In metalworks, Rolling is the process of deforming metals or alloys to the required shape or thickness. In the previous article, we have discussed what Rolling and Rolling procedures are and the mechanism. Let us now discuss different types of Rolling in Metalworks.
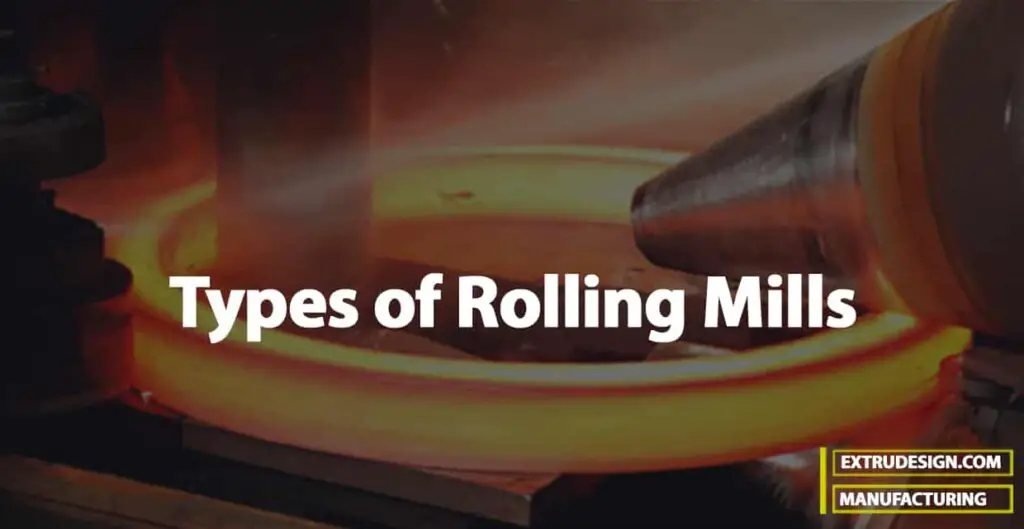
In this Rolling process, metals and alloys are plastically deformed into semifinished or finished products by being pressed between two rolls that are rotating. The metal is initially pushed into the space between two rolls, thereafter once the roll takes a ‘‘bit’’ into the edge of the material, the material gets pulled in by the friction between the surfaces of the rolls and the material. Rolling can be done in both hot and cold conditions. Let us now discuss different types of Rolling mills based on Hot Rolling.
Different Types of Rolling Mills
Following are the Different types of rolling mills.
- Two High Mills
- Three High Mills
- Four High Mills
- Cluster Mills
Let us discuss these Different types of Rolling mills in brief.
1. Two High Rolling Mills
- It comprises two heavy rolls placed one over the other.
- The rolls are supported in bearings housed in sturdy upright frames (called stands) which are grouted to the rolling mill floor.
- The vertical gap between the rolls is adjustable.
- The rolls rotate in opposite directions and are driven by powerful electrical motors.
- Usually, the direction of rotation of rolls cannot be altered, thus the work has to be fed into rolls from one direction only.
- A two-high rolling mill arrangement is shown in the below figure.
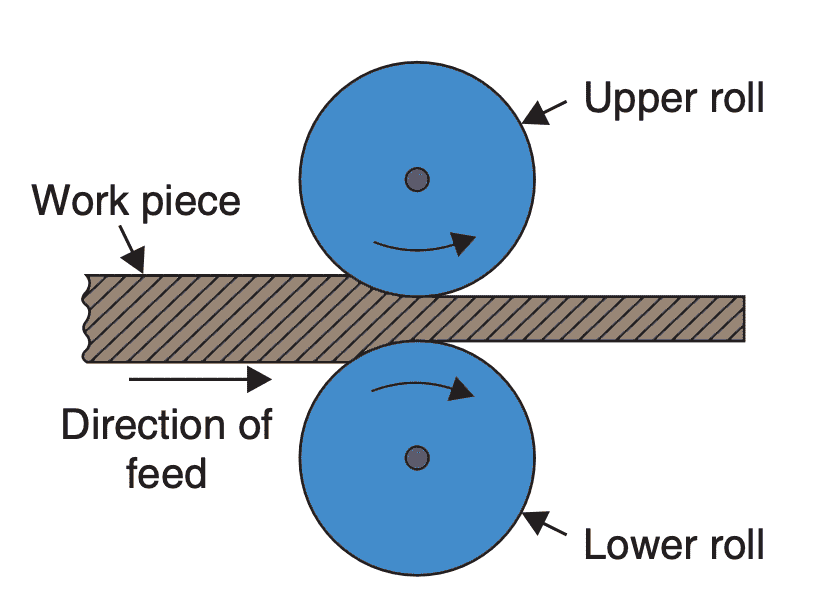
- If rolling entails more than one ‘pass’ in the same set of rolls, the material will have to be brought back to the same side after the first pass is over.
