In sheets metal works, press working is a production technology of sheet metal components using machine presses. Mechanical and hydraulic press machines are also used for similar production technologies such as forging, extrusion and rolling. Let us discuss more details about Press working and the Die-punch assembly and their tools.
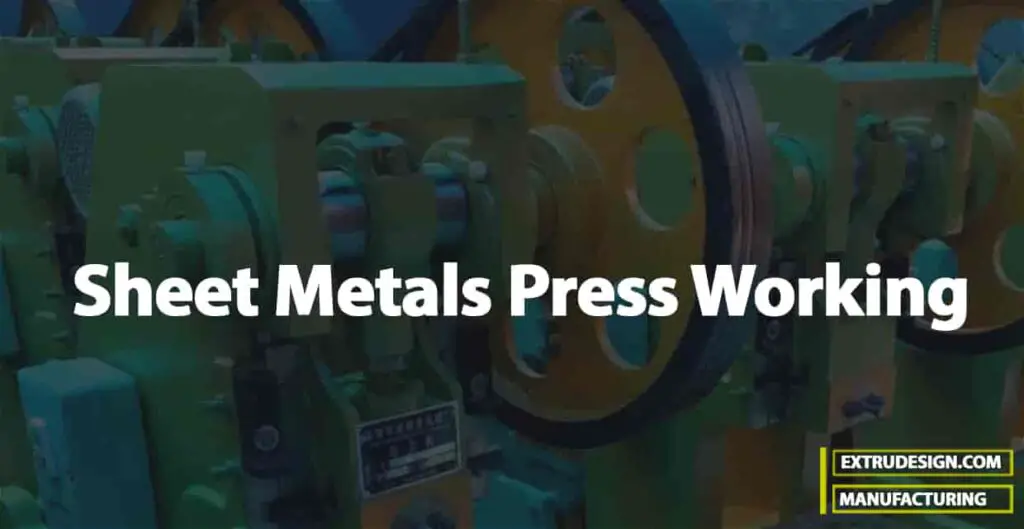
Presses
The machines used for producing the sheet metal components are called the presses.
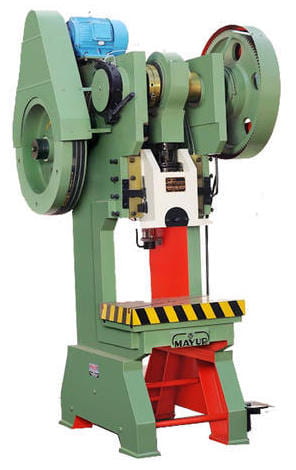
- Knuckle type mechanical presses are used widely for sheet metal work.
- These presses are usually of vertical configuration.
- These presses are provided with a heavy flywheel driven by an electric motor.
- A ram moves up and down the guideways provided in the frame of the press when the ram is connected to the flywheel through a connecting rod and a crank mechanism.
- The clutch for transferring the motion from the flywheel to the ram is operated by a foot-operated treadle.
- The arrangement is somewhat similar to the mechanism of a reciprocating engine.
- Such presses are very useful for providing short powerful strokes.
These presses are available in two configurations:
- Open Frame Type
- Closed Frame Type
Open frame type presses are less robust as compared to closed frame type, but provide greater access for loading material as they are open in the front as well as sides. Due to their appearance, they are also referred to as C-frame or gap presses as well.
Closed frame type presses are used for heavier work.
The capacity of the press is indicated by the force (or tonnage), the press is capable of exerting.
Die-Punch Assembly for Sheet Metal
A die and punch assembly for making holes in metal sheets is shown in the following figure.
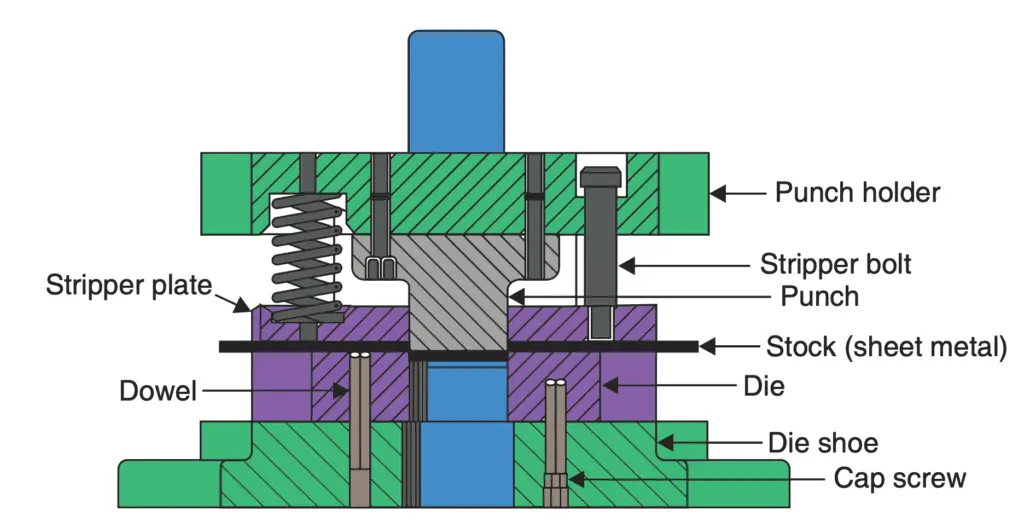
A set of dies are required tooling for working with the presses. A die set consists essentially of three
parts.
