In the previous article, we have discussed what is a Press working for sheet metals. The machines used for producing the sheet metal components are called the presses. These presses can be either Mechanical or hydraulic presses which can be used for many sheet metal operations. Let us discuss the Different Operations Performed with Presses in detail.
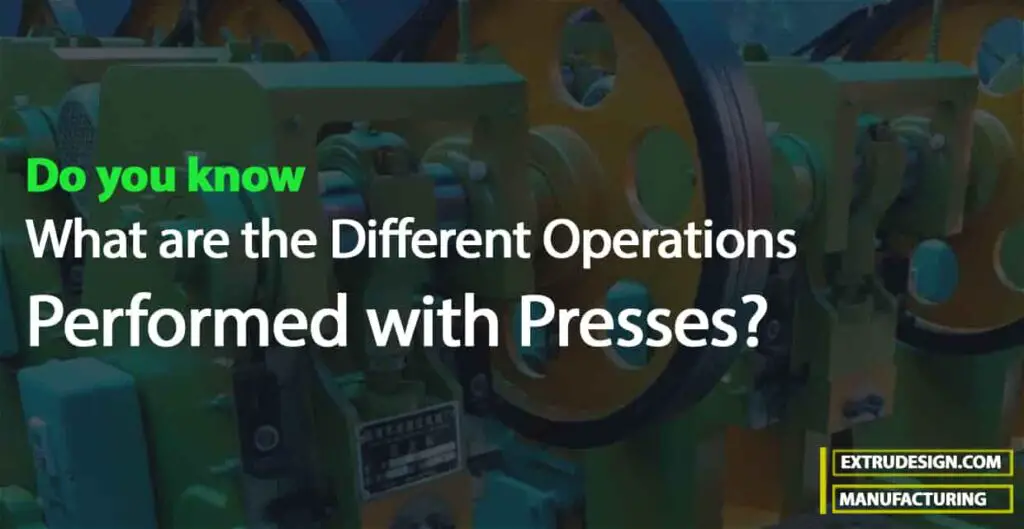
Mostly we have seen that the punching/Blanking is the main sheet metal operation that can be done with the Presses. But there is more to it. There are many other operations that can be done with these Presses.
Different Operations Performed with Presses
These different Sheetmetal operations that can be performed with the Presses are listed as follows.
- Bending
- Deep drawing
- Coining
- Embossing
Let us discuss them briefly with some schematic diagrams.
Bending
In Sheeetmetal works, Bending means deforming a flat sheet along a straight line to form the required angle. Various sections like angles, channels, etc., are formed by bending, which may then be used for the fabrication of steel structures.
Three common methods of bending are illustrated in the following schematic diagram.
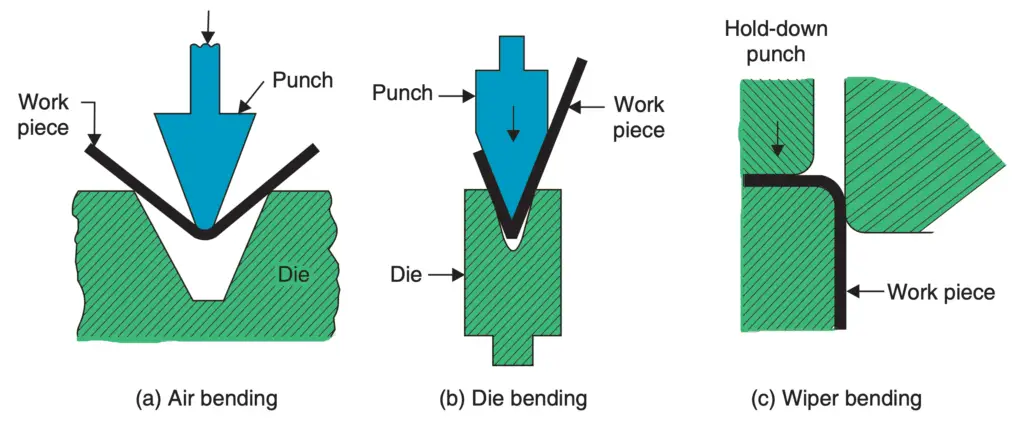
The bending operation is done with the help of a V-shaped punch, a die, and a press specially designed for such work. The stroke of such presses can be controlled at the operator’s will and such presses are called press brakes.
In V-bending, a V-shaped punch forces the metal sheet or a flat strip into a wedge-shaped die. The bend angle will depend upon the distance to which the punch depresses. Bends of 90° or obtuse as well at an acute angle, can be produced.
Wiper bending is used only for 90° bends. Here the sheet is held firmly down on the die, while the extended portion of the sheet is bent by the punch.