- Since transporting material (which is in red hot condition) from one side to another is difficult and time-consuming (material may cool in the meantime), a ‘‘two high reversing mill’’ has been developed in which the direction of rotation of rolls can be changed.
- This facilitates the rolling of material by passing it through back and forth passes.
2. Three High Rolling Mills
A three high rolling mill arrangement is shown in the below figure.
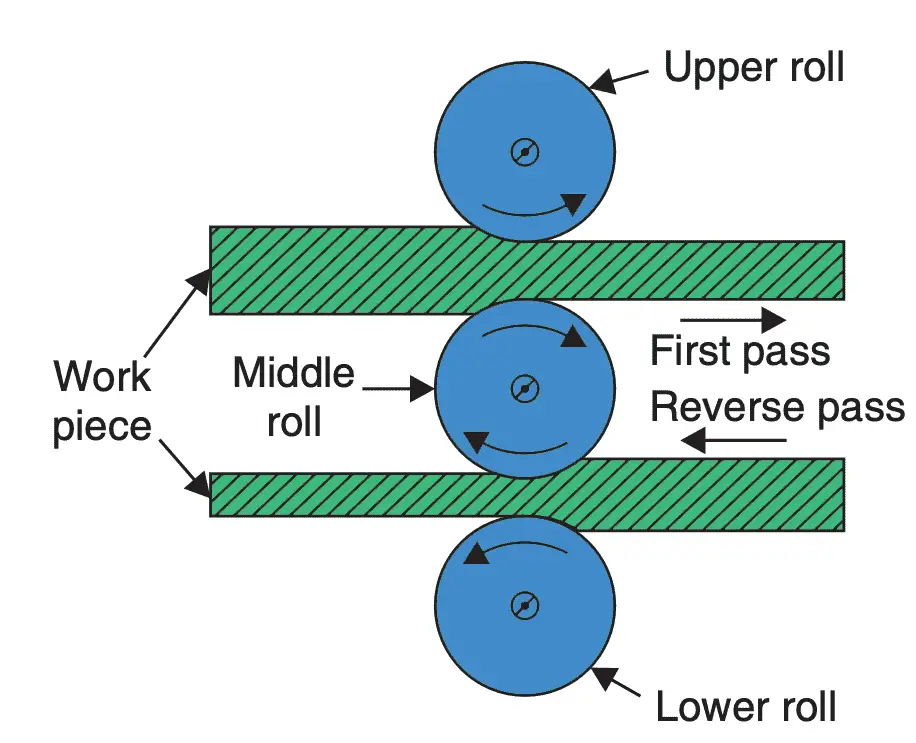
- It consists of three rolls positioned directly over one another as shown.
- The direction of rotation of the first and second rolls are opposite as in the case of two high mills.
- The direction of rotation of the second and third rolls are again opposite to each other.
- All three rolls always rotate in their bearings in the same direction.
- The advantage of this mill is that the work material can be fed in one direction between the first and second rolls and the return pass can be provided between the second and third rolls.
- This obviates the transport of material from one side of rolls to the other after one pass is over.