(a) a punch (male tool)
(b) a die (a female tool)
(c) a stripper plate
a. Punch
The Punch is fixed or bolted to the ram and the die is fixed on the machine bed in such a manner that the two are in perfect alignment. When the punch along with the ram of the press moves downwards, the punch passes centrally through the die.
b. Die
When the punch descends, it shears the metal sheet. The hole punched through has the same profile as the punch. If the remaining portion of the sheet metal is the useful part, the punched out portion is thrown away as scrap. In this case, the operation is called “punching”. However, if the punch-out portion is the useful part, the operation is termed “blanking” and the punched out piece is referred to as blank. The size of the blank is determined by the size of the hole in the die.
Question: Did you understand What is the difference between Punching and Blanking?
c. Stripper Plate
The function of the stripper plate is to keep the sheet held down during the subsequent upward movement of the punch; otherwise, the sheet may get entangled with the punch during the upward movement of the ram and the punch.
For efficient operation and clean-cut surfaces, some clearance is provided between the punch and the die. It is a function of the thickness of the sheet under shear and is 3–5% of the thickness. Actually, after the bottom surface of the punch comes into contact with the sheet, it travels or penetrates through the sheet up to about 40% of the sheet thickness inducing higher and higher compressive stress in the sheet metal. Ultimately, the resultant shear stress at the perimeter of the blank exceeds the maximum shear strength of the material and the blanks get sheared off through the remaining 60% of the sheet thickness. The depth of penetration-zone and shear zone is demarcated and easily seen if the periphery of the blank is examined visually.
The shear force Vs thickness graph is typical and is shown in the following figure.
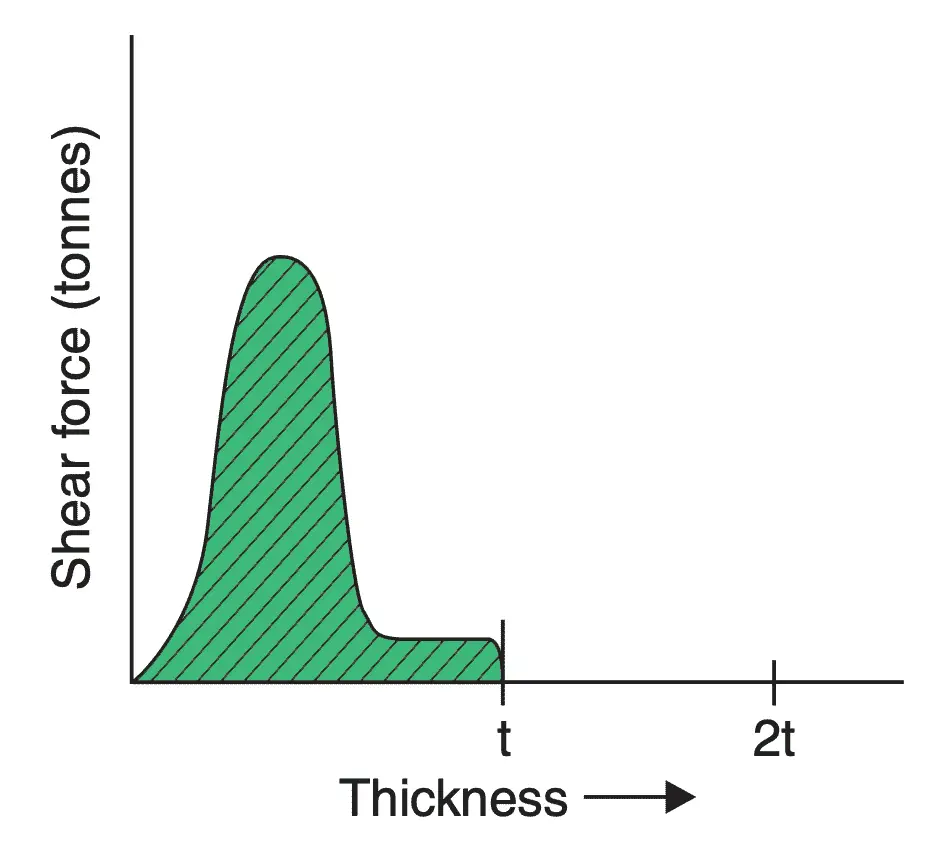
The area under this curve as shown with the shaded portion gives the energy required for the shearing operation. The die and punch are made of high quality, fine-grained alloy steel. They are then heat-treated to develop high hardness, wear resistance and impact resistance.
