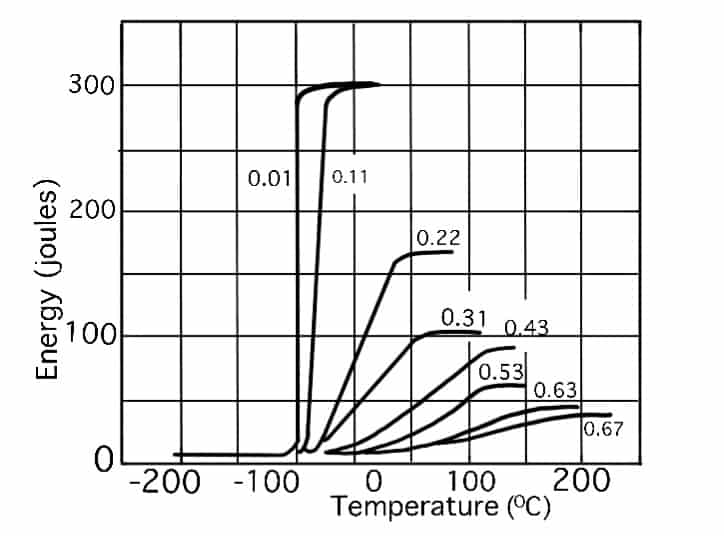
- Low-carbon annealed steels have a lower temperature transition range and a narrower one than high-carbon steels.
- Also as the carbon content of the annealed steels is increased, the steels become more brittle, and less energy is absorbed on impact during fracture.
Ductile to brittle transition is an important consideration in materials selection for components that operate in cold environments. For instance, ships that sail in cold waters and offshore platforms that are located in the arctic seas are especially susceptible to DBT. For such applications, the selected materials should have a DBT temperature that is significantly lower than the operating or service temperature.
Conclusion
We have understood that the Ductile fracture is mainly happens because of mainly overloading of the component, and it is less frequent than the brittle fractures. Brittle fractures are mainly occurs because of existence of defects in the metal due to forming of the material or fabrication process. And this brittle fracture is more frequent than the ductile fracture. Some time a combined fractures also possible. And one of the most important aspect is the Ductile to Brittle Transition Temperature of metals which cause of the brittle fracture. We must prevent the Brittle fractures at all cost. Let us know what do you think about these topic in the comment section below.
Leave a Reply