3. Four High Rolling Mills
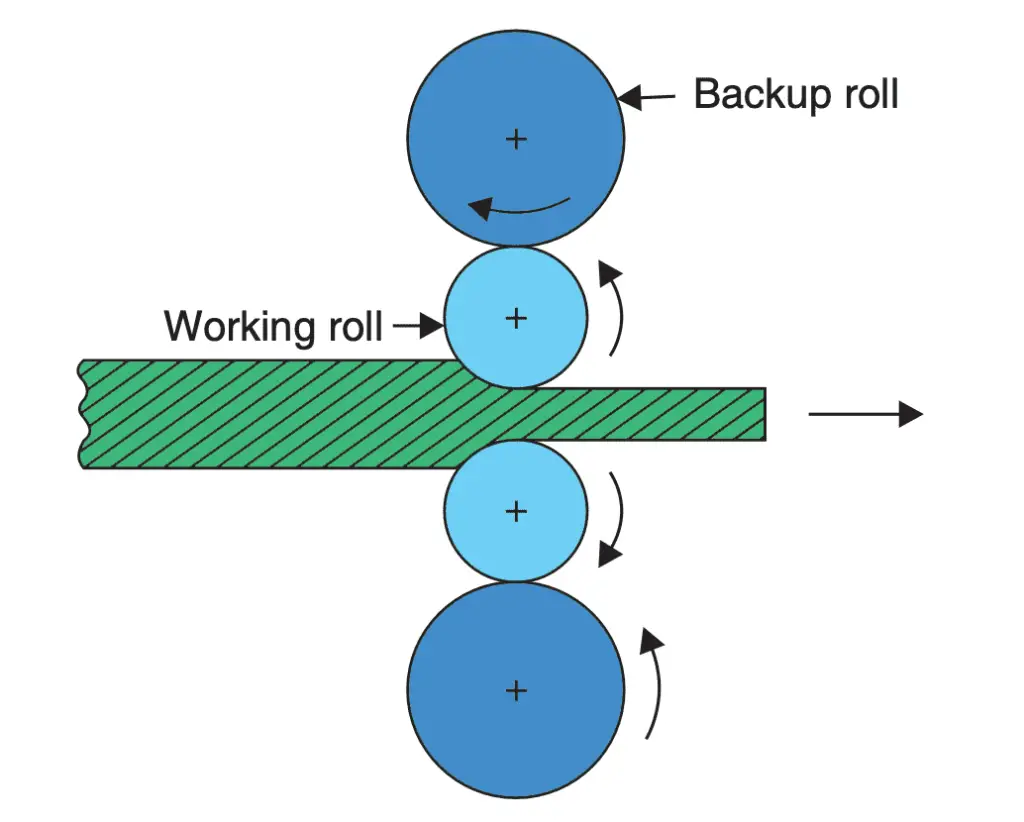
- As shown in the above figure, this mill consists of four horizontal rolls, two of smaller diameter and two much larger ones.
- The larger rolls are called backup rolls.
- The smaller Rolls are the working rolls, but if the backup rolls were not there, due to deflection of rolls between stands, the rolled material would be thicker in the centre and thinner at either end.
- Backup rolls keep the working rolls pressed and restrict the deflection when the material is being rolled.
- The usual products of these mills are hot and cold-rolled plates and sheets.
4. Cluster Mills
It consists of two working rolls of small diameter and four or more backing rolls. The large number of backup rolls provided becomes necessary as the backup rolls cannot exceed the diameter of working rolls by more than 2–3 times. To accommodate processes requiring high rolling loads (e.g., cold rolling of high strength steels sheets), the size of working rolls becomes small. So does the size of backup rolls and a stage may be reached that backup rolls themselves may offer deflection. So the backup rolls need support or backing up by further rolls. In the world-famous SENDZIMIR MILL, as many as 20 backup rolls are used in the cluster. This mill is used for rolling stainless steel and other high strength steel sheets of thin gauge.
Different types of Rolls & Roll Passes in Rolling Mills
There are two types of rolls. One is the Plain roll and the second one is the Grooved roll shown in the below figure.
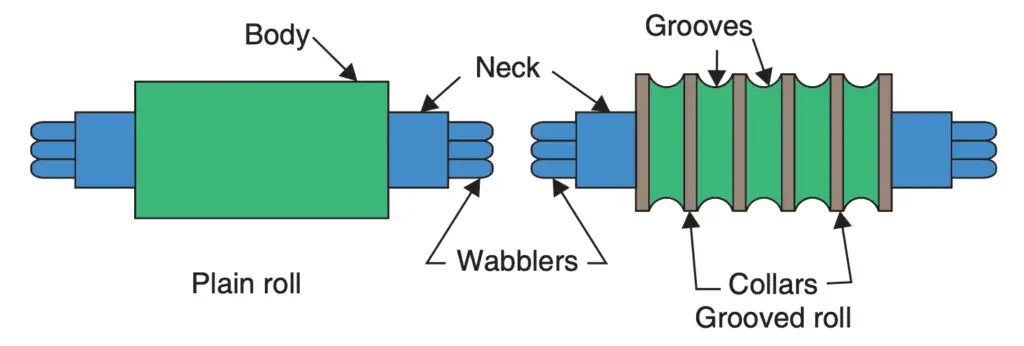
Rolls used for rolling consist of three parts. Body, neck and wobbler.