Sometimes, when no press capable of exerting full shear force is available, the bottom surface of the punch is given a taper. This is known as “shear”. Provision of shear reduces the maximum force required as the entire periphery of the punch will not bear on the sheet metal simultaneously.
What is Guillotine Shear?
You may have noticed, that for all press work, the raw material is in the form of sheets or plates. Commercially, sheets and plates are available in sizes 2500 × 1000 mm or 2500 × 1250 mm. They have to be cut into smaller rectangular or square pieces, as per sizes required before other operations like, bending, punching etc. are performed. For cutting sheets into smaller pieces with straight cuts, guillotine shears, (which are also mechanical presses) are used.
Guillotine shears are provided with two straight blades of adequate length made of die steel. The blades are hardened and finished by grinding to give smooth and sharp edges. One blade is fixed to the ram (which is much longer in the case of guillotine shear), while the other one is fixed to the edge of the machine bed in the manner shown in the following figure.
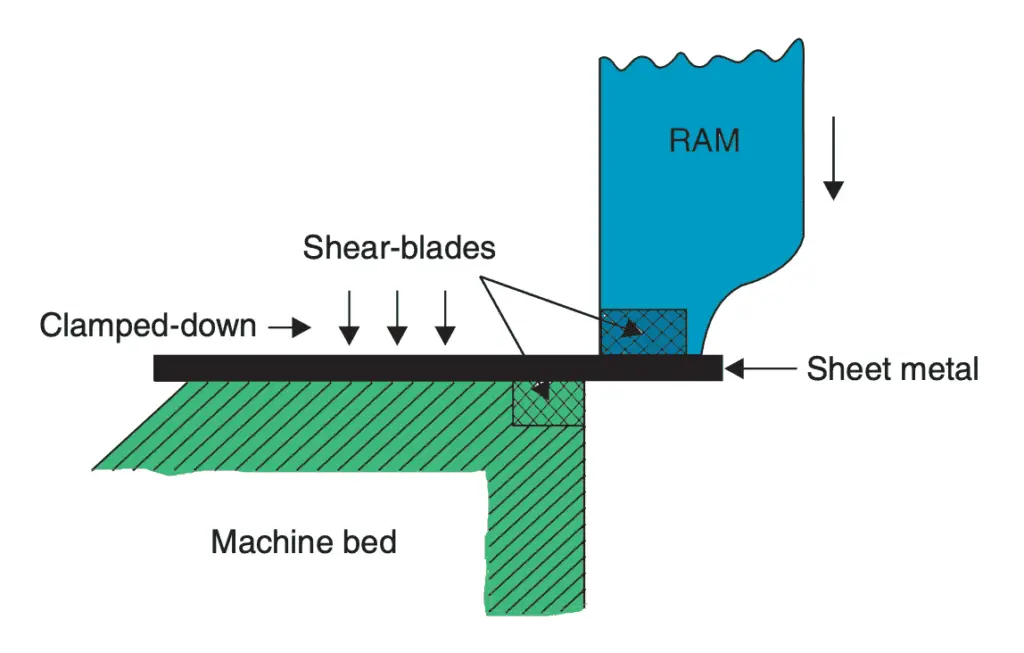
The sheet is placed on a machine bed with one end projecting. It is held down by a clamp. When the ram moves down, the blades shear the sheet along the blade length. Steel plates up to 10 mm thick can be sheared in this way on 250-tonne presses. No sheet-metal shop is complete without a guillotine shear.
Conclusion
The press working for sheet metals is very popular production technology to produce the sheet metal components. We have discussed different types of presses and also discussed about the main Die-punch assembly with a detailed schematic diagram. Also discussed the sheetmetal cutting technology. Let us know what do you think about this article inn the comment section below.
Very good and useful articles