Do you know what is Spring back for Sheetmetal works with Presses?
Answer: At the end of the bending operation, after the punch exerting the bending force is retrieved, due to elasticity, there is a tendency for the bend angle to open out. This is called “spring back”. The effect of spring back may be offset by slight overbending in the first place. Other methods to prevent spring back are bottoming and ironing. For low carbon steel spring back is 1– 2°, while for medium carbon steel it is 3–4°.
Deep Drawing
In the deep drawing process, we start with a flat metal plate or sheet and convert it into a cup shape by
pressing the sheet in the centre with a circular punch fitting into a cup-shaped die.
If the depth of the cup is more than half its diameter, the process is termed deep drawing and with a lesser depth to diameter ratio, it is called shallow drawing. Parts of various geometries and shapes are made by the drawing process. The deep drawing process is illustrated in the following figure.
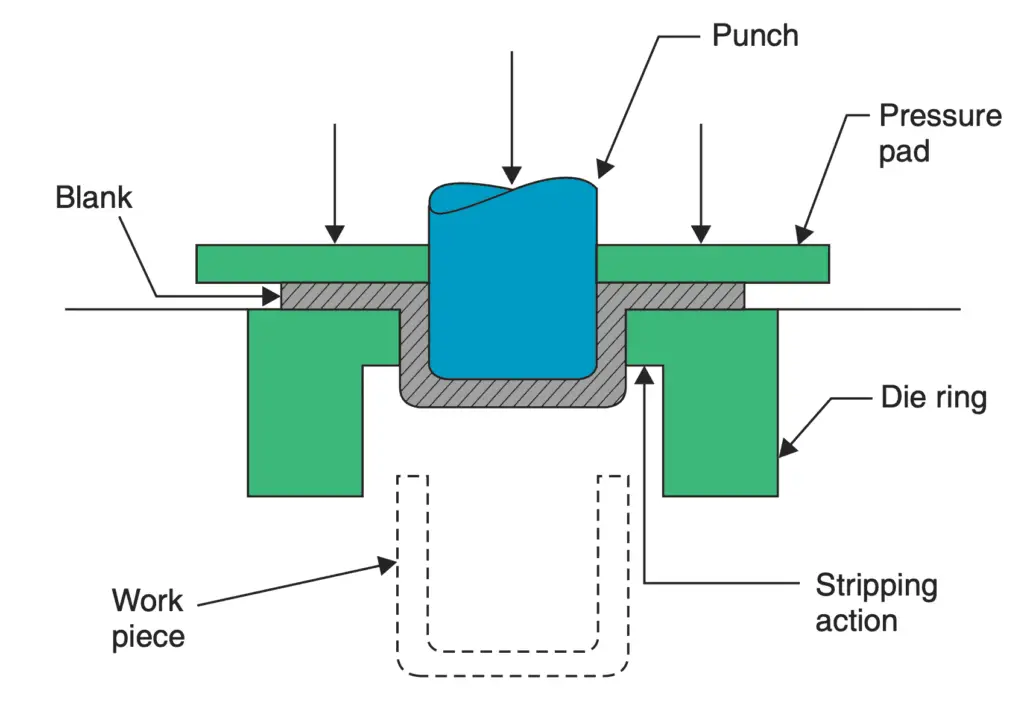
- During the drawing process, the sheet metal part is subjected to a complicated pattern of stress.
- The portion of the blank between the die wall and punch surface is subjected to pure tension, whereas the portion lower down near the bottom is subject both to tension and bending.
- The portion of the metal blank, which forms the flange at the top of the cup is subjected to circumferential compressive stress and buckling and becomes thicker as a result thereof.
- The flange has therefore to be held down by a pressure pad, otherwise, its surface will become buckled and uneven like an orange peel.
- Deep drawing is a difficult operation and the material used should be especially malleable and ductile, otherwise, it will crack under the induced stresses.
- The wall thickness of a deep-drawn component does not remain uniform.
- The vertical walls become thinner due to tensile stresses.
- But the thinnest portion is around the bottom corner of the cup all around.
- This thinning of sheets at these locations is called “necking”.
- After deep drawing, the component may be subjected to certain finishing operations like “growing”, the object of which is to obtain a more uniform wall thickness.
The products made by this Deep drawing process can be found in the household kitchen, we use many vessels like deep saucepans.
Coining
Both coining and embossing operations are done ‘cold’ and mechanical presses with a punch and die are used for these operations.
- In the coining process, a blank of metal that is softened by the annealing process is placed between two dies containing an impression.
- The blank is restricted on its circumference in such a manner, that upon the two dies closing upon the blank, the material cannot flow laterally i.e., sideways.