The necks rest in the bearings provided in the stands and the star-shaped wobblers are connected to the driving shaft through a hollow cylinder.
The wobbler acts like a safety device and saves the main body of the roll from damage if too heavy a load causes severe stress.
The actual rolling operation is performed by the body of the roll.
The rolls are generally made from a special variety of cast iron, cast steel or forged steel. Plain rolls have a highly finished hard surface and are used for rolling flats, plates and sheets. Grooved rolls have grooves of various shapes cut on their periphery.
One-half of the required shape of the rolled product is sometimes cut in the lower roll and one-half in the upper roll so that when the rolls are assembled into their stands, the required shape in full will be produced on the work material, once it passes (i.e., rolled) through the groove in question.
However, it should be understood that the desired shape of the rolled section is not achieved in a single pass. The work material has to be rolled again and again through several passes and each pass brings the cross-section of the material closer to the final shape required. These passes are carefully designed to avoid any rolling defect from creeping in. Rolling is a painstaking process as would be noticed from the scheme of passes shown in the below figure for the conversion of a steel billet into a round bar.
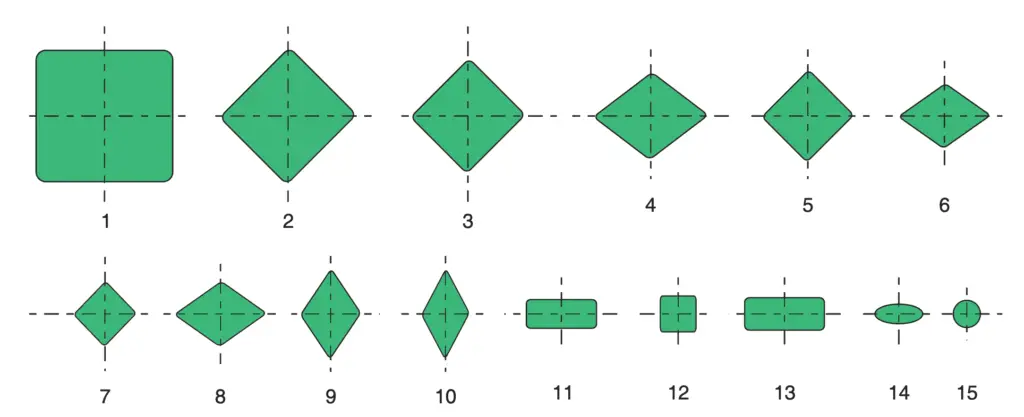
Various passes fall into the following groups
(i) Breakdown or roughing passes,
(ii) Leader passes
(iii) Finishing passes
Breakdown passes are meant to reduce the cross-sectional area. The leader passes gradually and brings the cross-section of the material near the final shape. The final shape and size are achieved in finishing passes. Allowance for shrinkage on cooling is given while cutting the finishing pass grooves.
What is Ring Rolling?
Seamless rings such as the rings without a joint as shown in the below figure has wide application in industry.
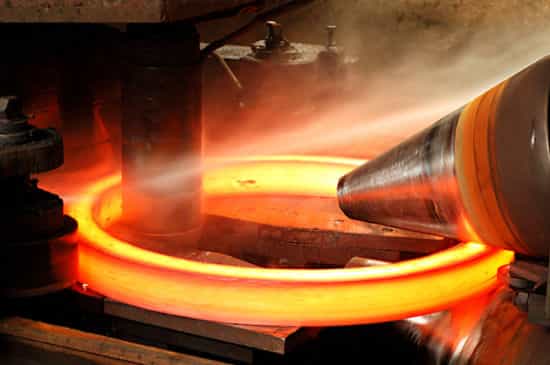
The inner and outer races of the ball and roller bearings, and steel tyres for railway wheels are some such applications. These rings are made by a special rolling process called Ring Rolling.
Ring Rolling Procedure
- The starting workpiece is a thick-walled circular piece of metal in whose centre a hole has been made by drifting and piercing.
- The workpiece is heated until it becomes red hot and then placed between two rolls A and B which rotate in opposite directions.
- The arrangement of the rolls and the ring is shown in the below schematic representation.
