The hydraulic machines, which convert the hydraulic energy into mechanical energy, are called turbines while the hydraulic machines which convert mechanical energy into hydraulic energy are called pumps. Hydraulic energy is in the form of pressure energy. If the mechanical energy is converted into pressure energy by means of centrifugal force acting on the fluid, the hydraulic machine is called a centrifugal pump. If the mechanical energy is converted into hydraulic energy (or pressure energy) by sucking the liquid into a cylinder in which a piston is reciprocating (moving backwards and forwards), which exerts the thrust on the liquid and increases its hydraulic energy (pressure energy), the pump is known as the reciprocating pump. Let us discuss more details such as the main components, the working principle of the Reciprocating Pump and the different types in it.
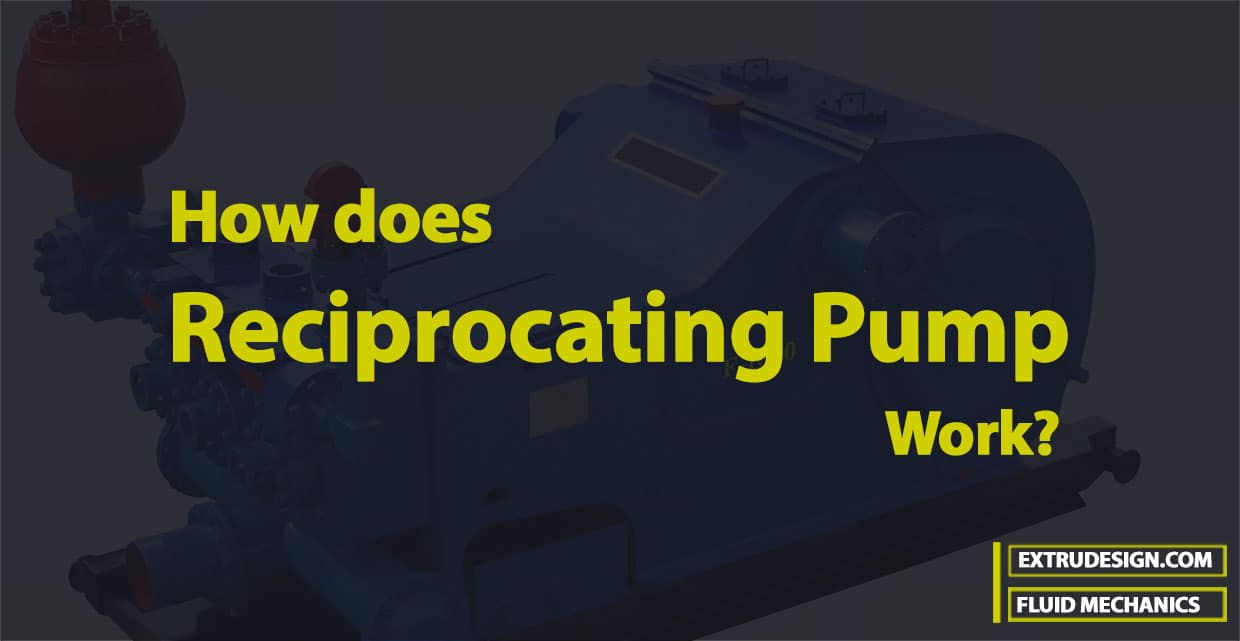
The following schematic represents all the main parts of a reciprocating pump.
- A cylinder with a piston, piston rod, connecting rod and a crank.
- Suction pipe
- Delivery pipe
- Suction valve
- Delivery valve
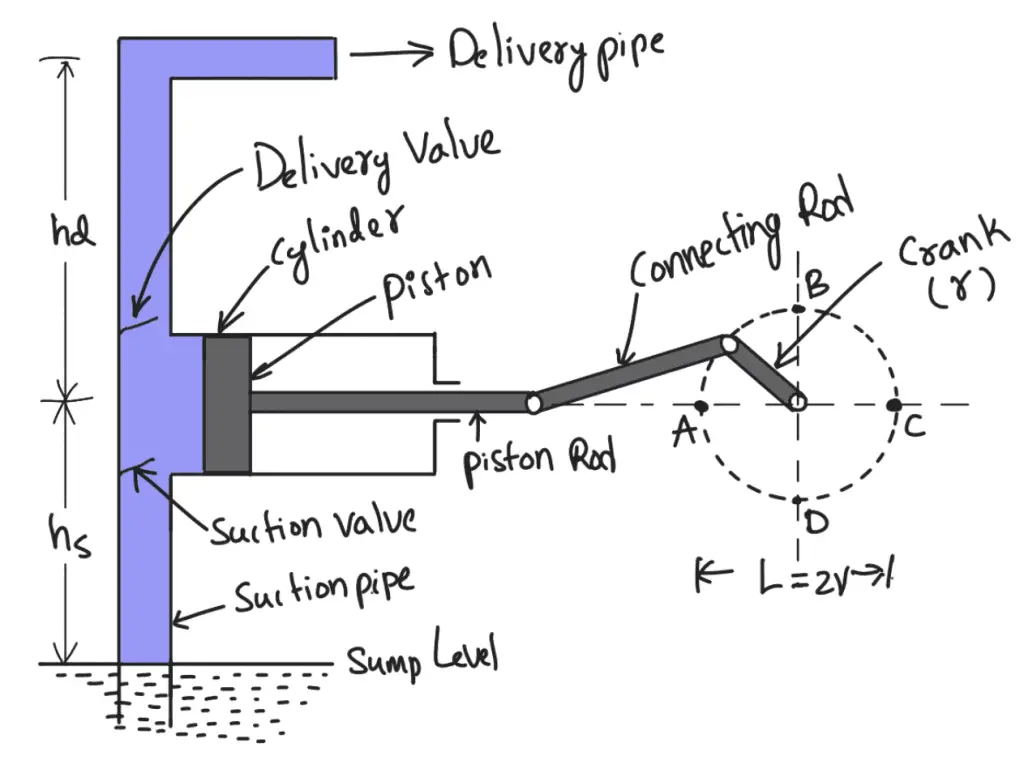
Working of A Reciprocating Pump
The above schematic diagram shows a single-acting reciprocating pump, which consists of a piston which moves forwards and backwards in a close-fitting cylinder. The movement of the piston is obtained by connecting the piston rod to the crank by means of a connecting rod.