- The material is only free to flow upwards as a result of which it fills up the depressions in the upper die and downwards when it fills up depressions in the bottom die.
- The Coining process is illustrated in the following figure.
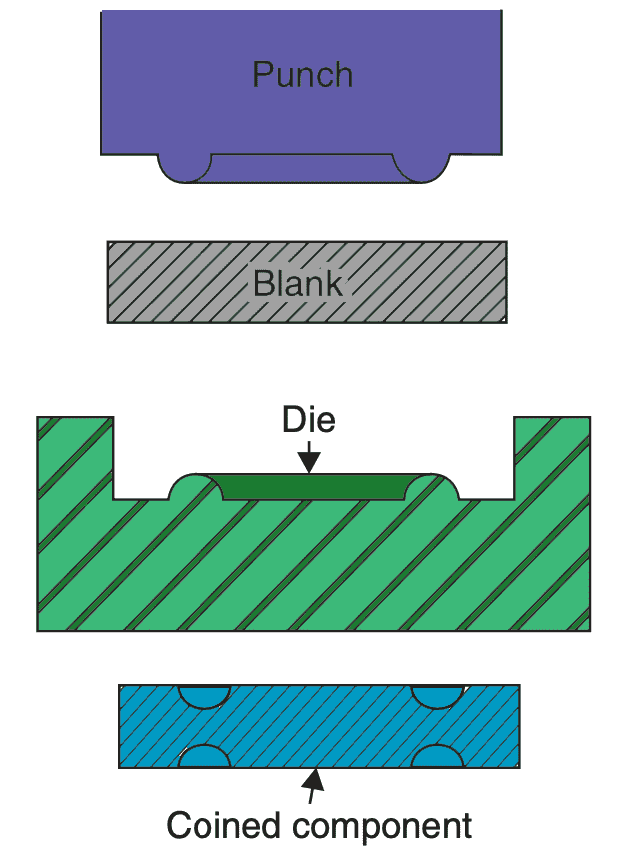
- The result of the coining operation is that the design engraved on the top and bottom dies gets imprinted on the corresponding faces of the blank in relief (i.e., raised material) without the size of the blank-circumference changing.
- Coins used as money in daily usage are manufactured in this manner.
- Here forces required are much higher, enough to cause plastic flow of material.
Embossing
In embossing, impressions are made on sheet metal in such a manner that the thickness of the sheet remains uniform all over even after embossing has been done. It means that if one side of the sheet is raised to form a design, there is a corresponding depression on the other side of the sheet. Basically, it is a pressing operation where not much force is needed. The Embossing process is illustrated in the following figure.
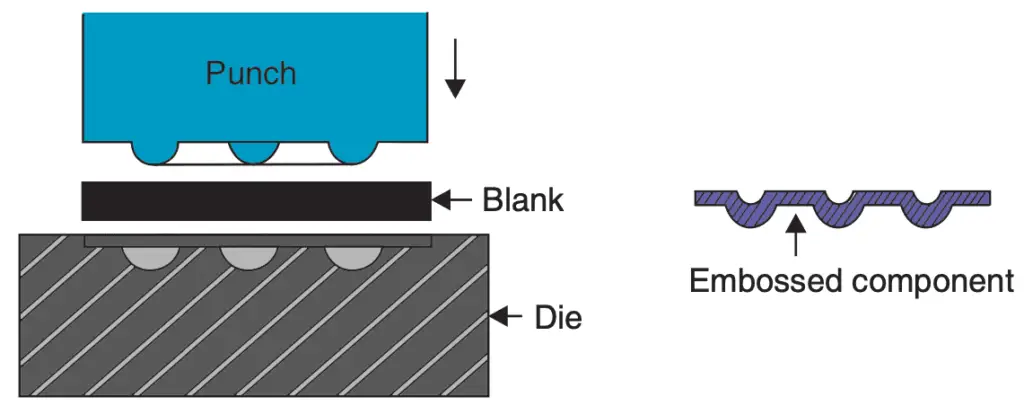
The sheet is spread on the bottom die and the stroke of the punch is so adjusted that, when it moves down to its lowest position, it leaves a uniform clearance between the impressions carved in the punch and the die which is equal to the thickness of the sheet being embossed. The design is transferred onto the sheet by bending the sheet up or down without altering its thickness anywhere. Many decoration pieces with religious motifs are made in this way.
Conclusion
We have discussed the different operations that can be performed with the Mechanical presses. And there are many other operations out there that are not mentioned here. Let us know in the comment section if you know any of the other operations that can be performed with the Press that I missed here.
Leave a Reply