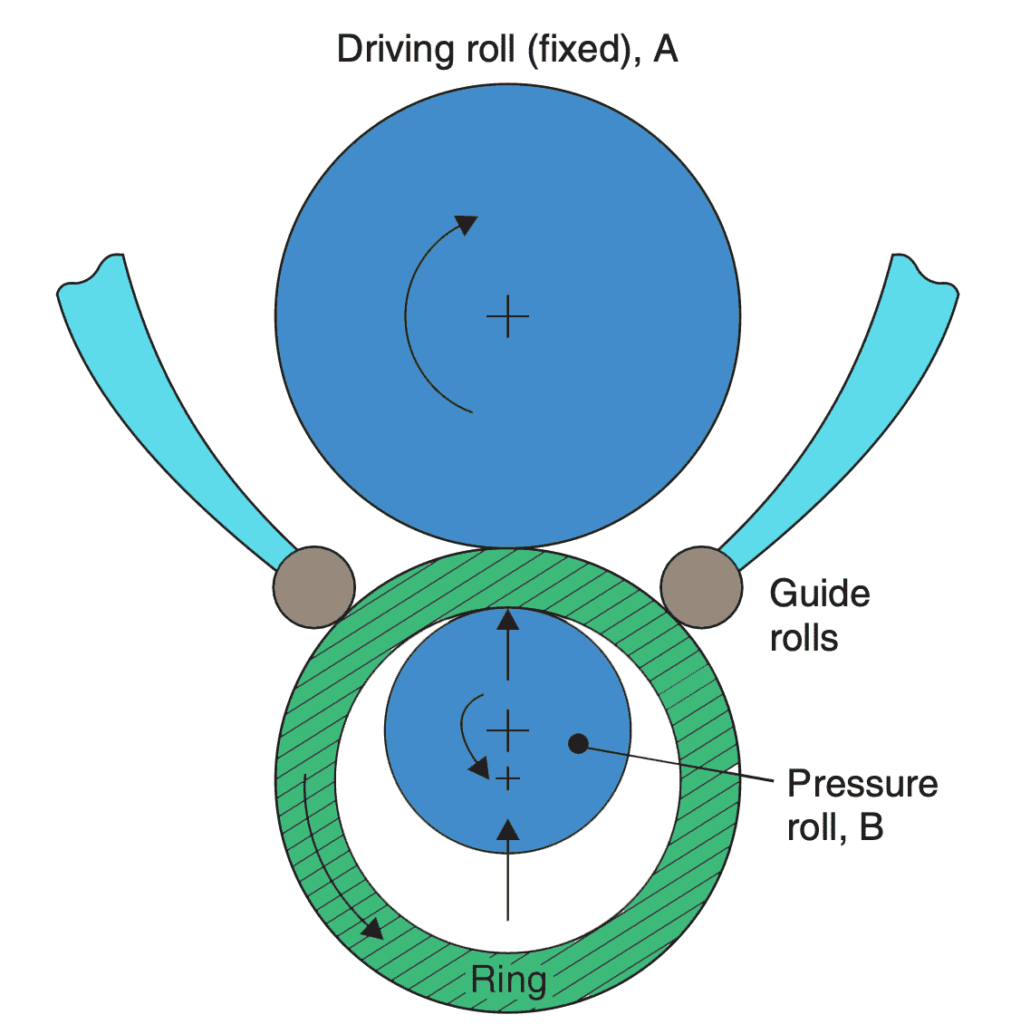
- The pressure roll B exerts pressure on the material from inside.
- Caught between rolls A and B, the ring rotates.
- At the same time, the inside and outside dia of the ring progressively increase and the wall thickness keeps on reducing.
- In order to ensure that the ring is circular, two guide rolls are suitably placed on the outer surface of the ring.
- When the outer and inner dia of the ring increase to the size required, the rolling is stopped.
What is Cold Rolling Process?
The cold rolling process is also similarly performed with the Rolls and the Roll passes as we mentioned above but it has some specific advantages over the Hot Rolling products. Let us see what are some of the Drawbacks of the Hot Rolling processes.
Drawbacks of Hot Rolling Process
Hot rolled steel products look an unattractive greyish-black in colour. Non-ferrous materials also develop tarnished colouring due to oxidation of the outer surface. The surface finish is rough and the finished sizes of hot rolled products are far from satisfactory.
In the case of steel, the oxidation of carbon present on the surface leads to decarburisation. However hot rolling is very economical as due to increased plasticity, large reductions in cross-section are quickly achieved with low energy consumption. A great deal of hot rolled “black” bars and sheets/plates of steel are used in the construction industry for the fabrication of structures.