- The crank is rotated by means of an electric motor.
- Suction and delivery pipes with suction valve and delivery valve are connected to the cylinder.
- The suction and delivery valves are one-way valves or non-return valves, which allow the water to flow in one direction only.
- The suction valve allows water from the suction pipe to the cylinder which the delivery valve allows water from the cylinder to the delivery pipe only.
- When the crank starts rotating, the piston moves to and fro in the cylinder.
- When the crank is at A, the piston is at the extreme left position in the cylinder.
- As the crank is rotating from A to C, (i.e., from θ = 0° to θ = 180°), the piston is moving towards the right in the cylinder.
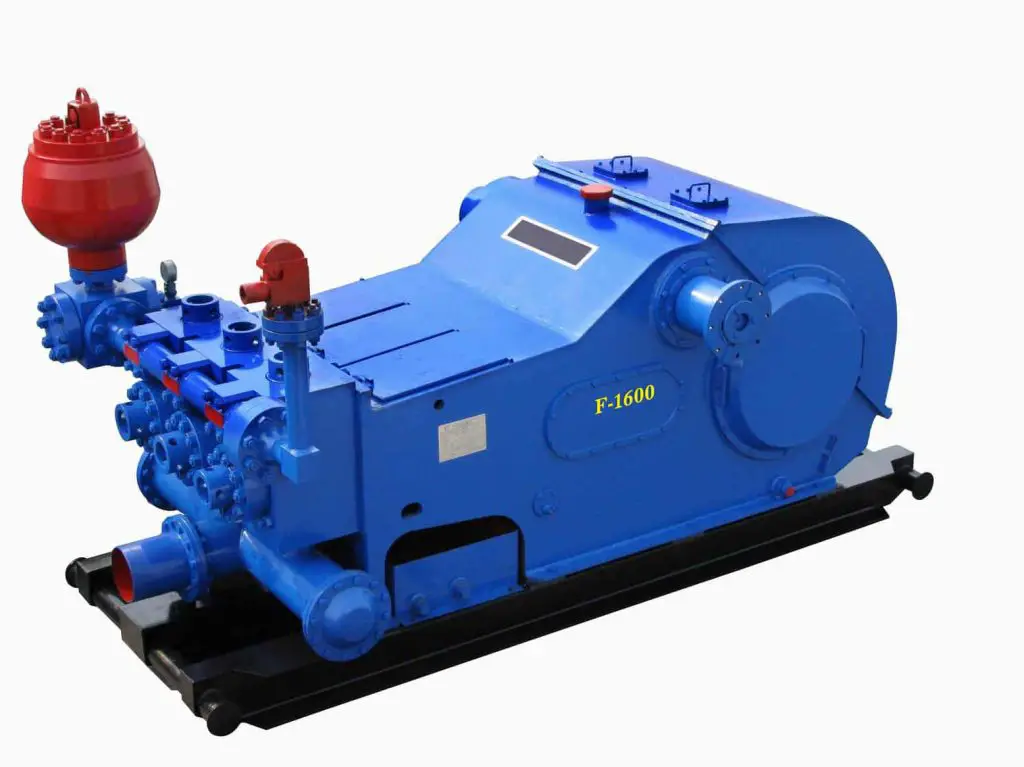
- The movement of the piston towards the right creates a partial vacuum in the cylinder.
- But on the surface of the liquid in the sump atmospheric pressure is acting, which is more than the pressure inside the cylinder.
- Thus, the liquid is forced in the suction pipe from the sump. This liquid opens the suction valve and enters the cylinder.
- When the crank is rotating from C to A (i.e., from θ = 180° to θ = 360°), the piston from its extreme right position starts moving towards left in the cylinder.
- The movement of the piston towards the left increases the pressure of the liquid inside the cylinder more than atmospheric pressure.
- Hence suction valve closes and the delivery valve opens. The liquid is forced into the delivery pipe and is raised to the required height.
Classification Of Reciprocating Pumps
The reciprocating pumps may be classified as :
- According to the water being in contact with one side or both sides of the piston, and
- According to the number of cylinders provided.
If the water is in contact with one side of the piston, the pump is known as single-acting. On the other hand, if the water is in contact with both sides of the piston, the pump is called double-acting.
Hence, classification according to the contact of water is:
- (i) Single-acting pump
- (ii) Double-acting pump
According to the number of cylinders provided, the pumps are classified as :
- (i) Single-cylinder pump
- (ii) Double-cylinder pump
- (iii) Triple-cylinder pump
This is all about the Reciprocating Pump. Let us know what you think about this article in the comment section below. Check out the Comparison of the Reciprocating Pump with the Centrifugal pump.
Leave a Reply