Thinner gauges, better surface finish, tighter size control and “bright” surfaces are obtained in the cold rolling process. These products also develop greater strength and wear resistance due to strain hardening.
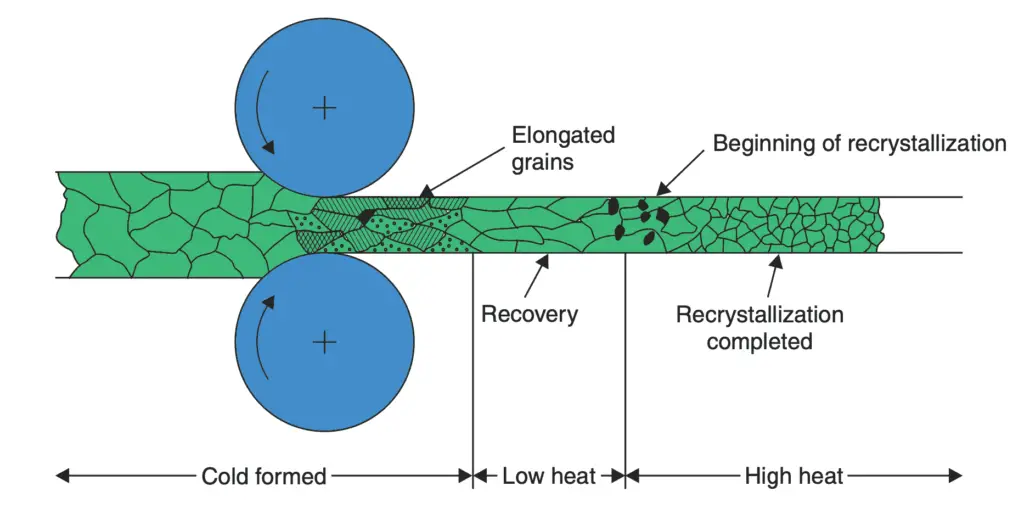
The effect of mechanical work done which is the strain hardening is automatically nullified in the hot rolling process, as recrystallisation in the hot worked material keeps on taking place simultaneously. This is shown schematically in the below figure.
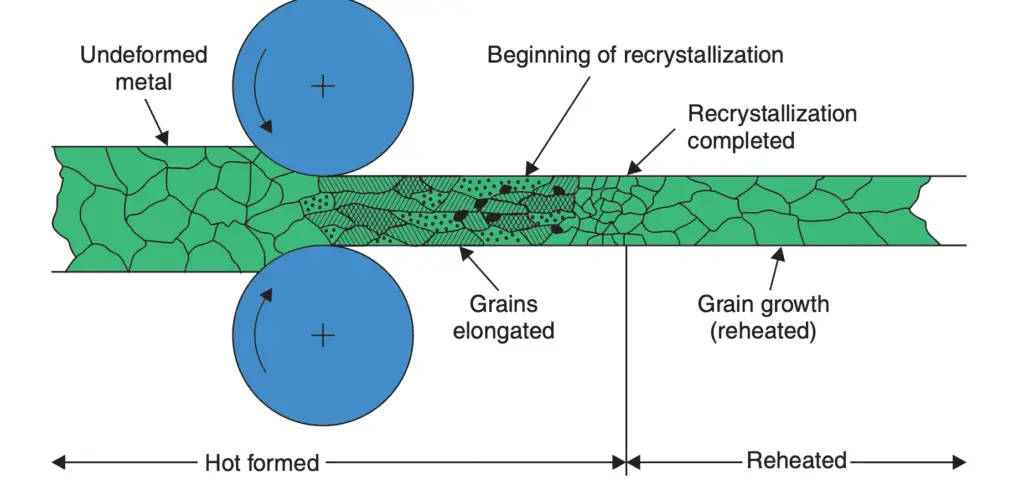
Thus the actual process employed in the industry for the production of small gauge material is hot
rolling to slightly above the finished size required, cleaning/removing the oxidised surface by machining
pickling or some other suitable process and finally using cold-rolling of work material to finished sizes.
Conclusion
We have discussed the different types of Rolling mills types and also discussed the different Roll and Roll passes design that is used in these rolling mills. One of the important methods of the rolling process is Ring rolling. which is described with a schematic diagram. also discussed the differences between the cold rolled and hot rolled products. let us know what you think about this article in the comment section below.
Leave a Reply